The company which built the Haut Fourneau B integrated iron and steelworks dates back 1809. Over the following century there were various mergers and takeovers with other local and regional producers.
By 1914 the company was one of the primary metal producers in Belgium, operating 8 blast furnaces with a steel production capacity of 500,000 tonnes per year, and producing semi and finished products such as bar, plate, beams and rails.
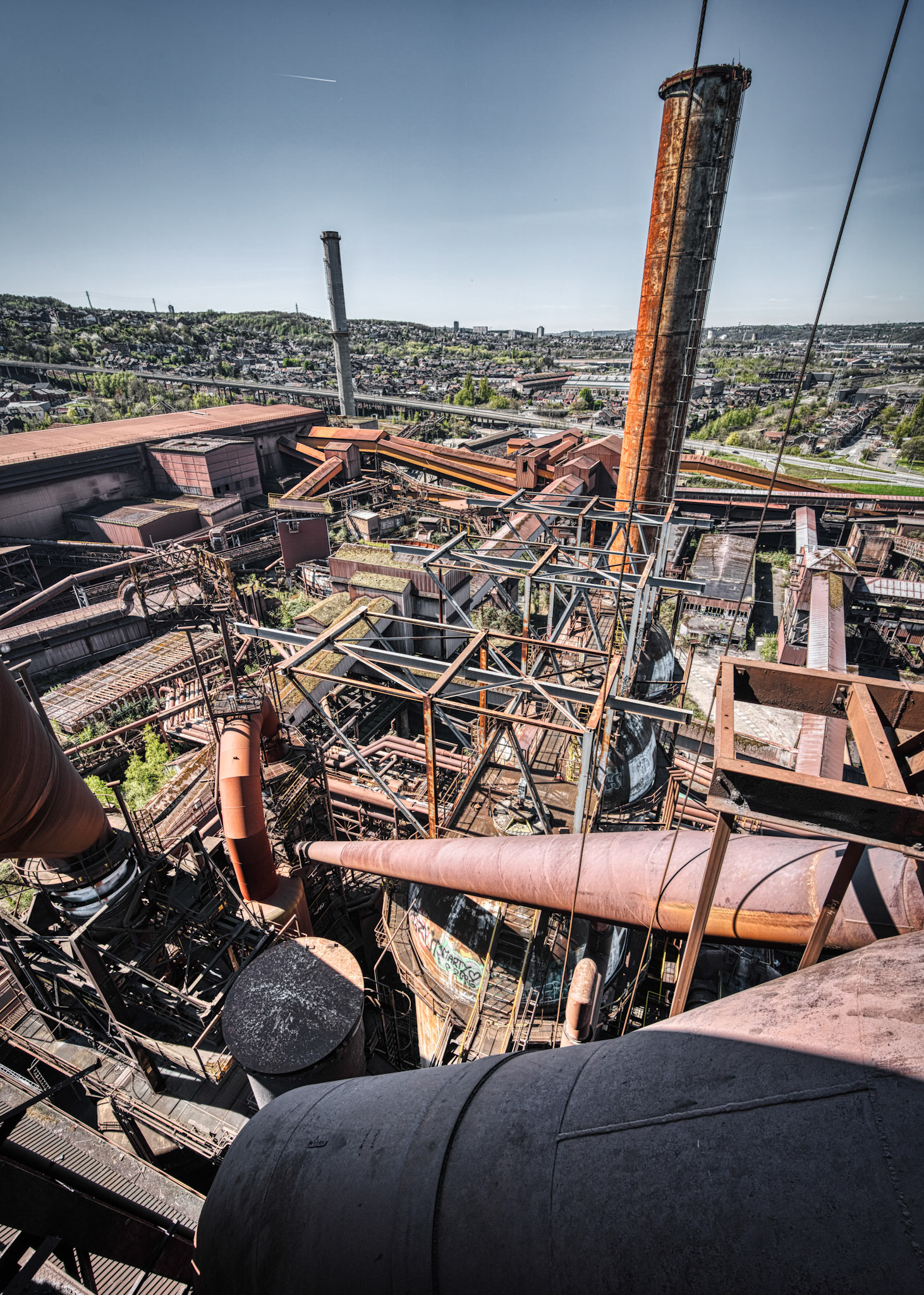
In 2011 all liquid steel production in the ArcelorMittal Liege division was ended, resulting in protests, strikes, and the temporary abduction of several ArcellorMittal executives as protest against the closure.
The company cited overcapacity, and uncompetitiveness as reasons for the closure, but a report commissioned by trade unions contradicted these claims and alleged that ArcelorMittal’s reports used biased accounting methodology.
Trade Union officials called for the Liege steel industry to be taken out of ArcellorMittal’s ownership to protect it, but this never happened and the site still sits unused and decaying to this day.
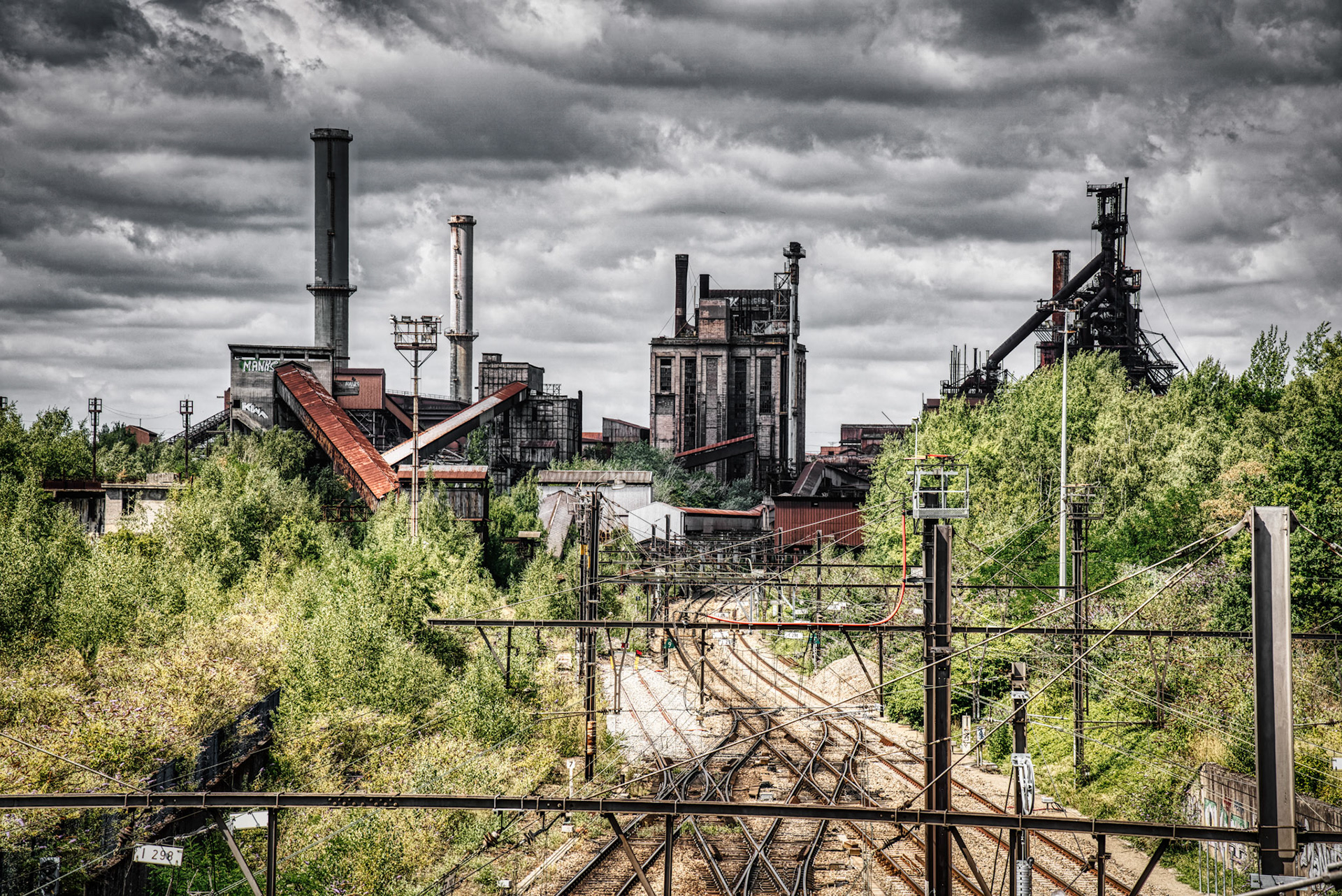
The site itself is enormous. Various buildings, hundreds of pipes, stairs, ladders, band conveyors, storage tanks and much more. Easily to get lost. Even after days of exploration, there's always something more to see.
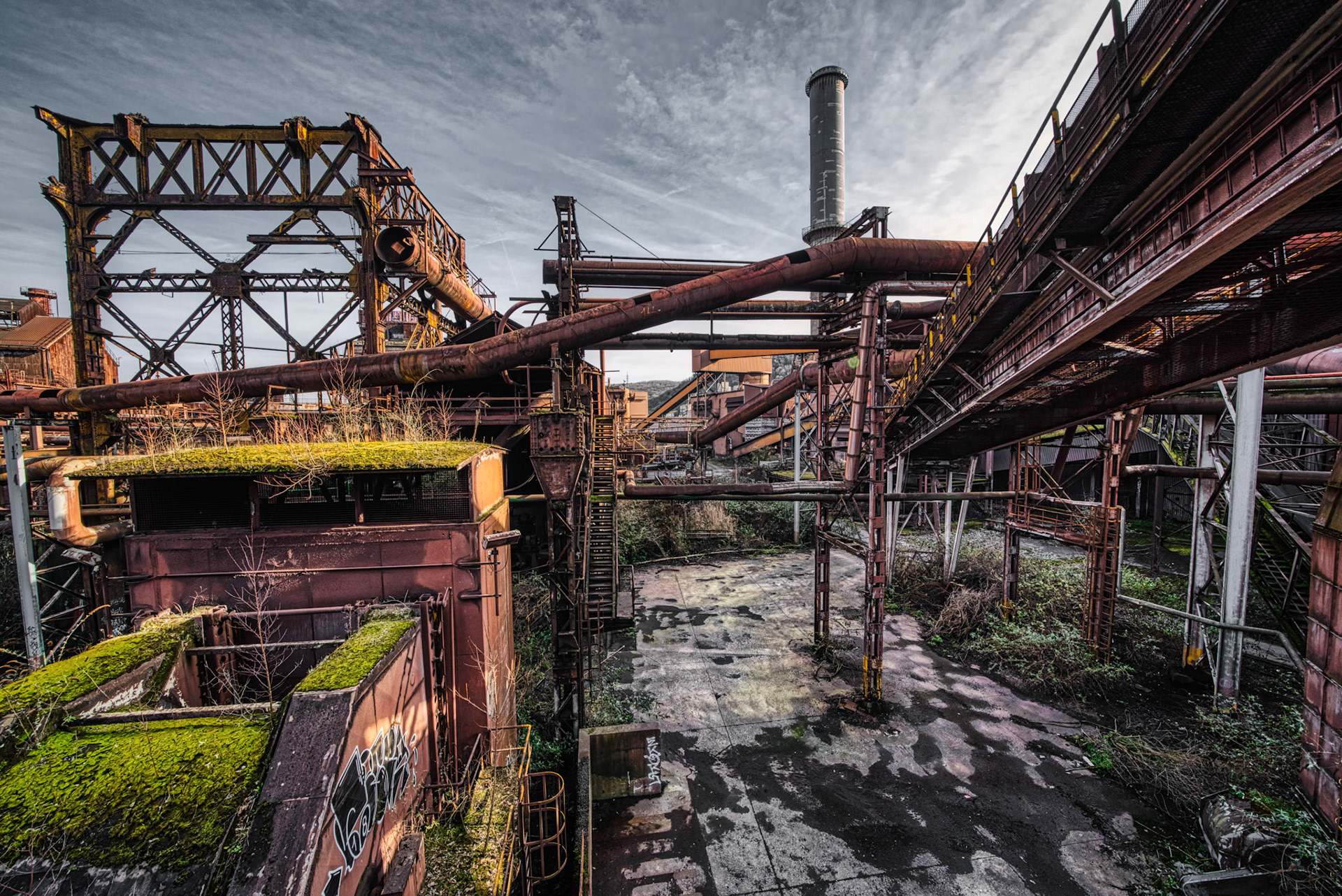
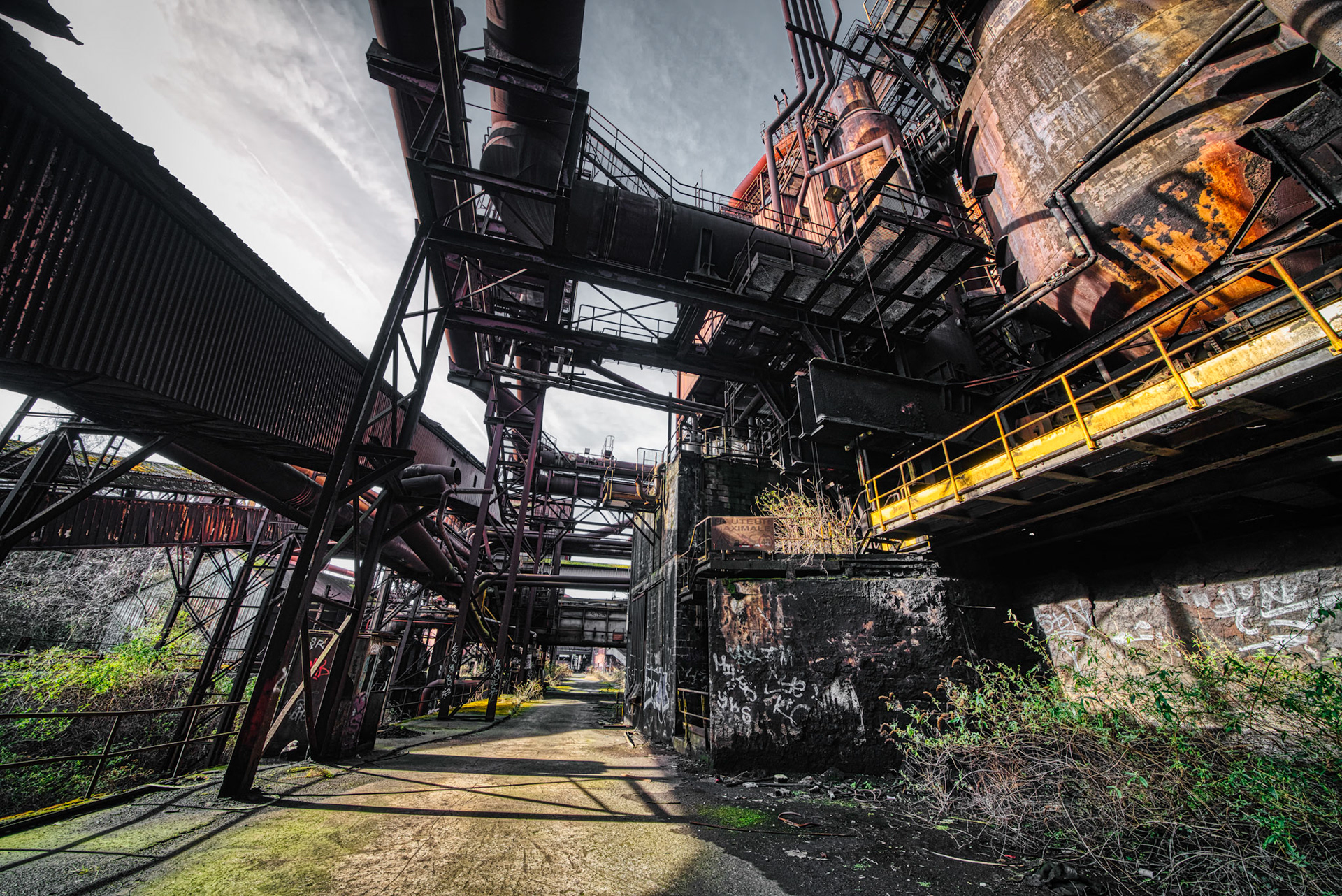
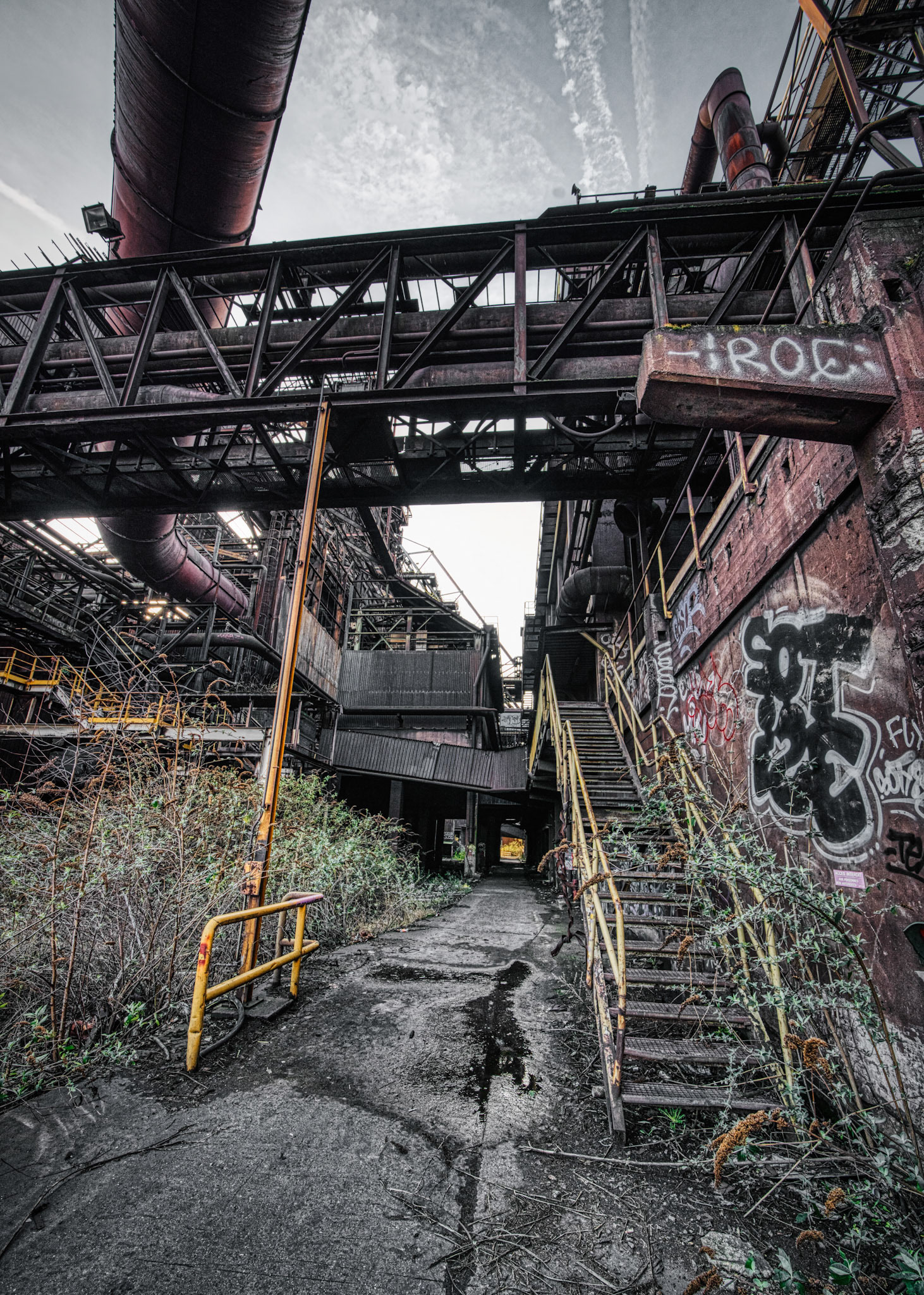
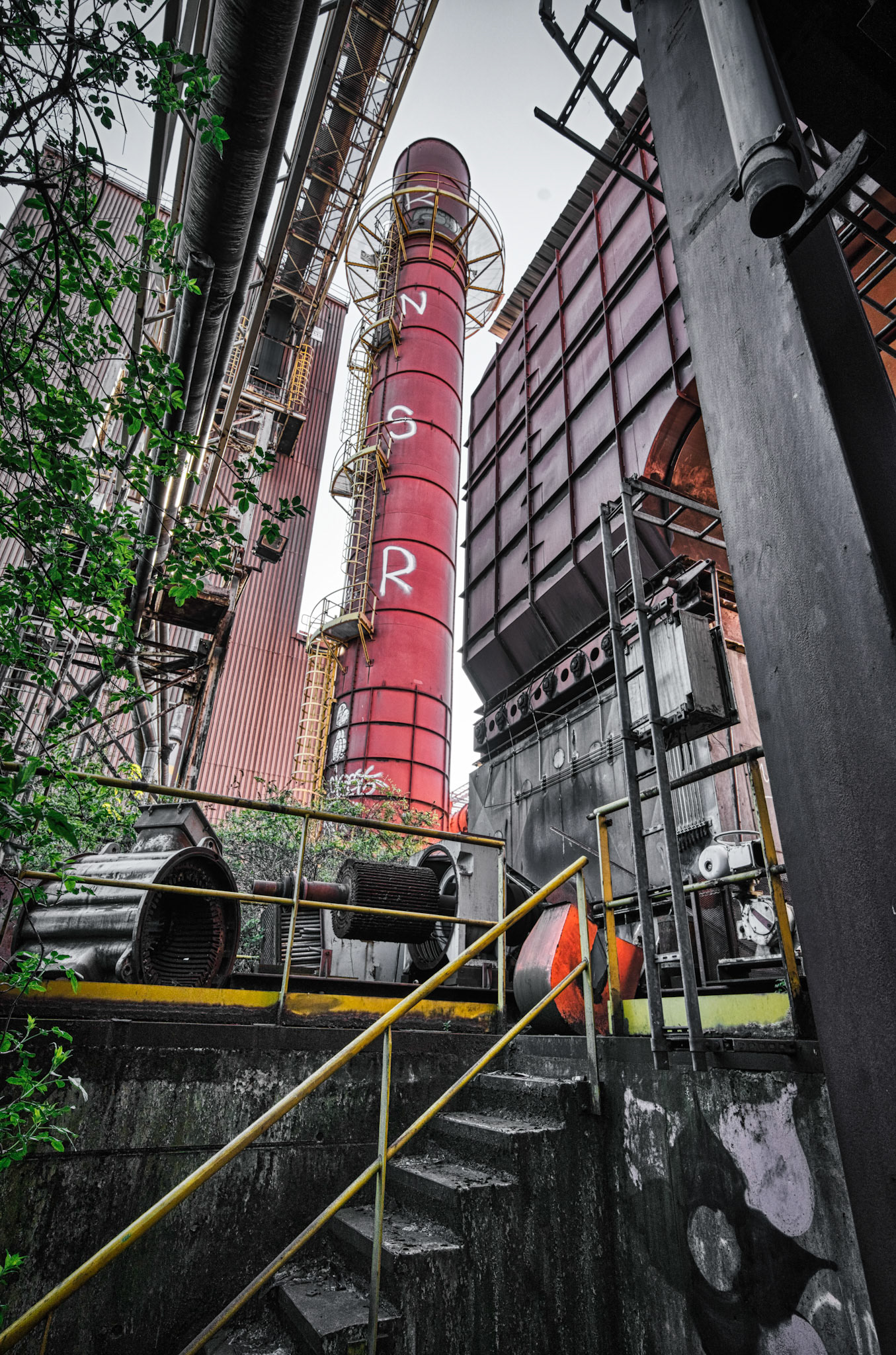
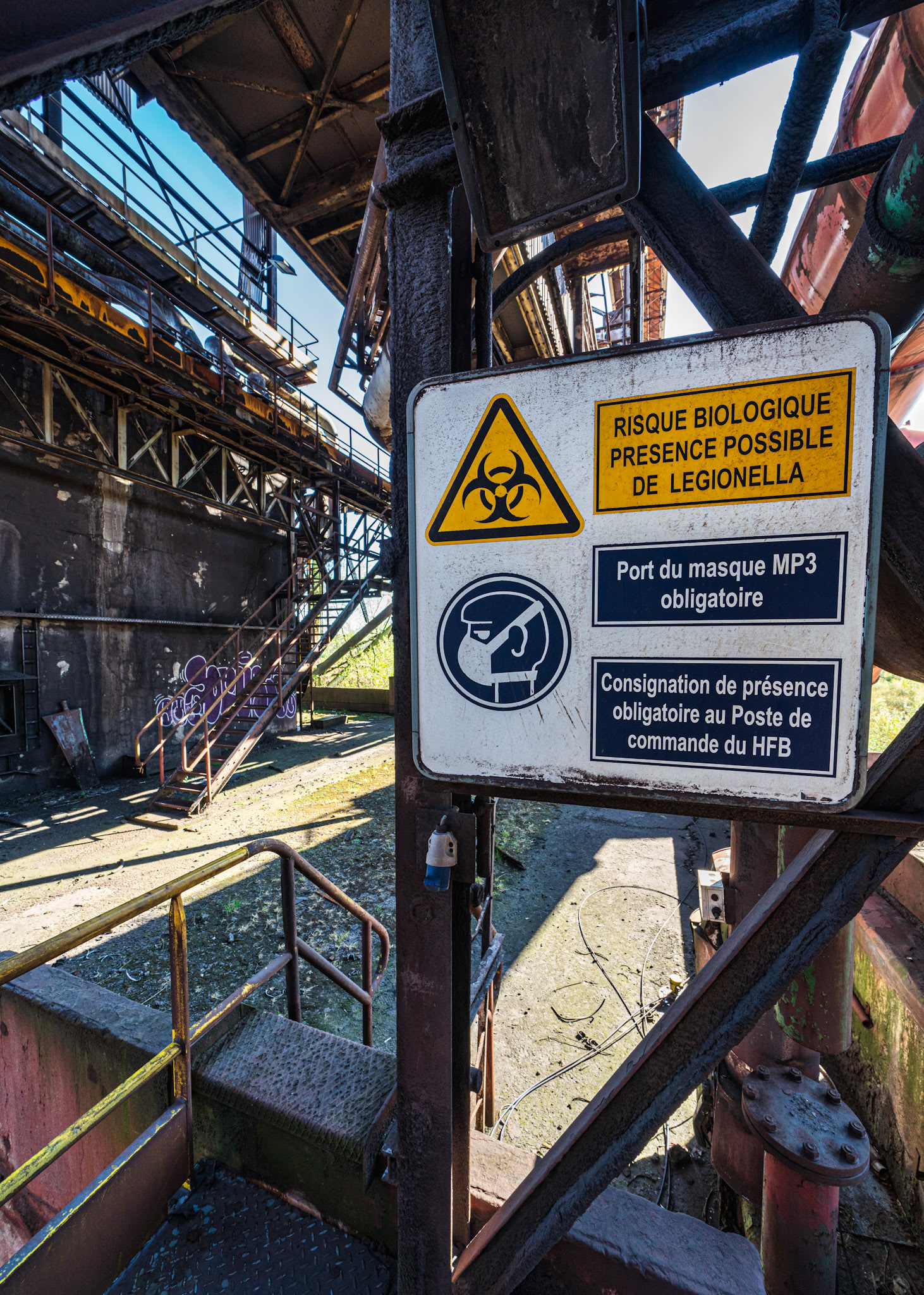
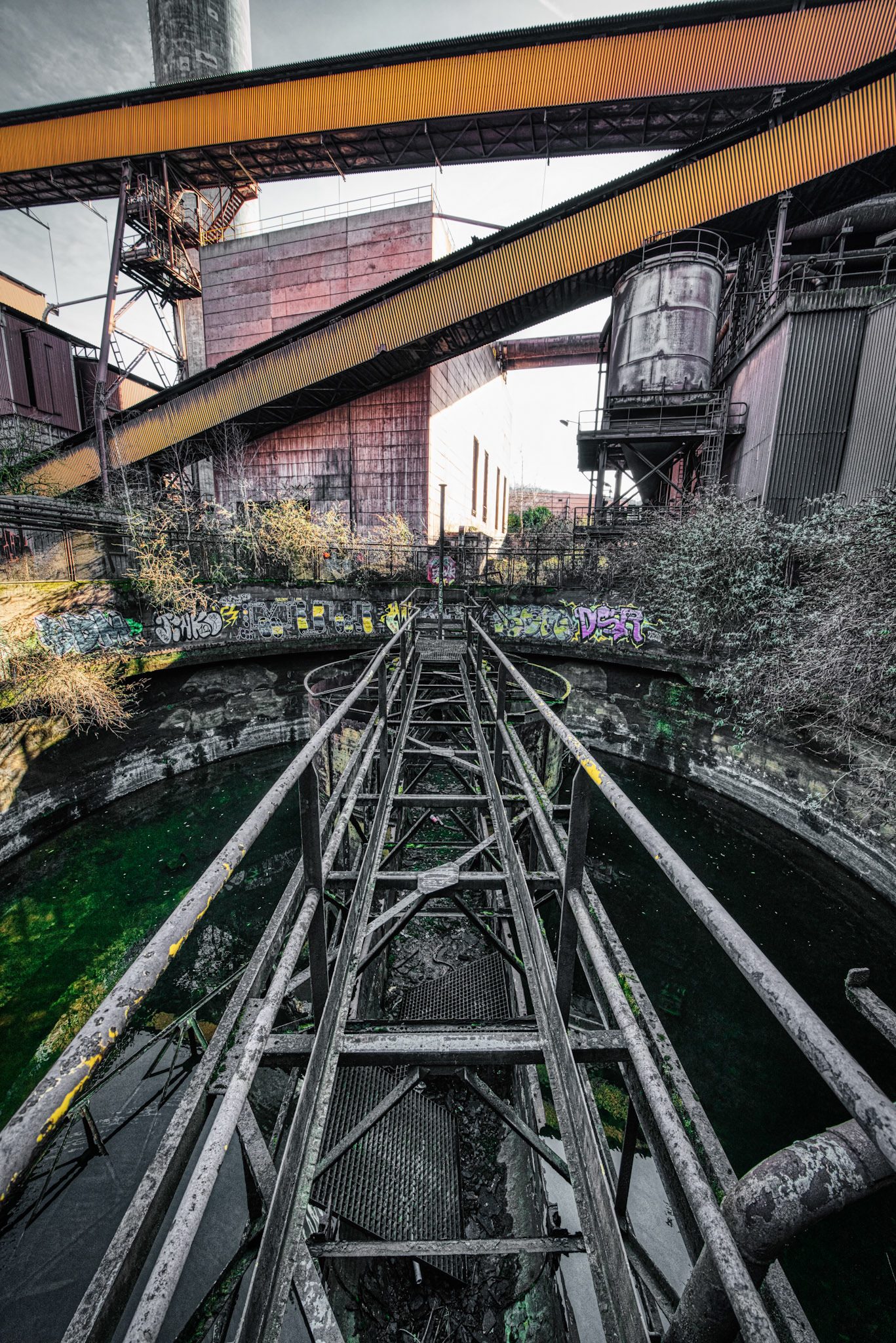

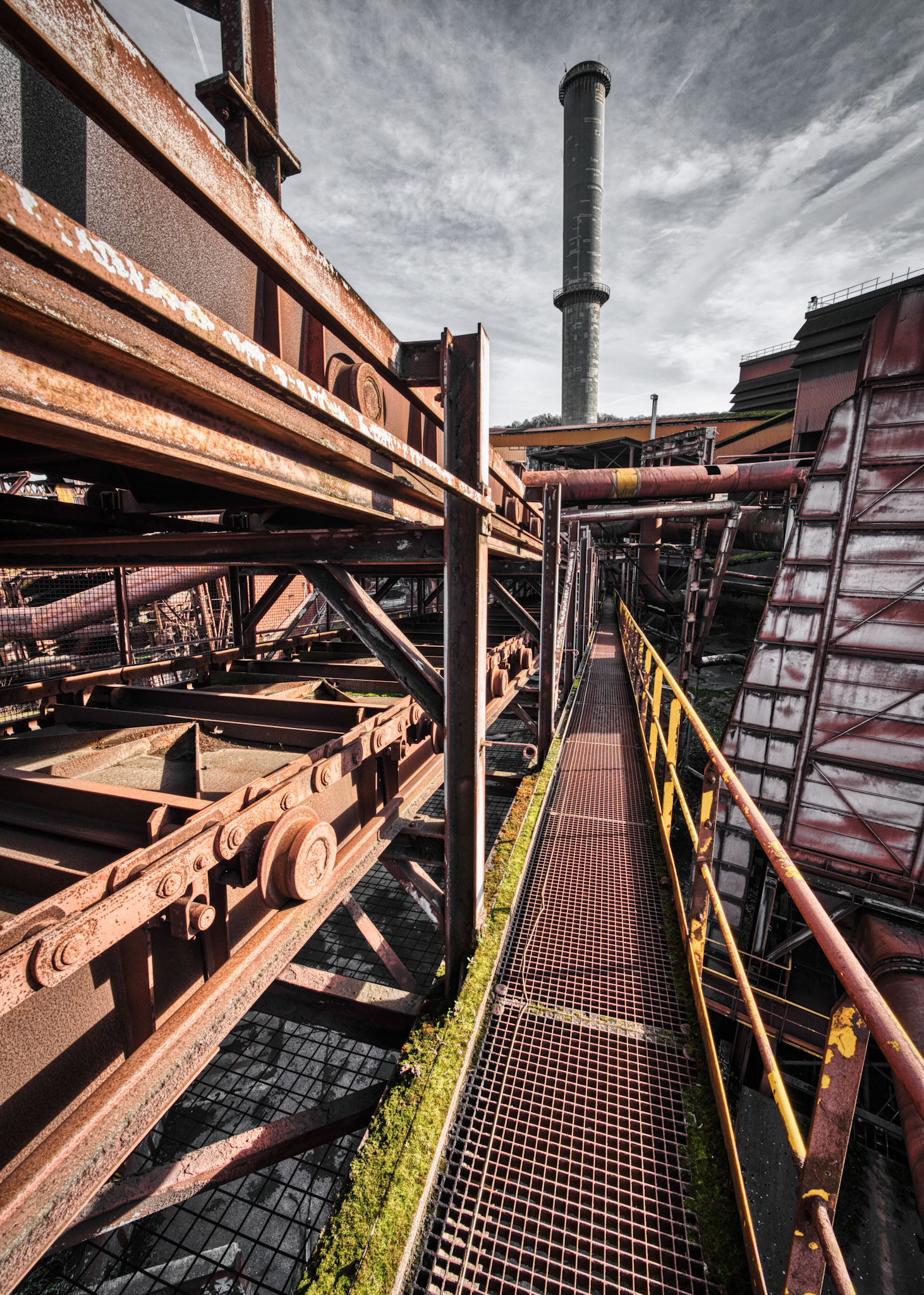
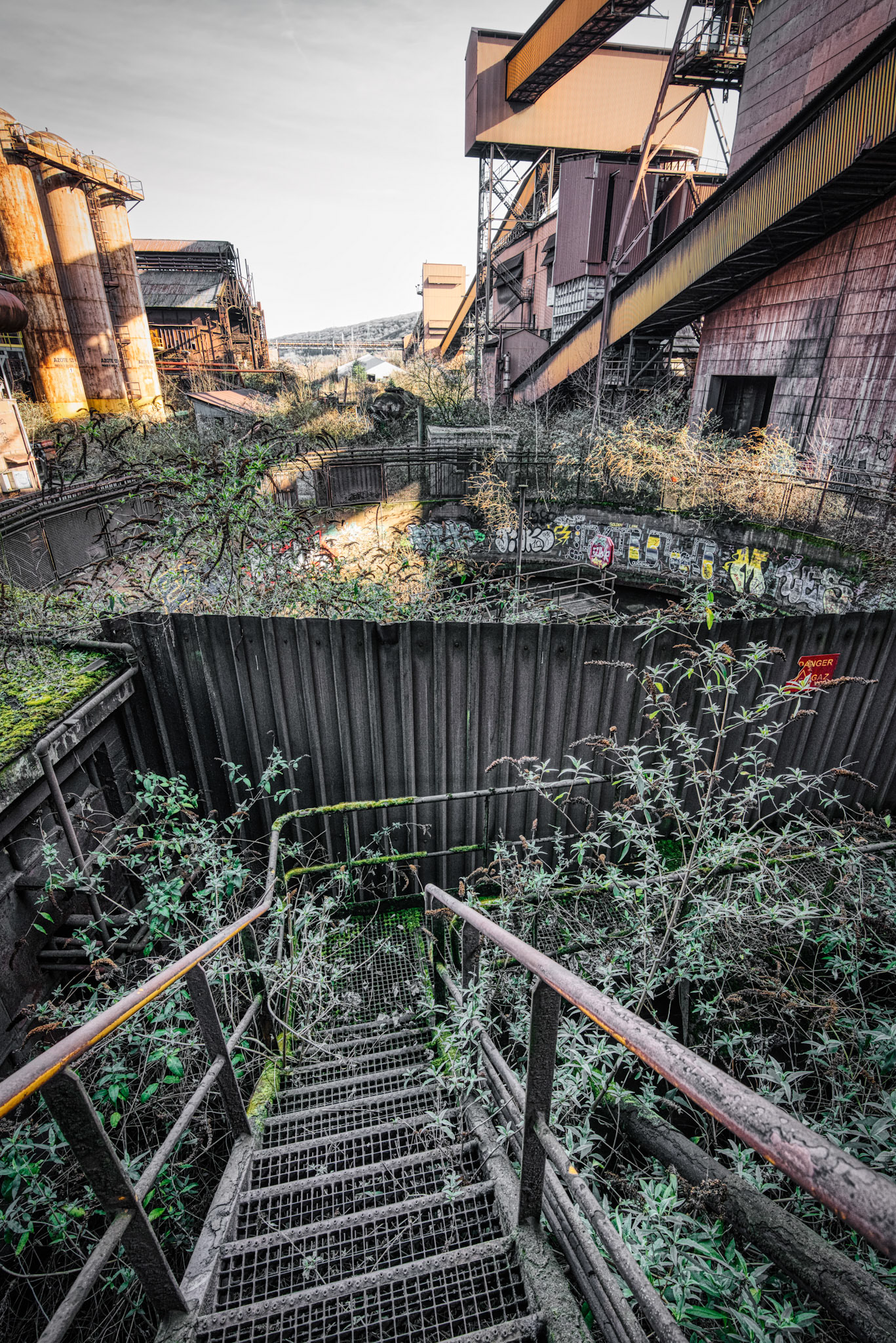
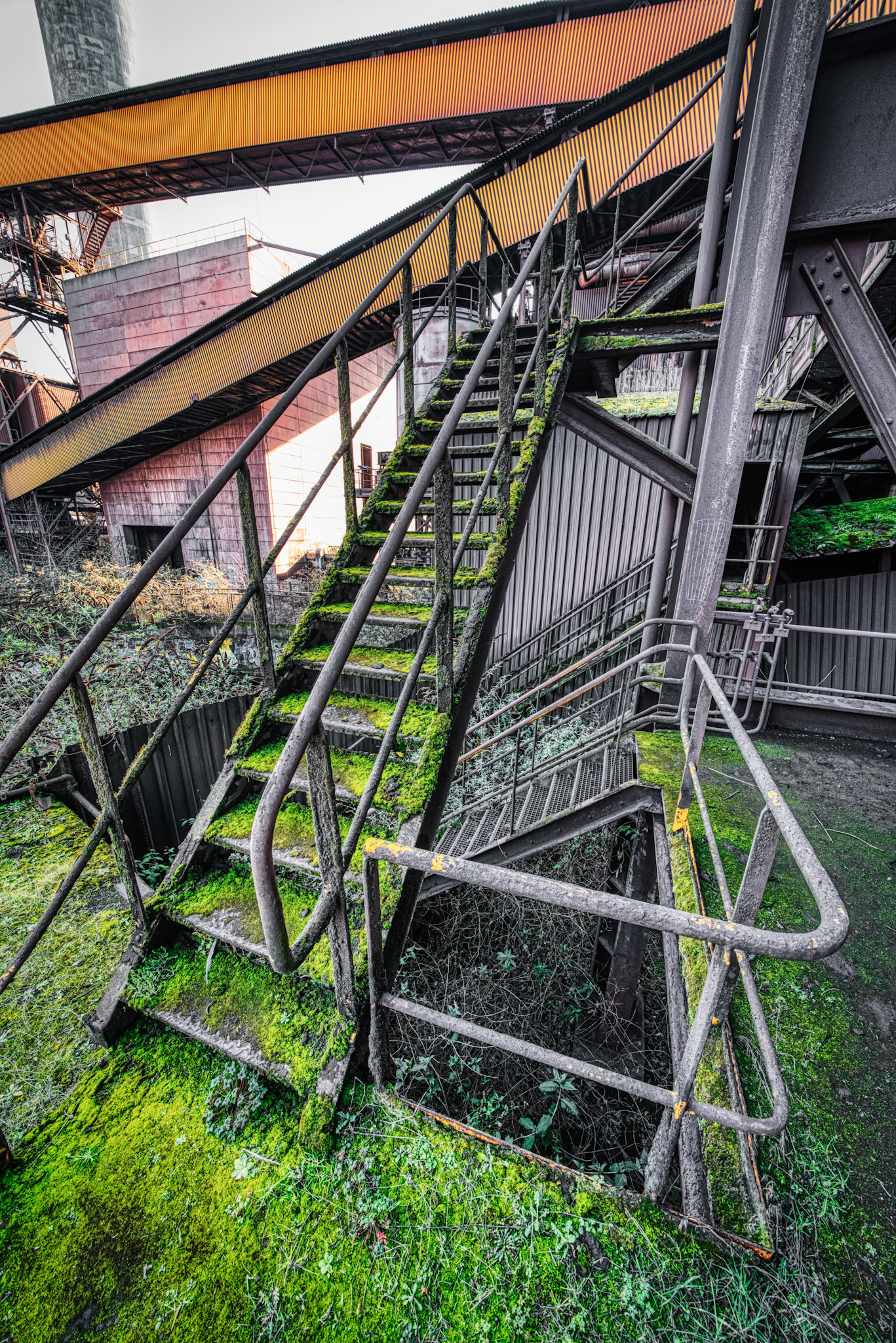
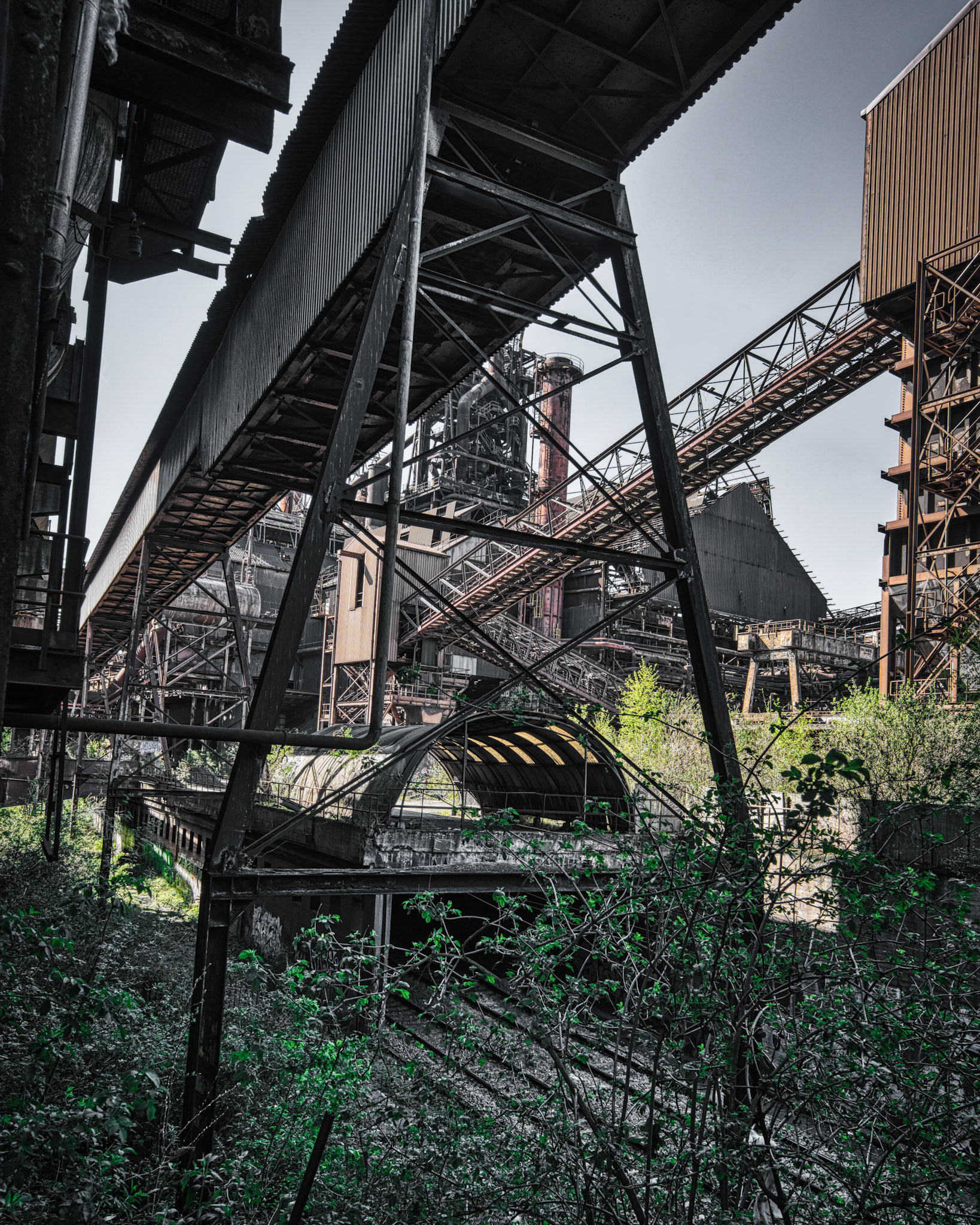
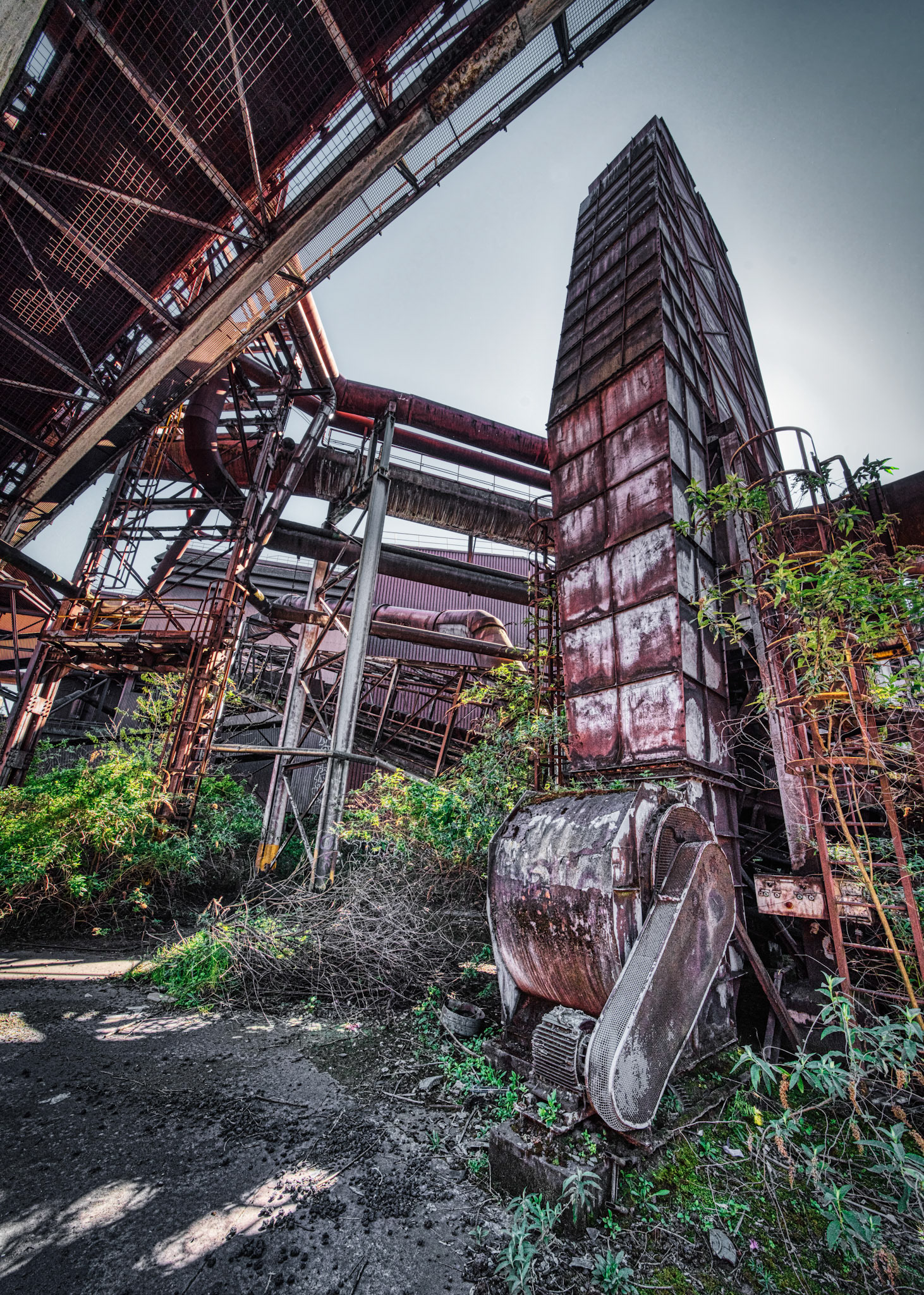
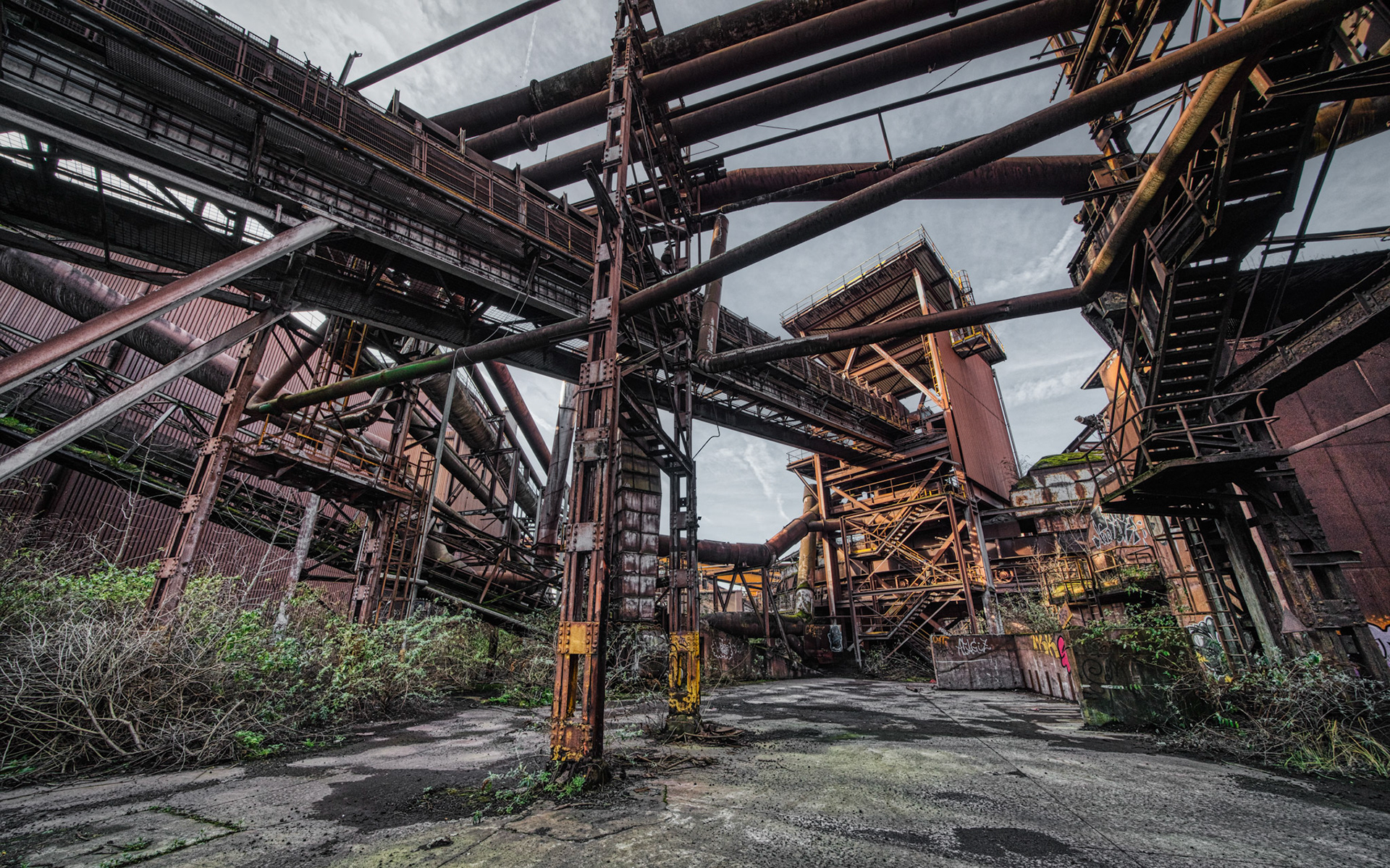
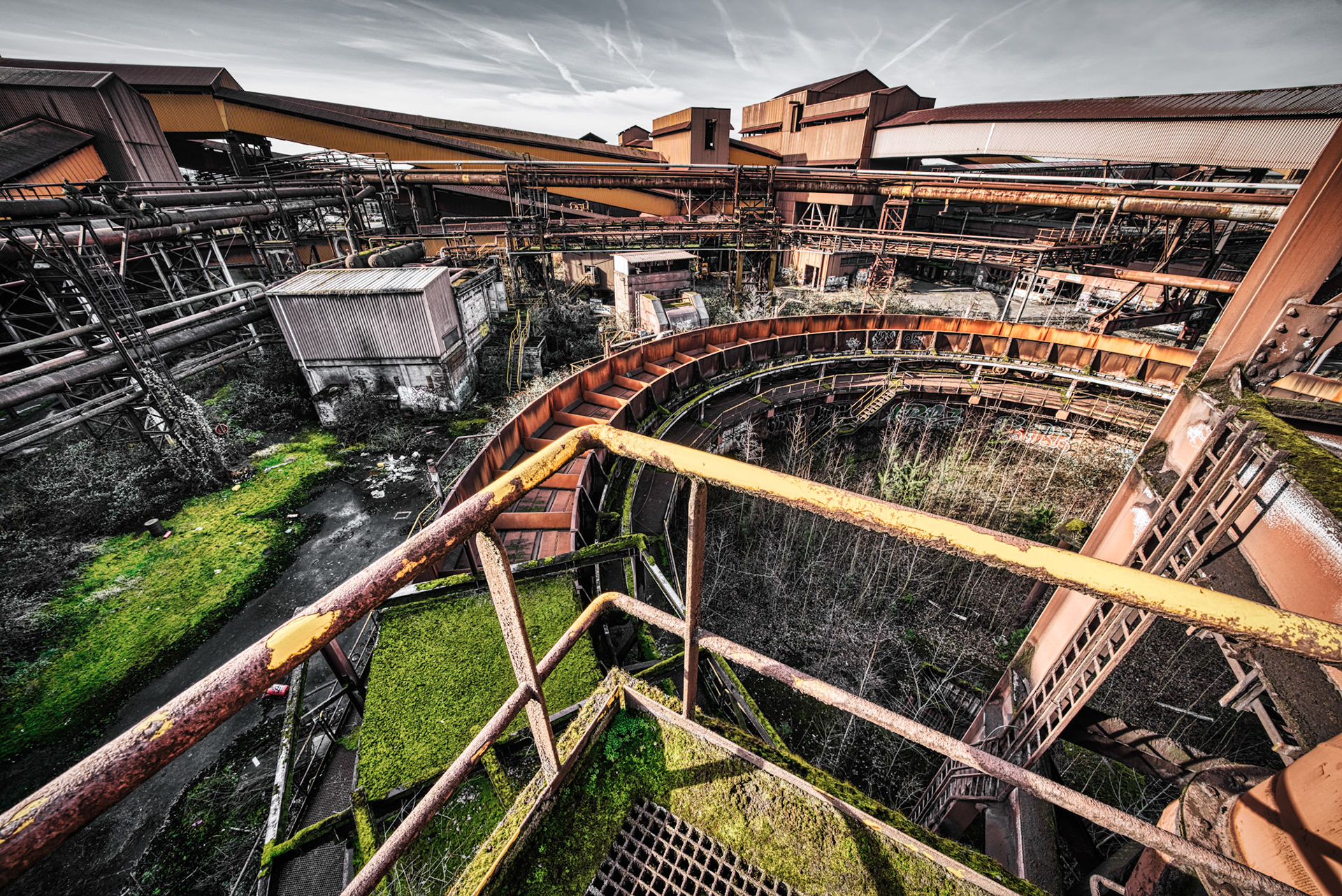
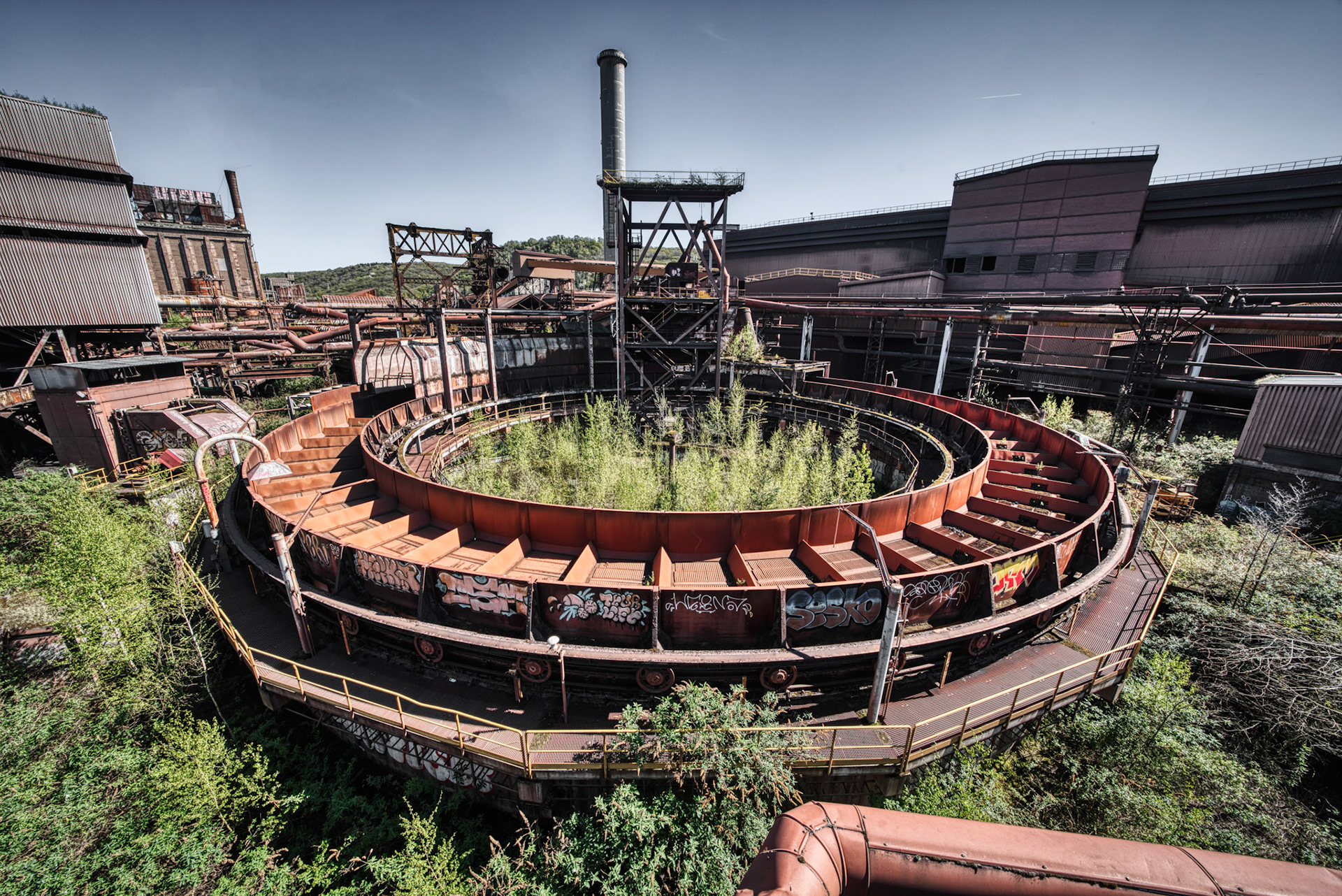
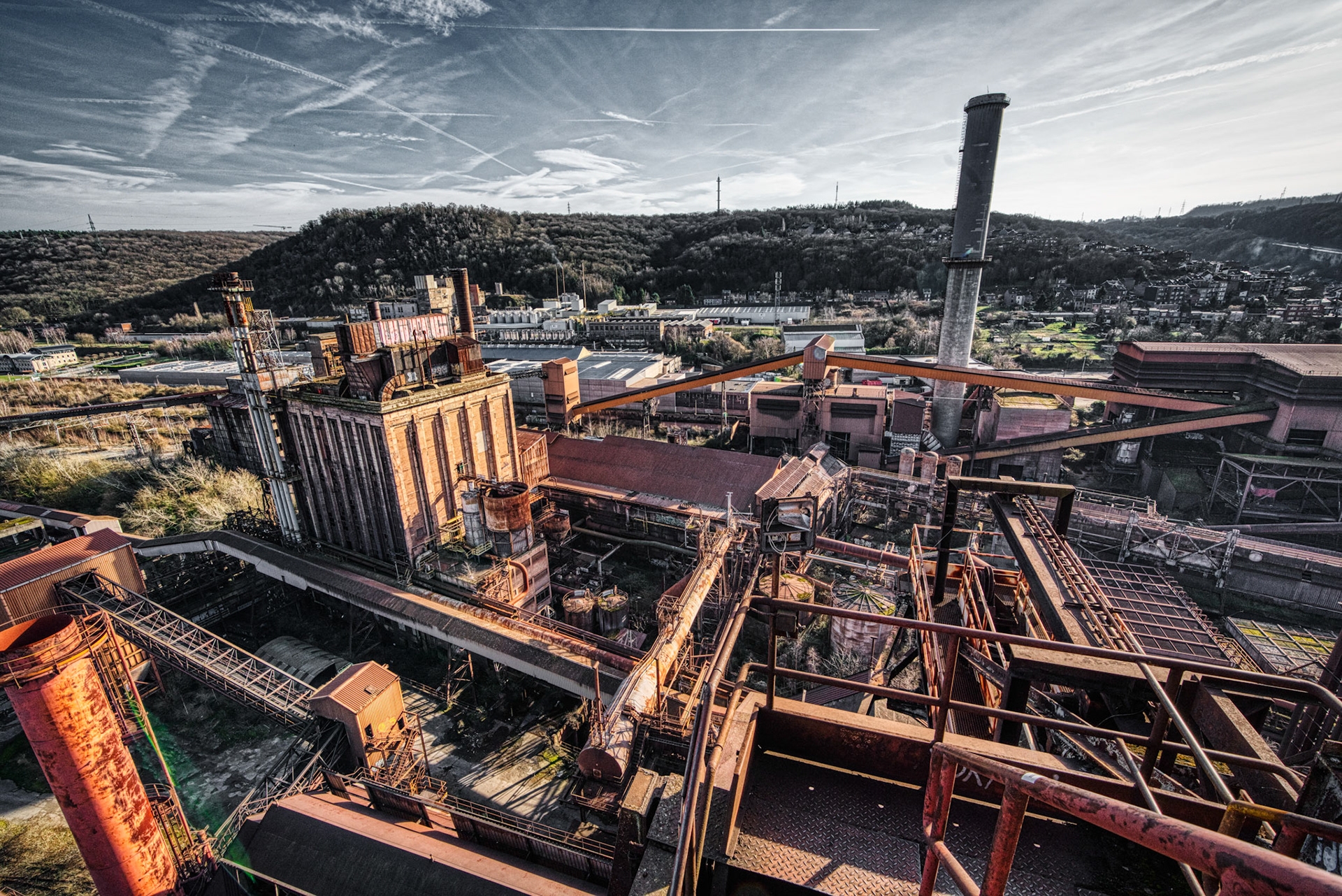
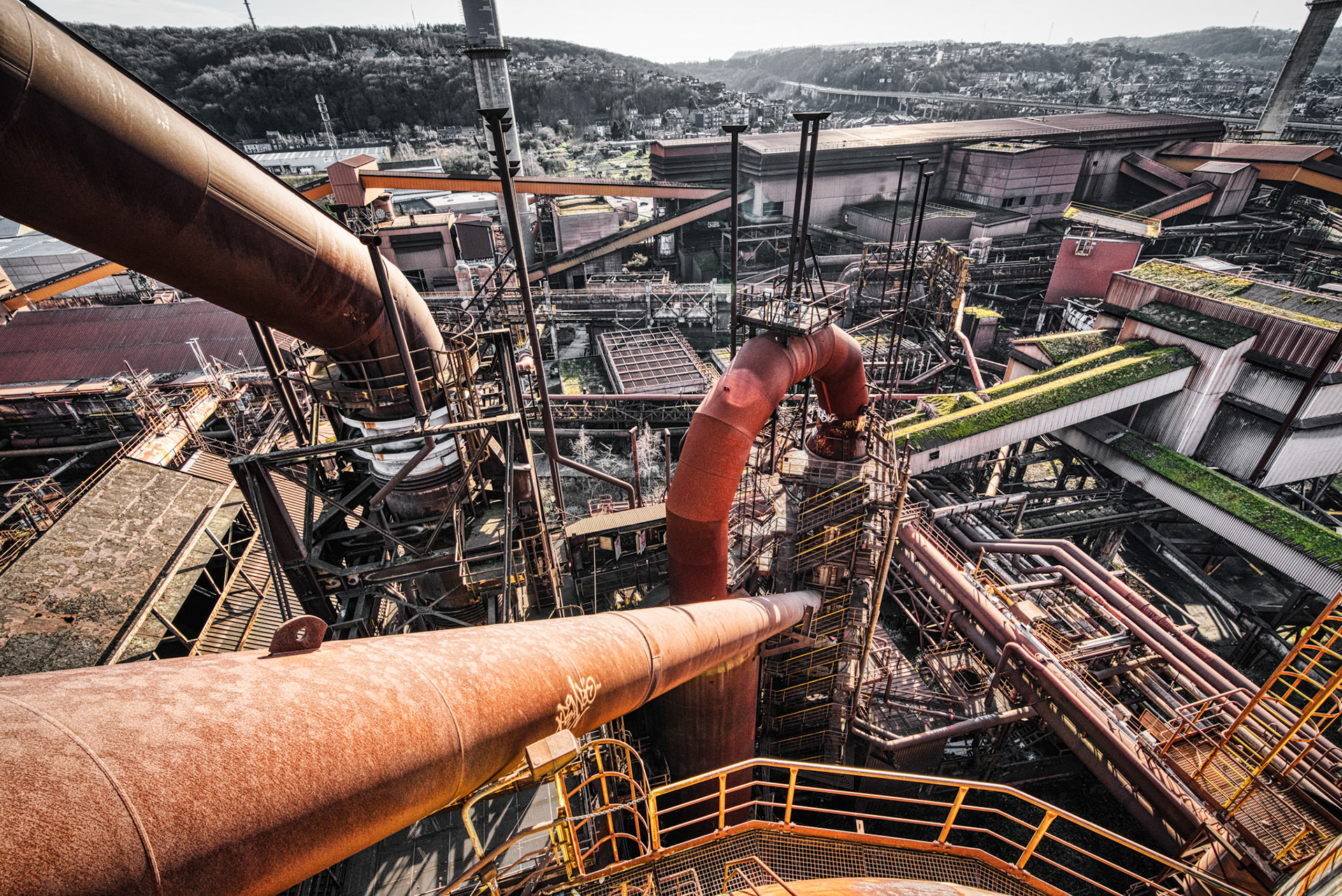
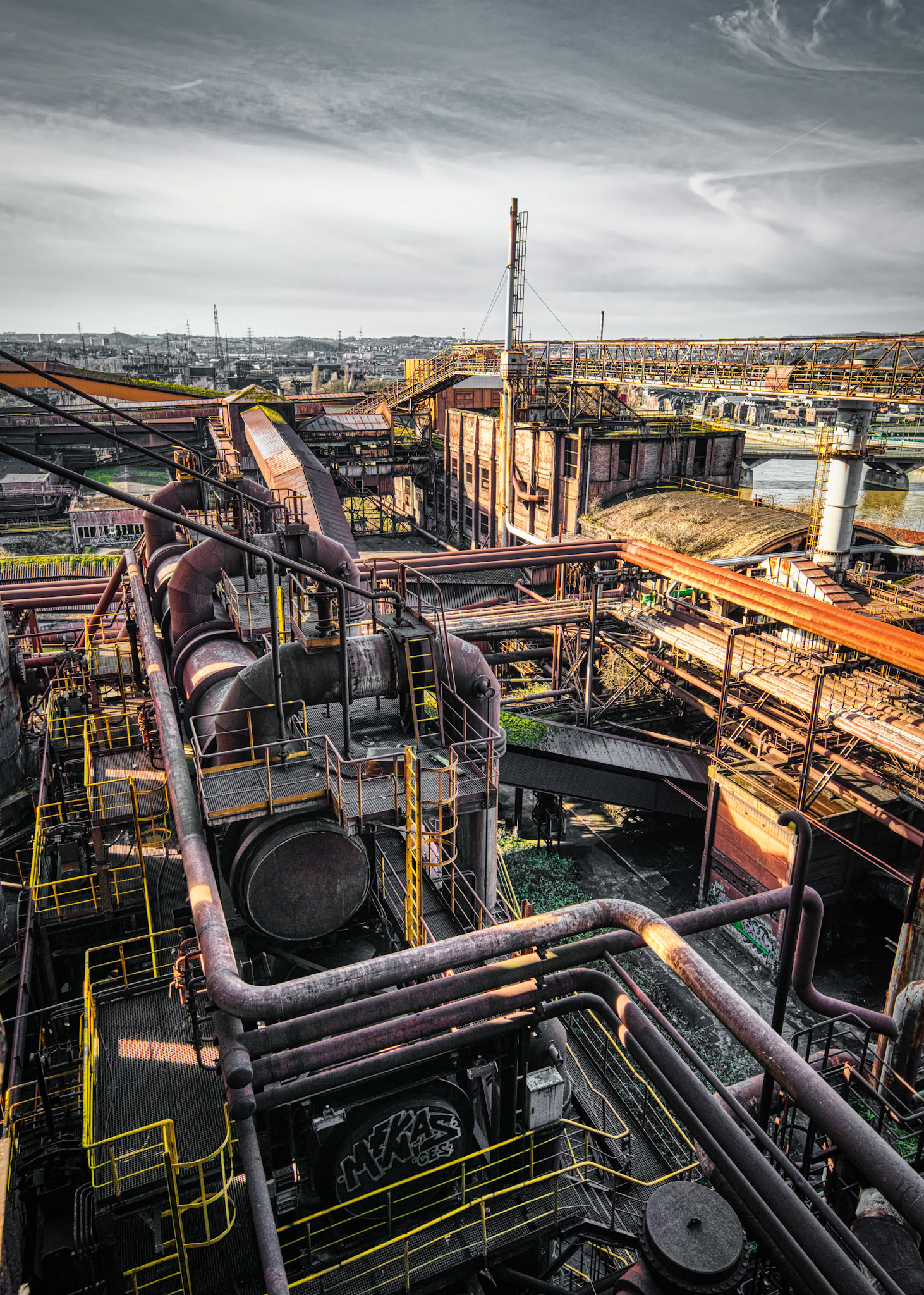
Blast Furnace
In the blast furnace, liquid pig iron is produced from processed iron ores in a continual smelting process. The blast furnace generates heat of over 2000 degrees Celsius in order to melt iron from the iron ore.
To reach this temperature, coke is used as fuel and the fire inside the furnace is fanned with hot air at 1400 degrees Celsius. Also, limestone is added for the purpose of bonding impurities.
The blast furnace is filled from above in order to build alternating layers of coke and iron ore. The part deeper in the furnace has the highest temperature. The molten iron flows to the bottom with the slag floating on top.
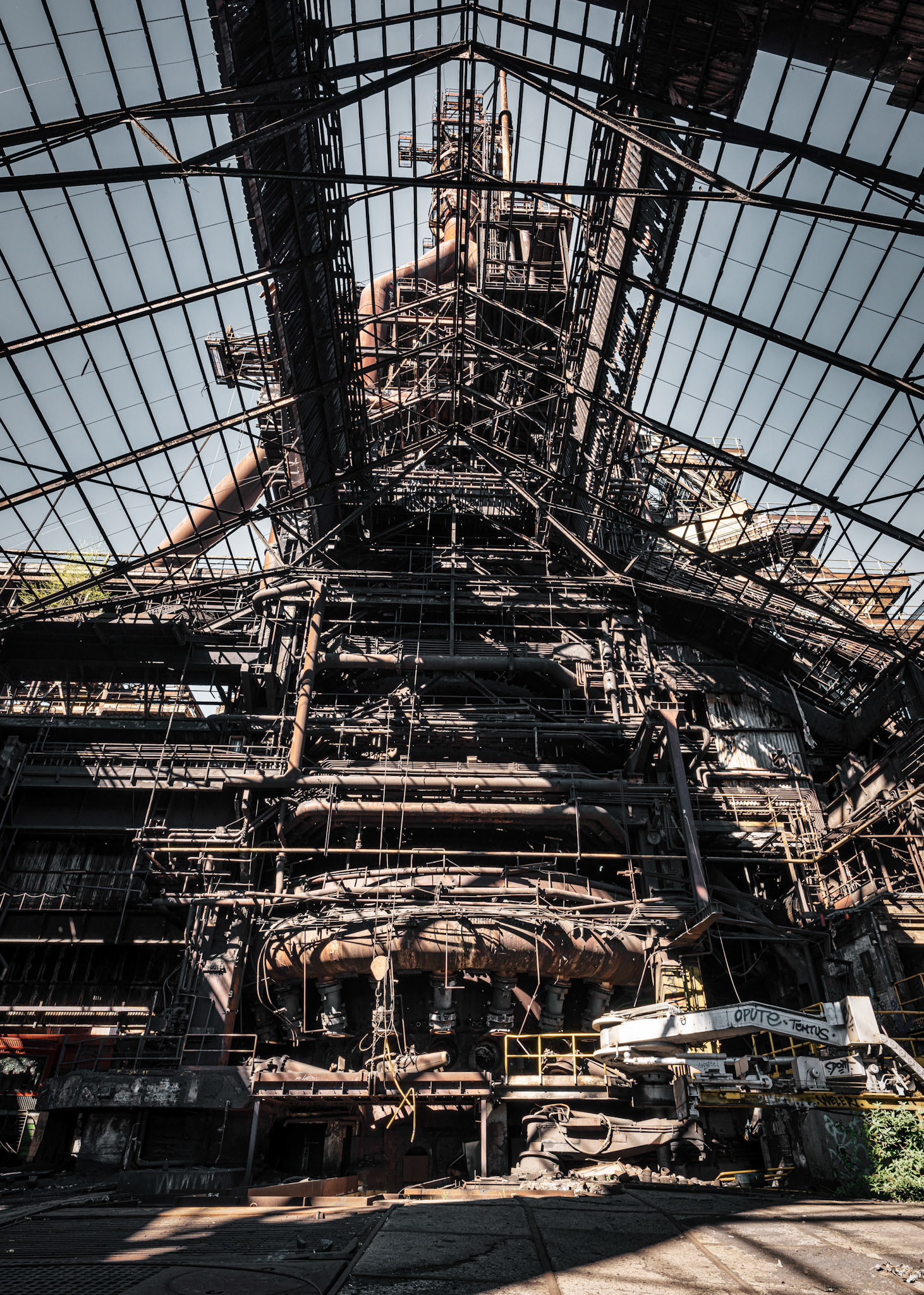
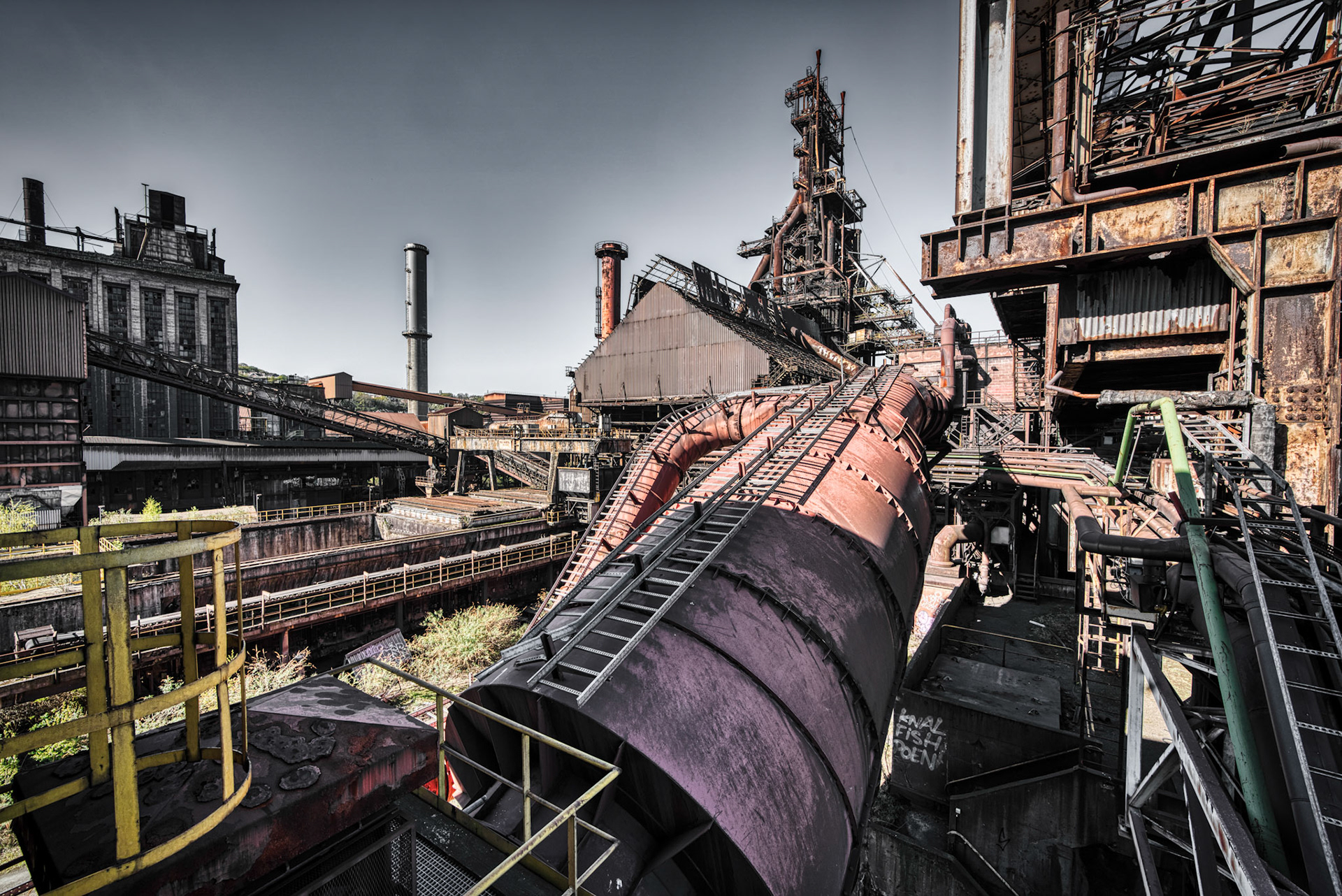
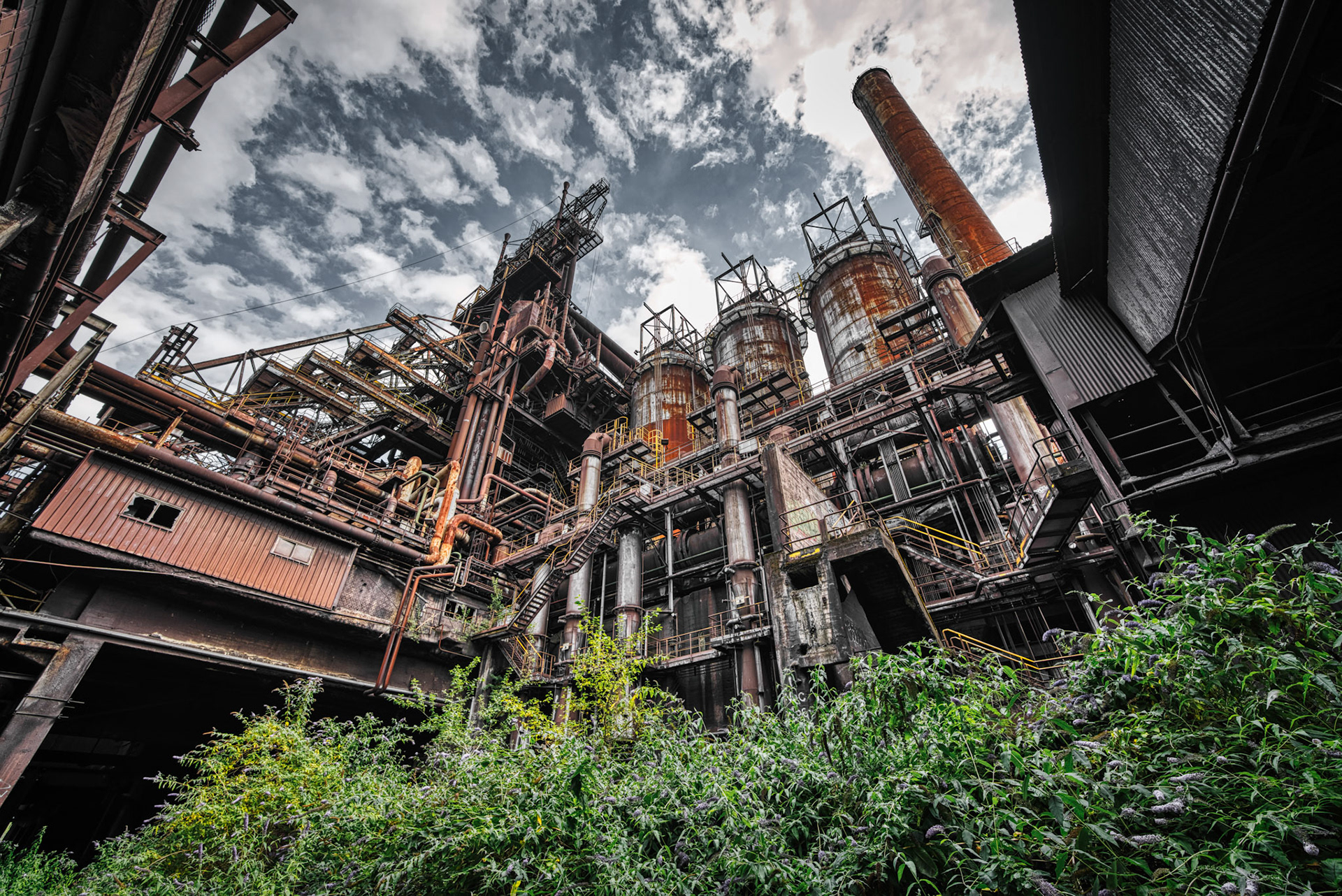
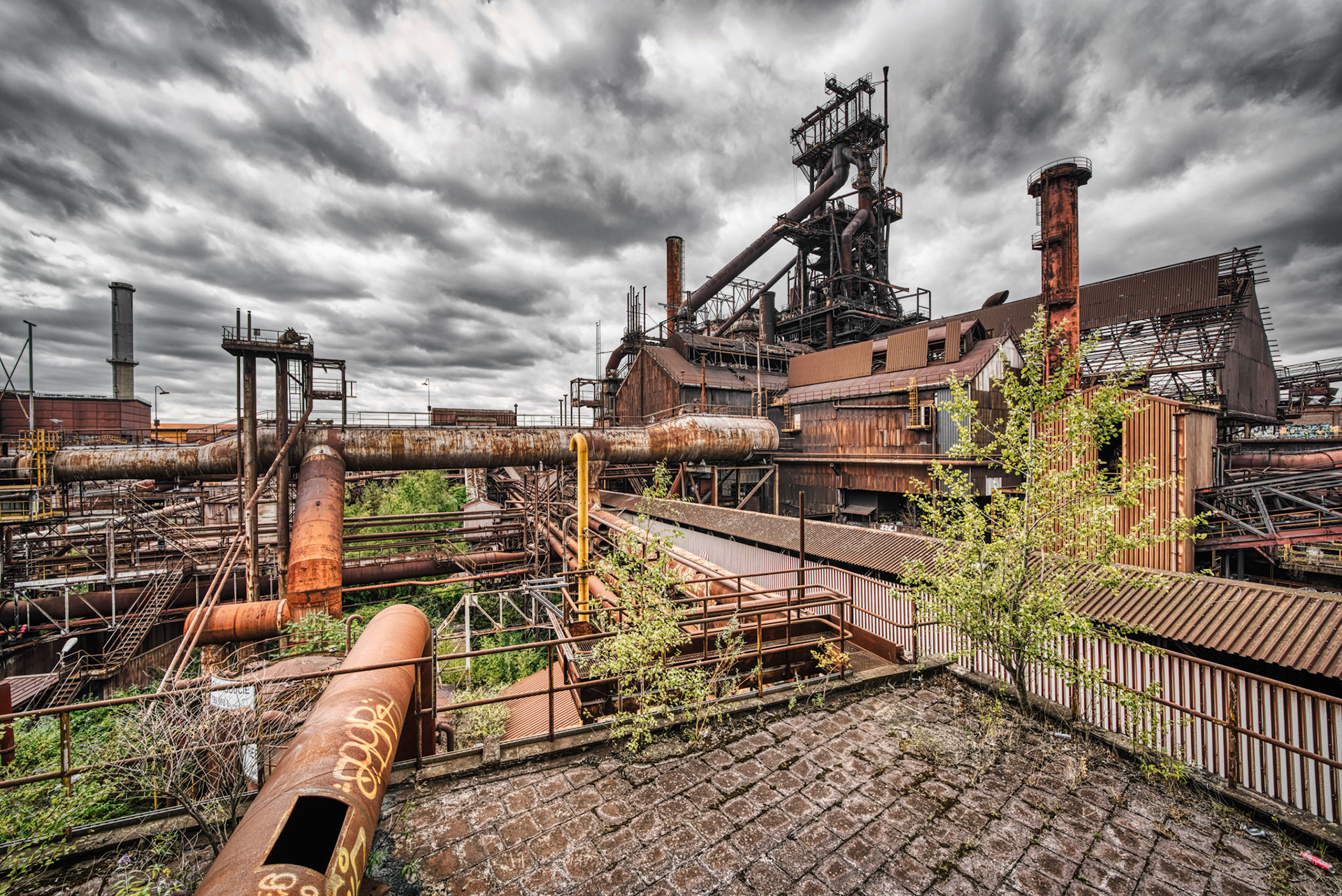
Hot air is blown from the surrounding blower ring and coke burned to yield temperatures up to about 1900 degrees. Burning coke provides the majority of the heat required for this process. At such high temperatures, Coke reacts with the oxygen in the hot air to form Carbon Monoxide (CO). The CO and heat now move upwards and meet the raw material running down from the top. The temperature in the upper parts of the Blast Furnace is considerably lower than at the bottom.
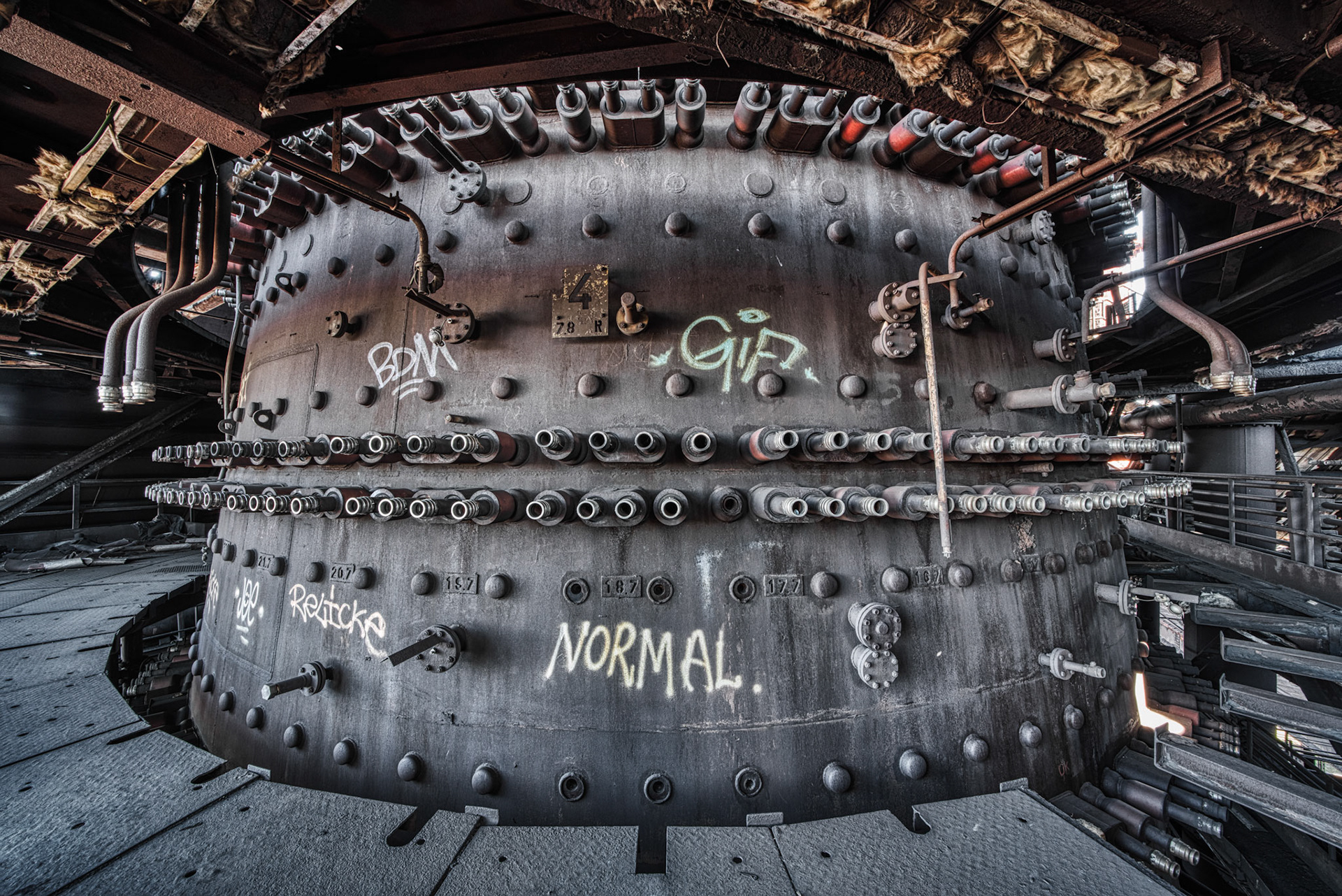
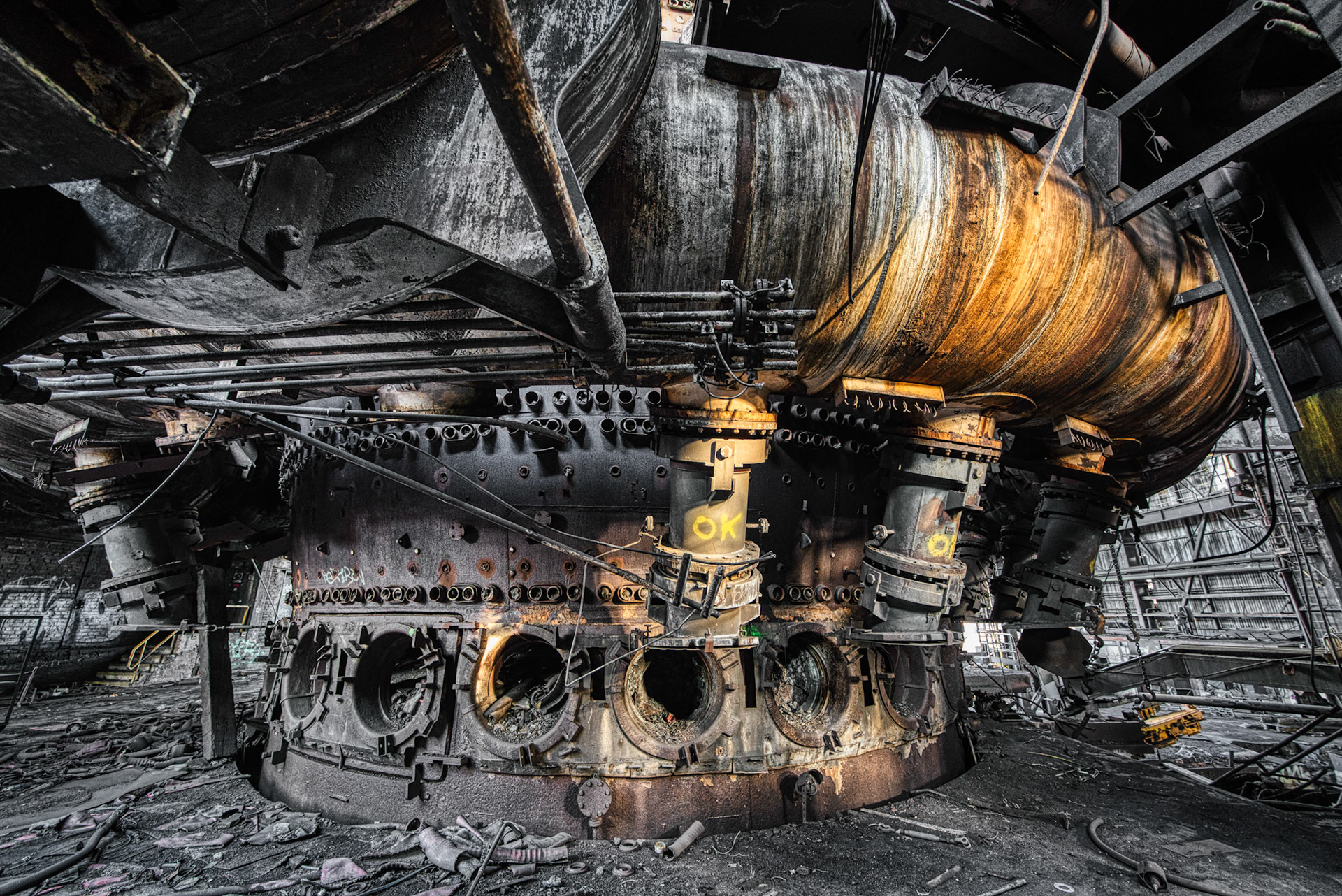
Ore, coke, and limestone, are weighed by discharging from bins and transported to the blast furnace top
by skip cars.
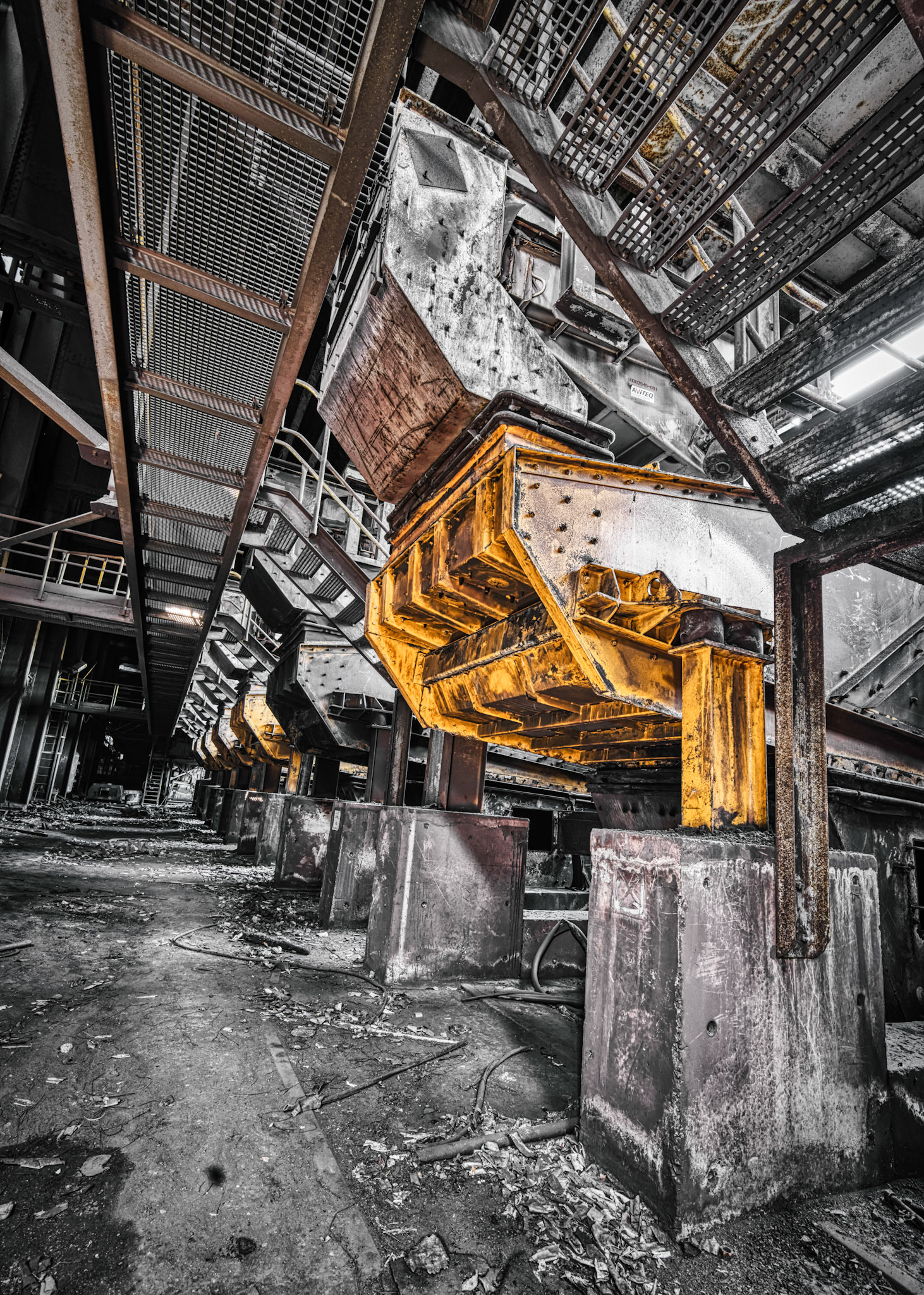
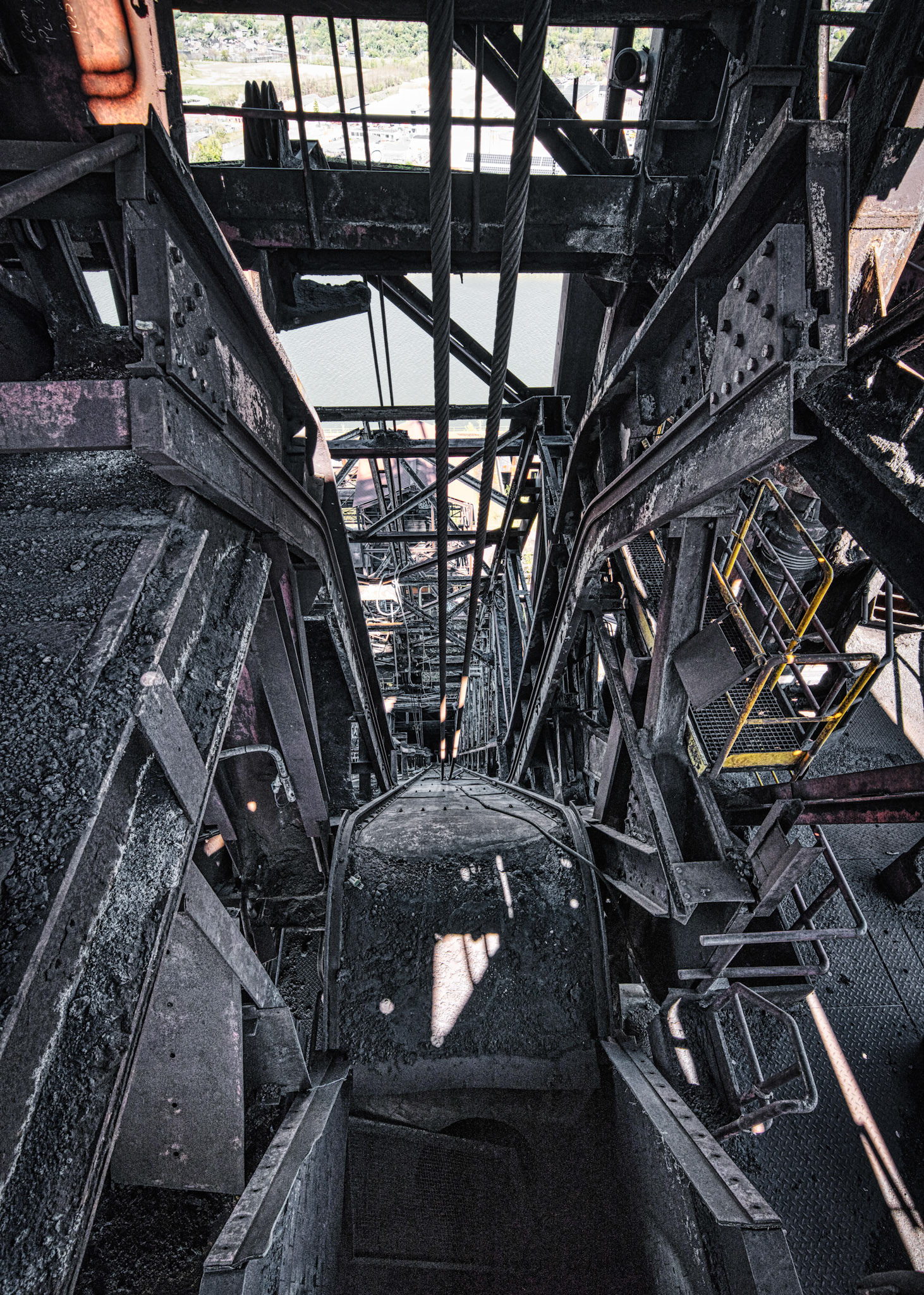
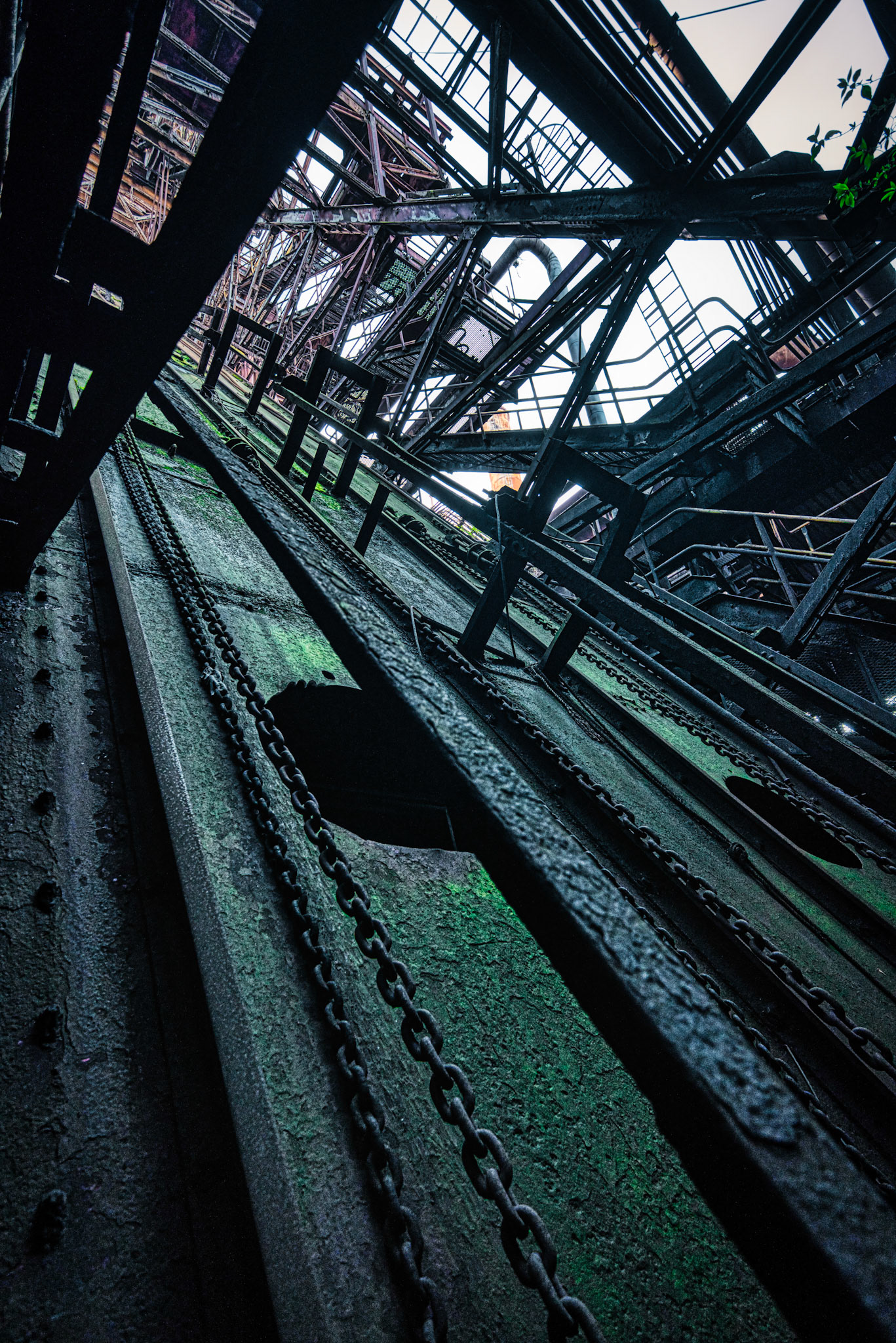
Every two hours the blast furnace is tapped: A tap hole is bored by means of a large drill. Out of it flow both the slag and the glowing yellow molten pig iron at approximately 1500 °C. When the outflow changes to slag only, the hole is closed up again by use of a mudgun. The blast furnace produces a total of 13,000 tons of pig iron a day.
Tapping will be done in the blast furnace cast house. It is the most labour intensive area in the entire operation.
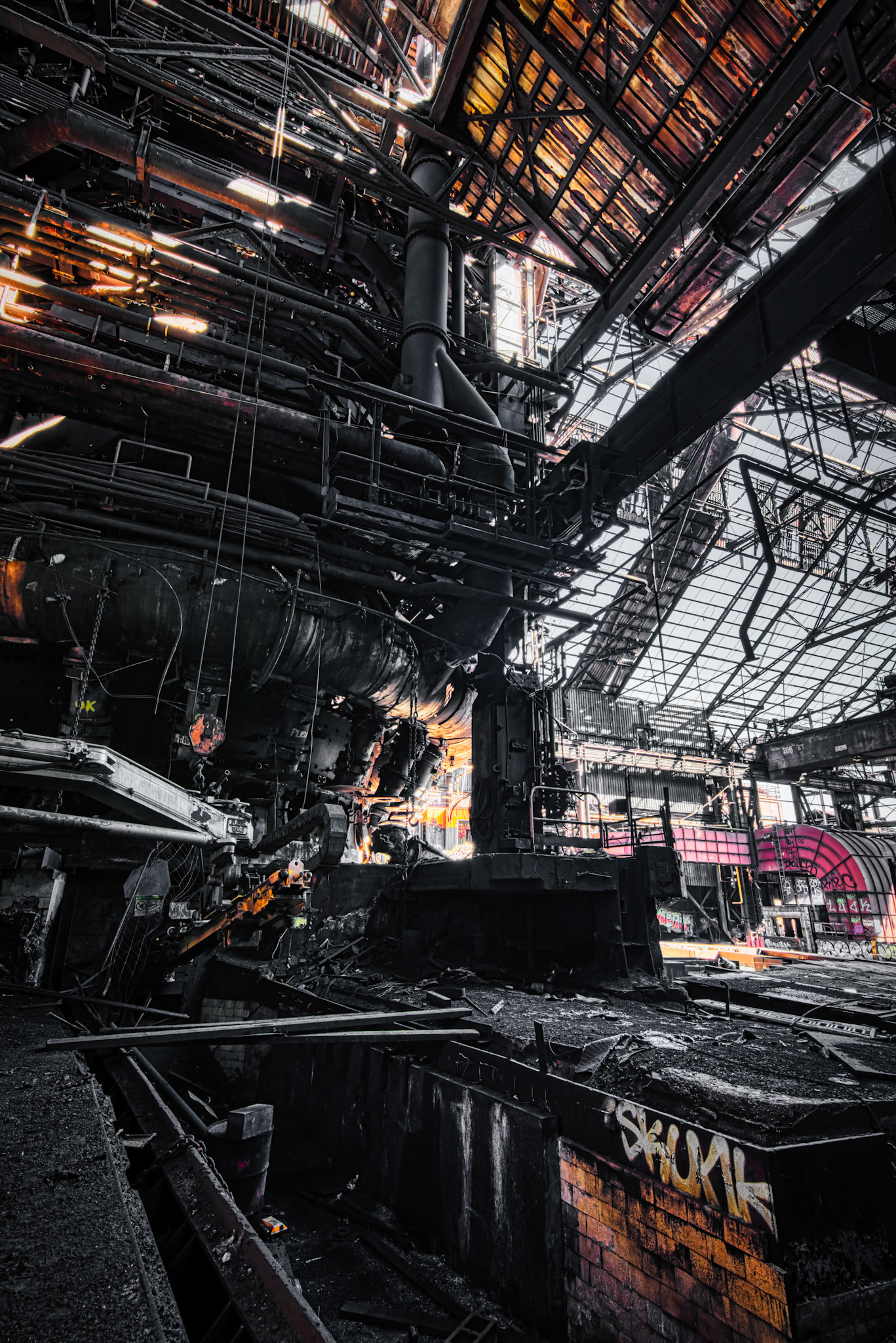
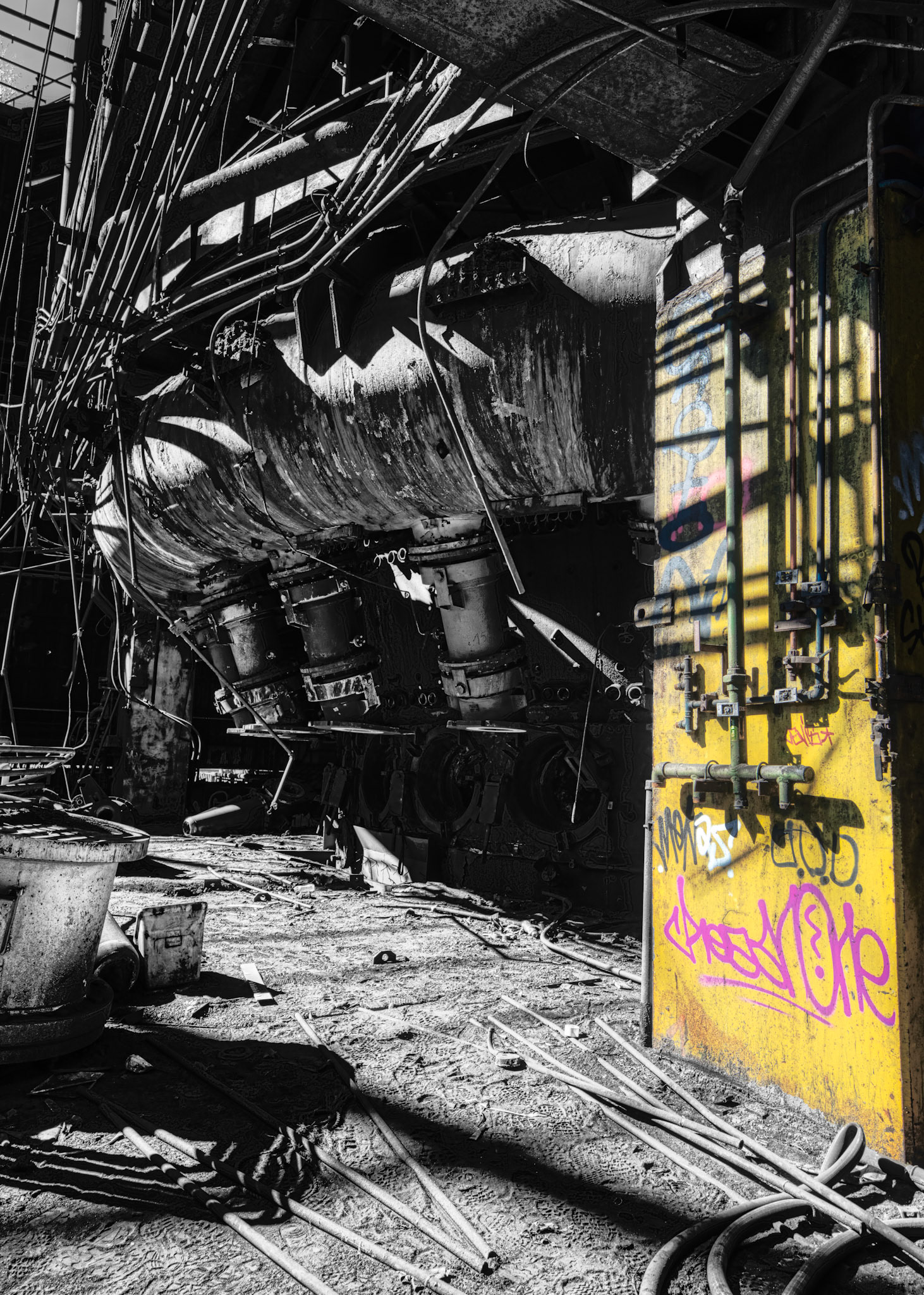
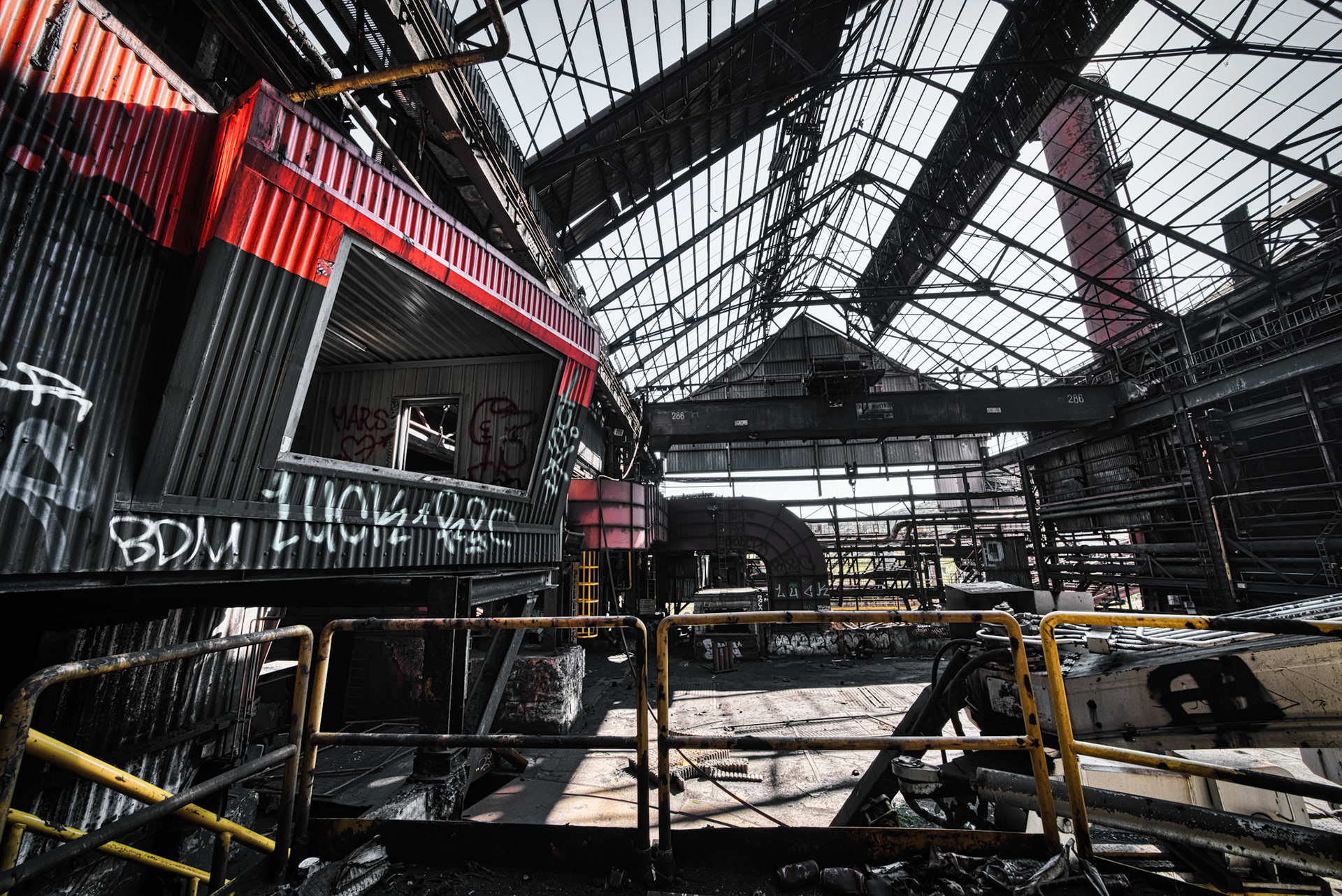
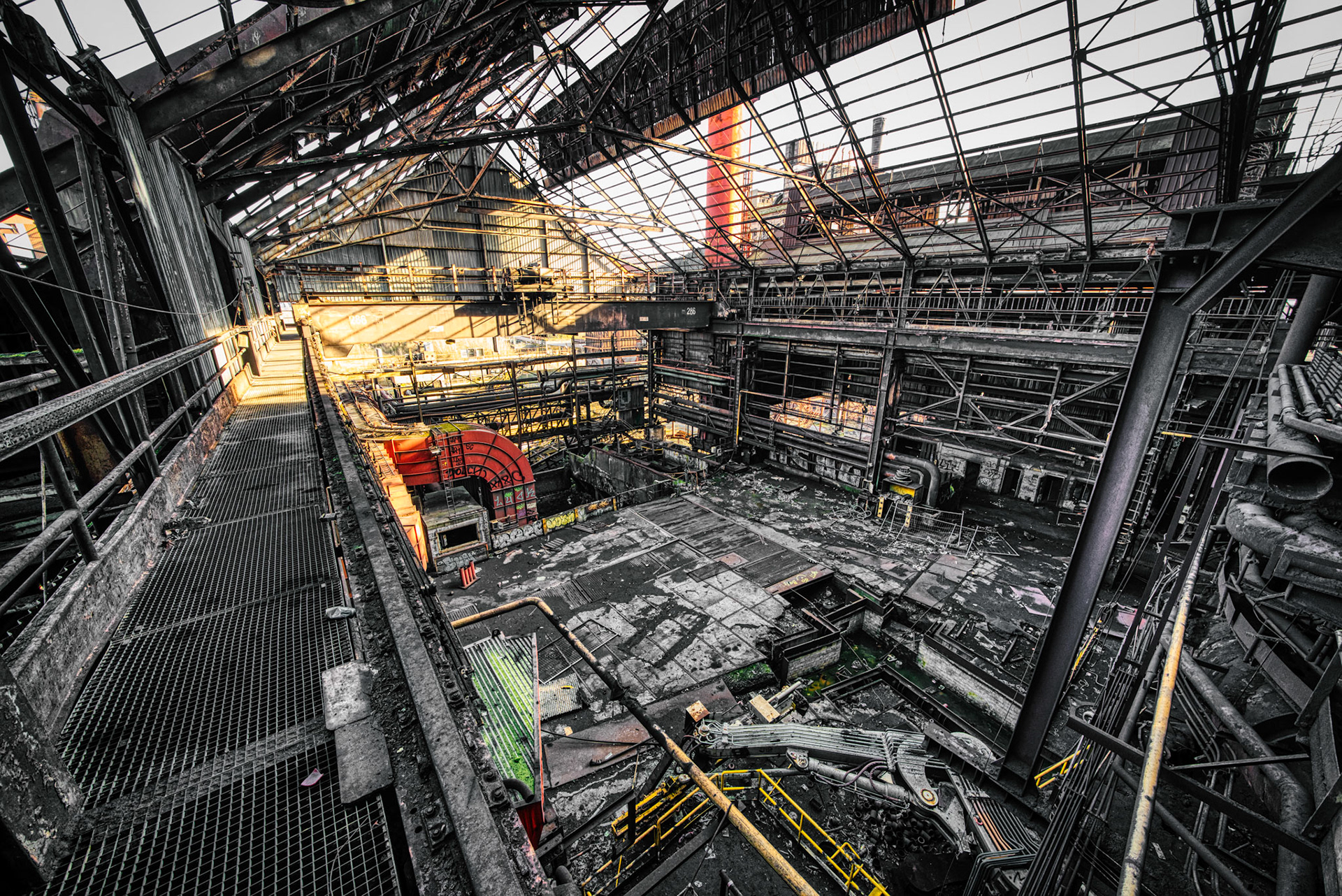
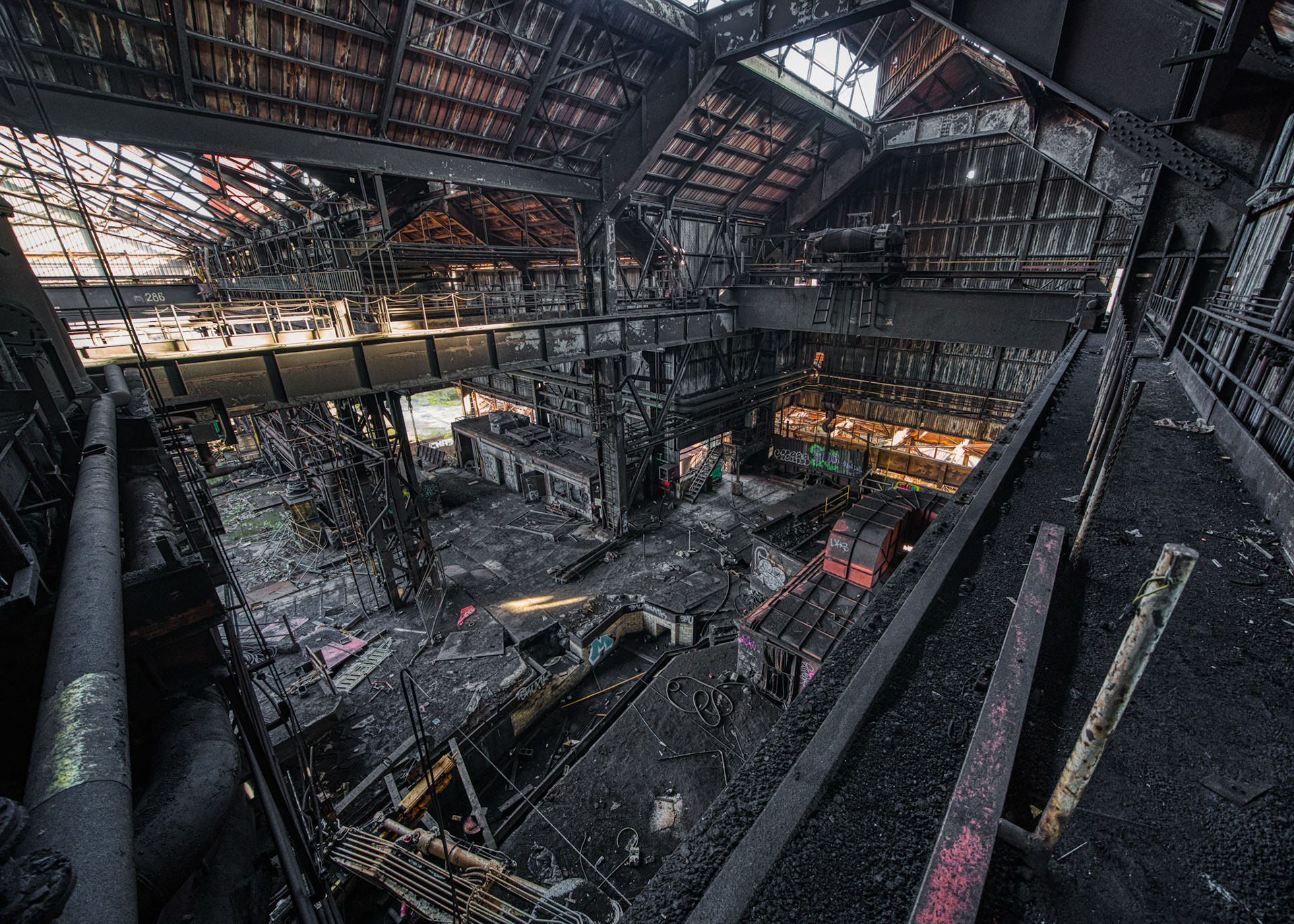
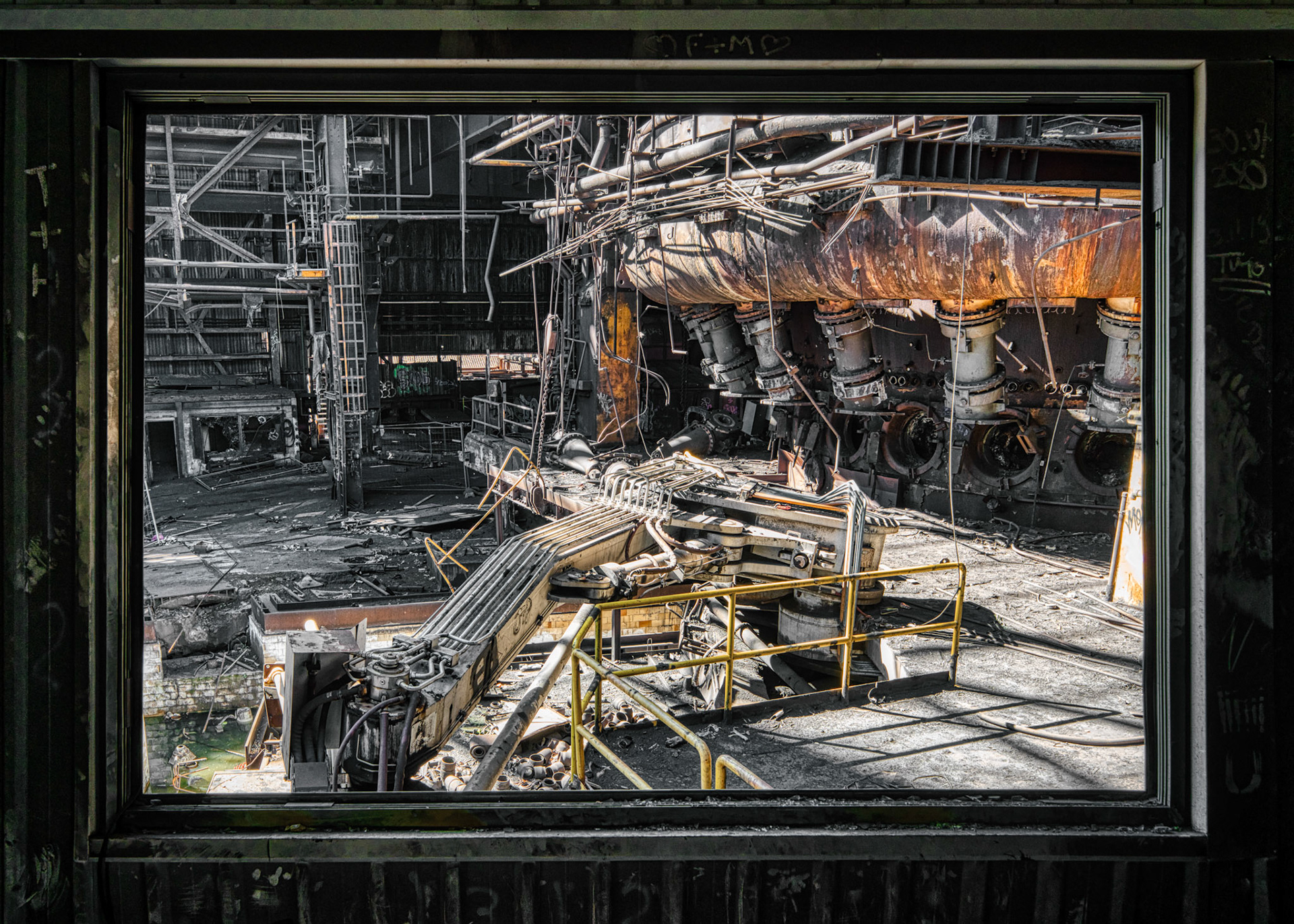
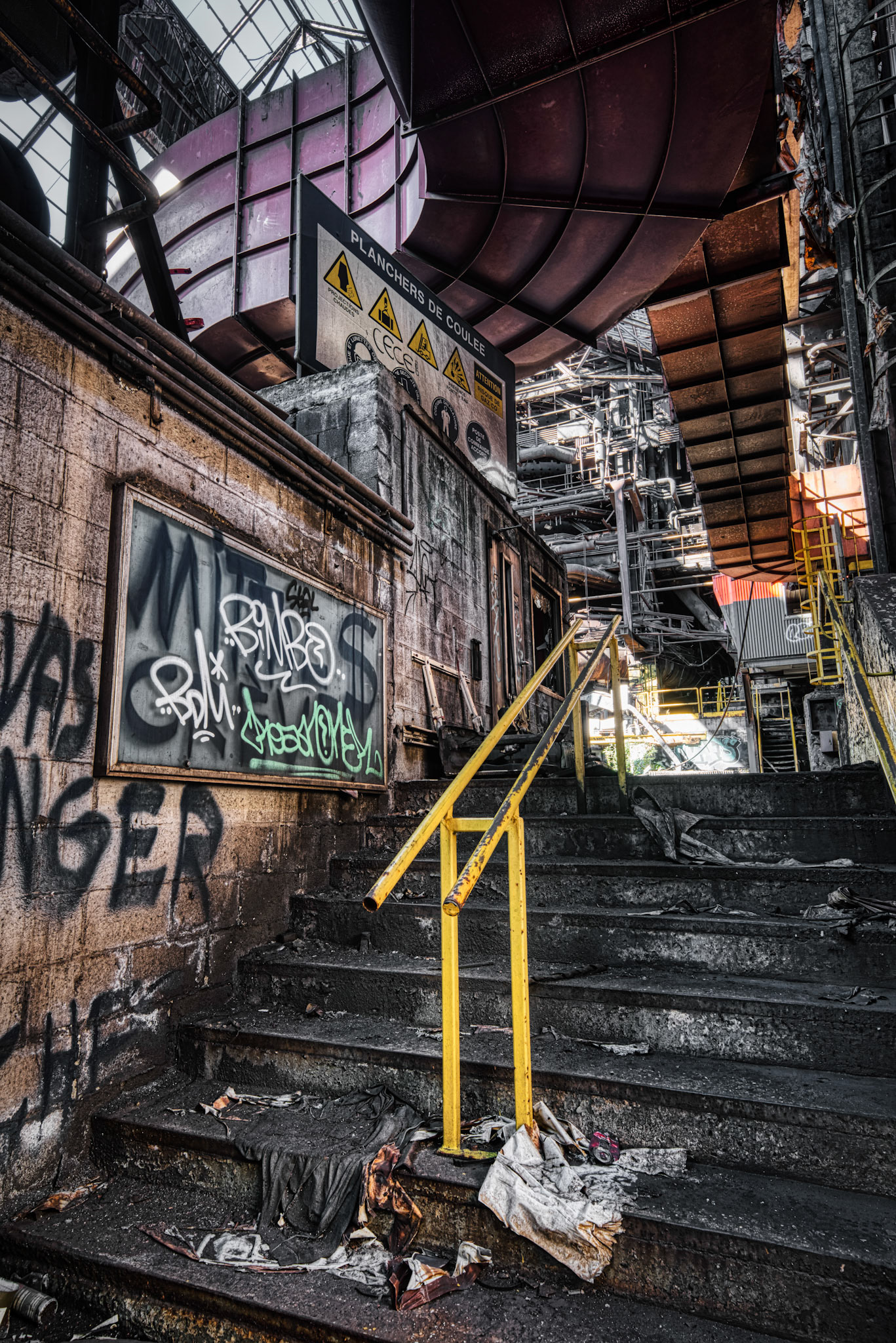
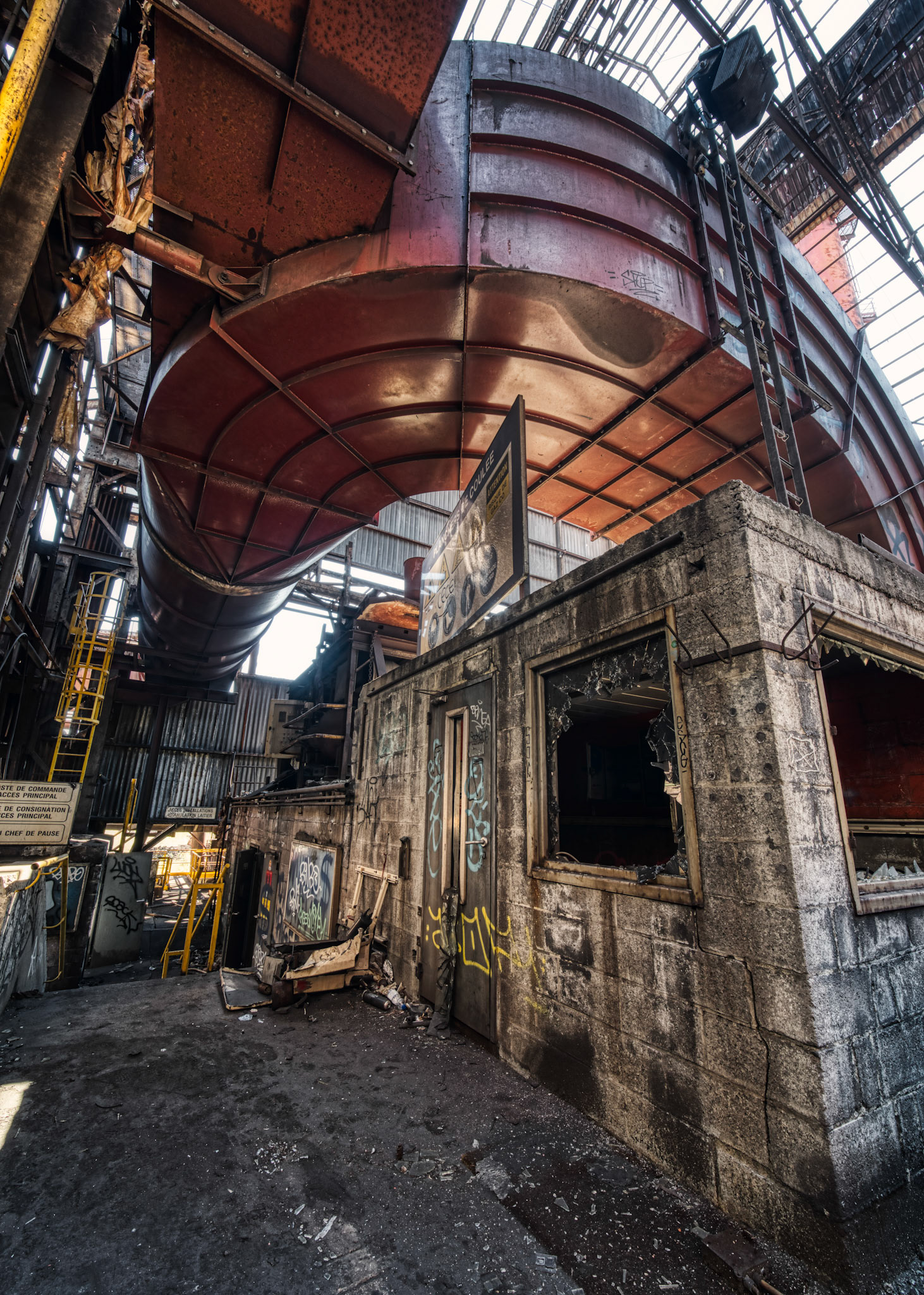
The supporting structure of the blast furnace is staggering and consists of various floors, pipes, tanks, ladders and stairs.
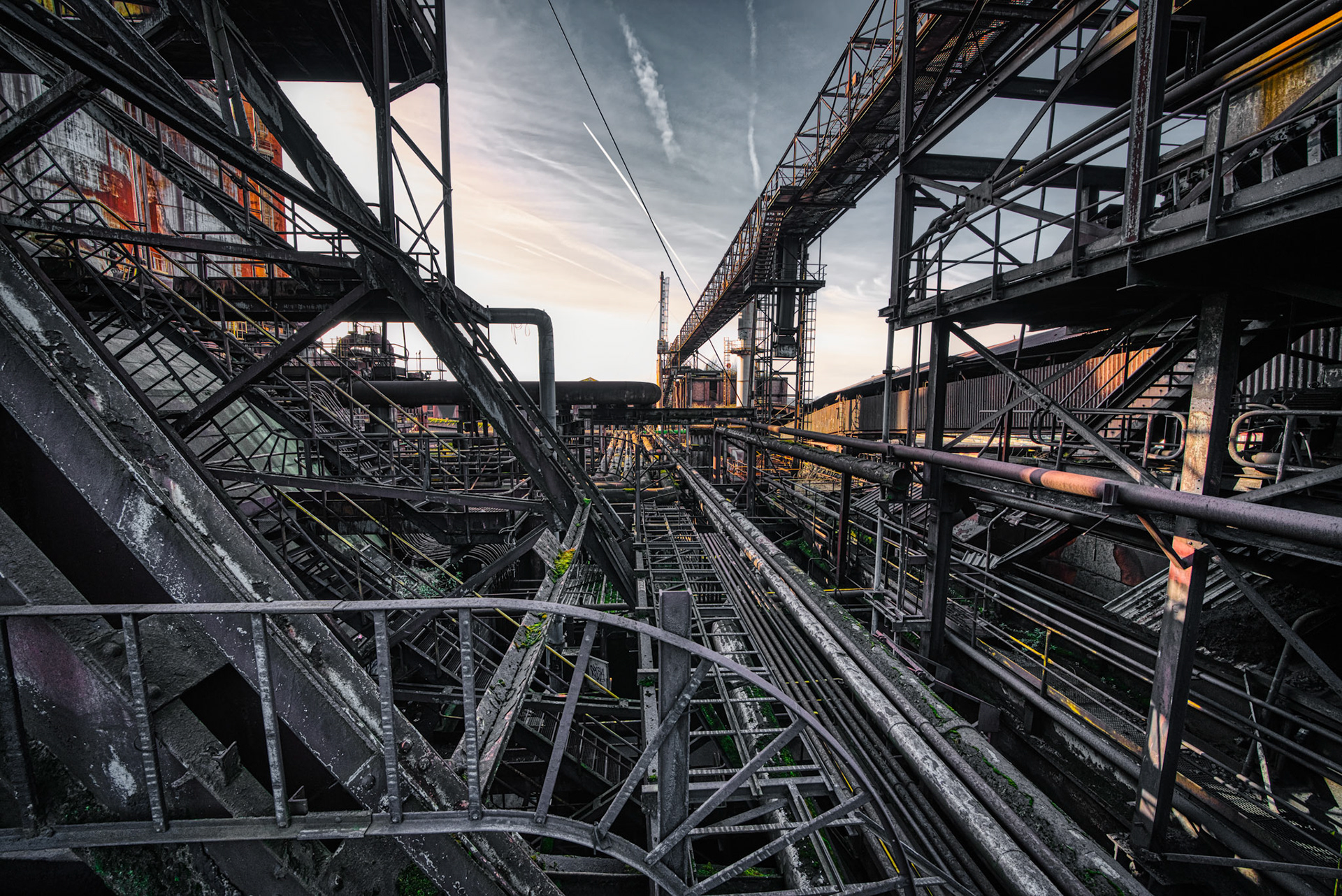
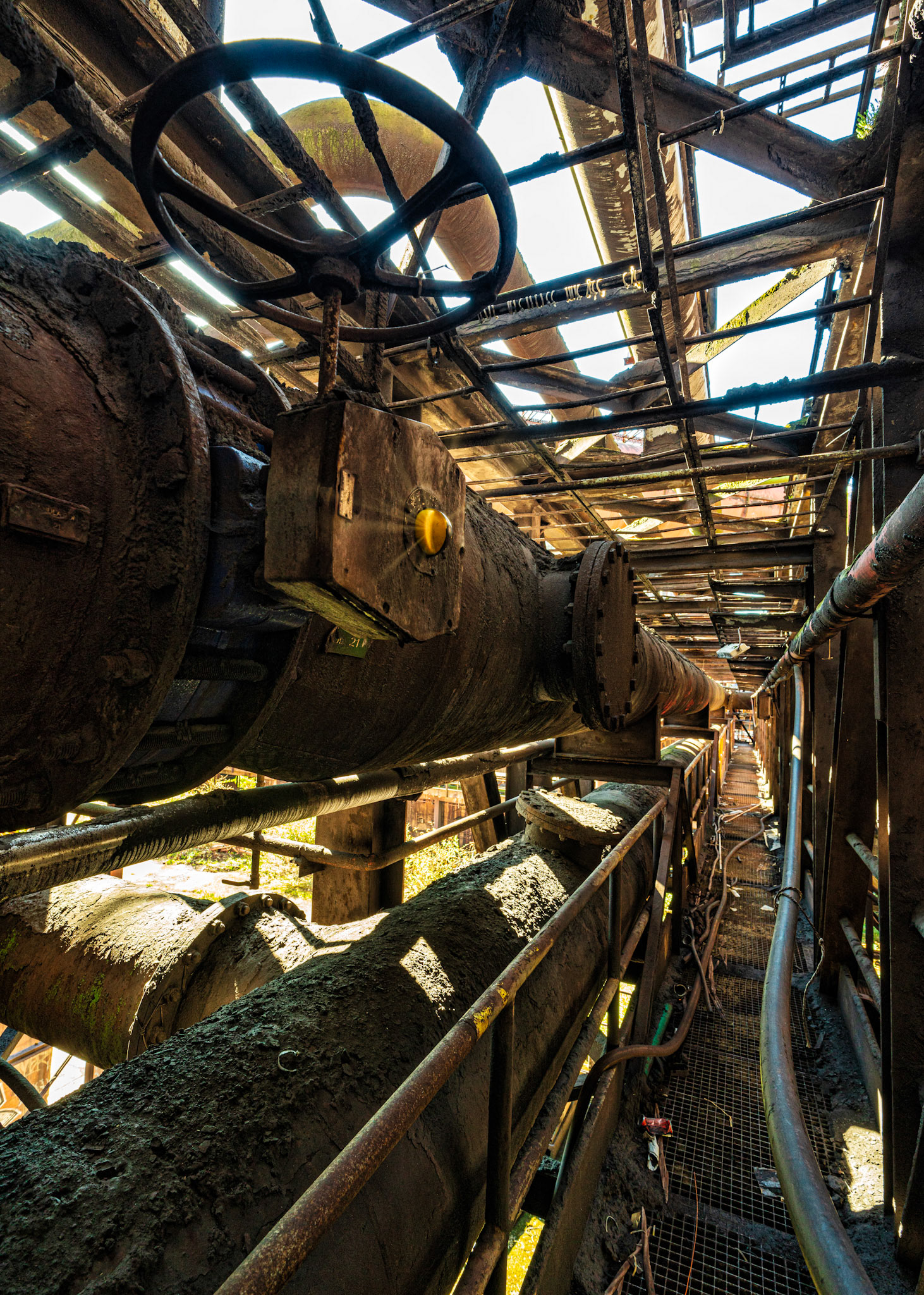
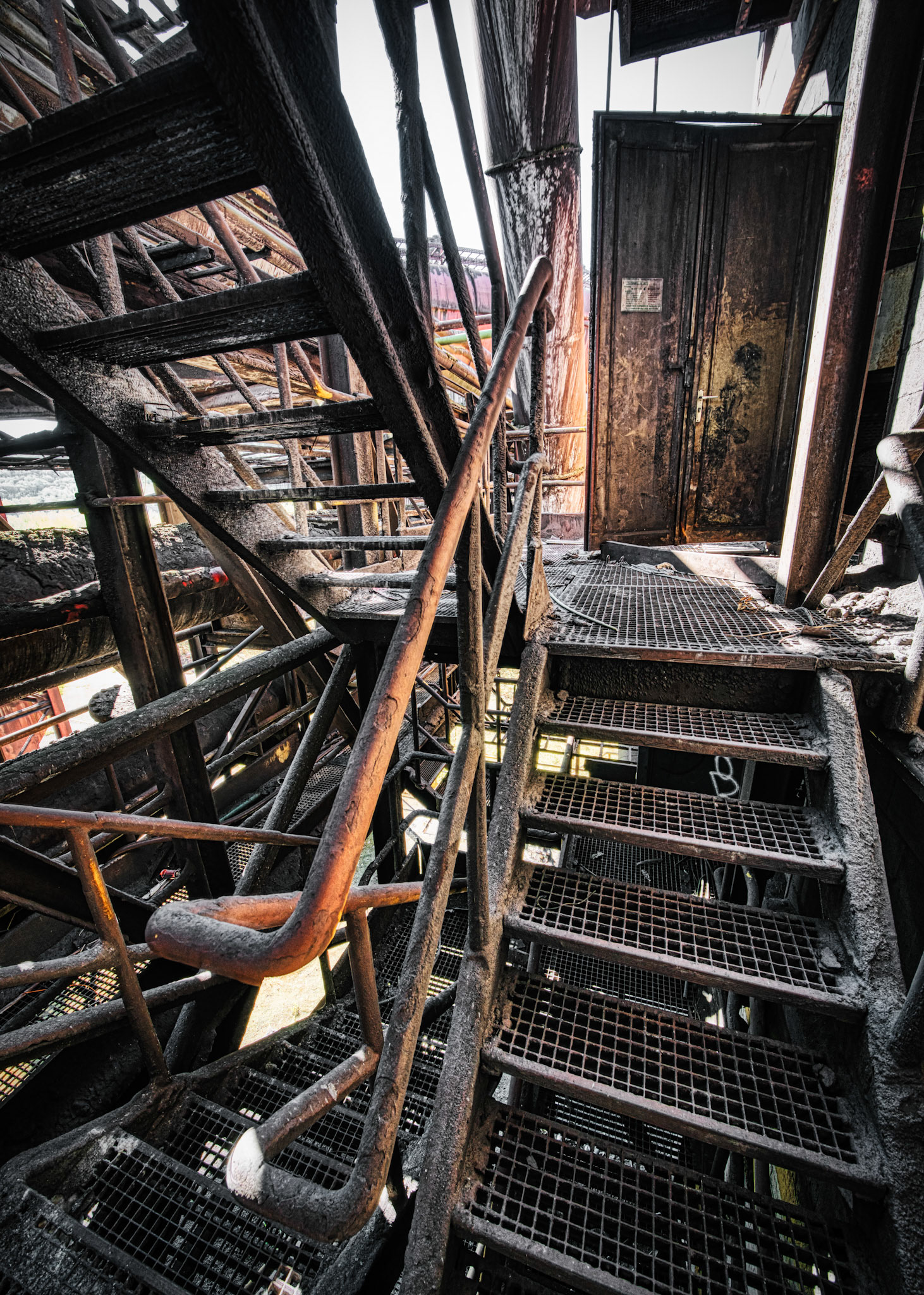
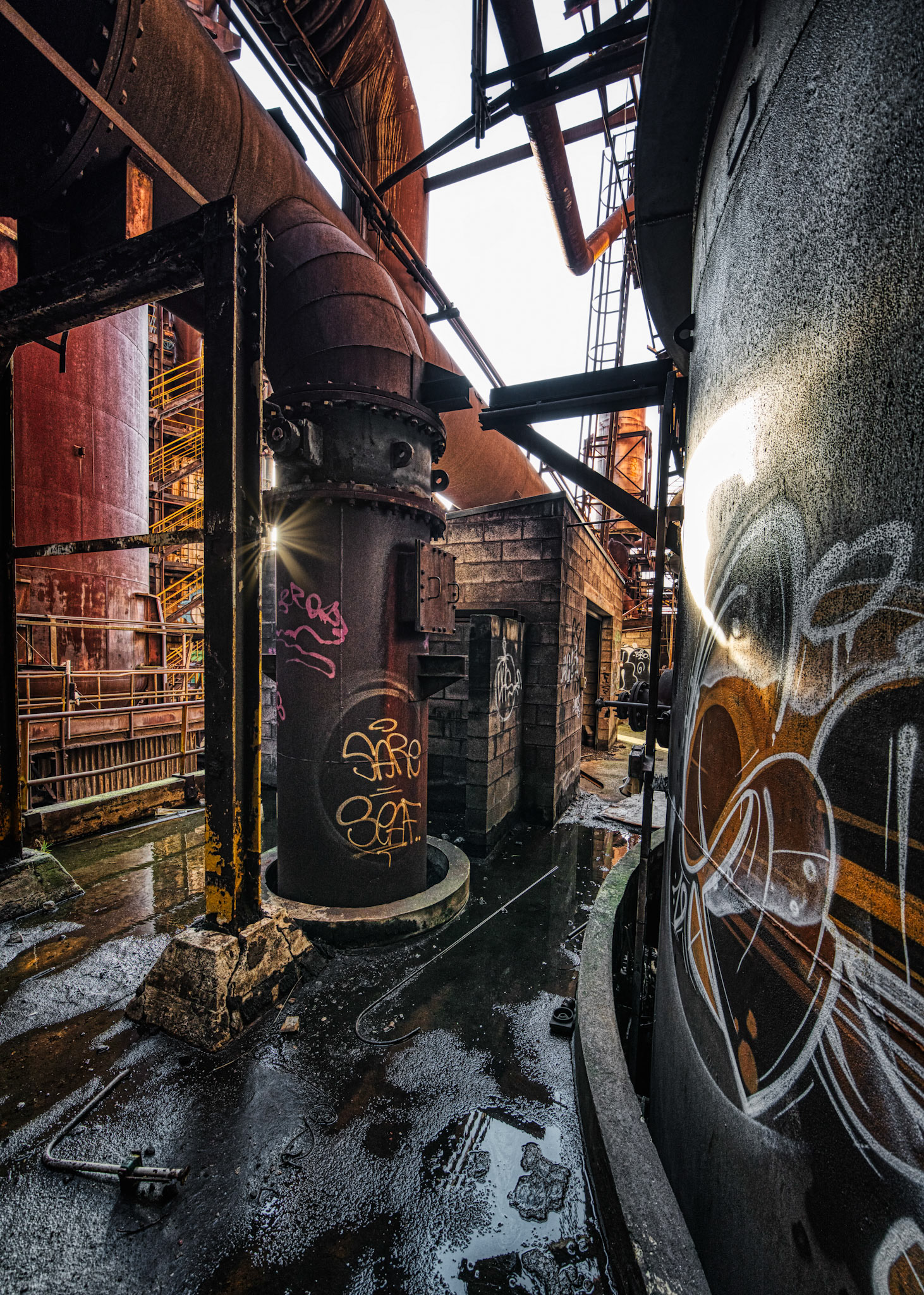
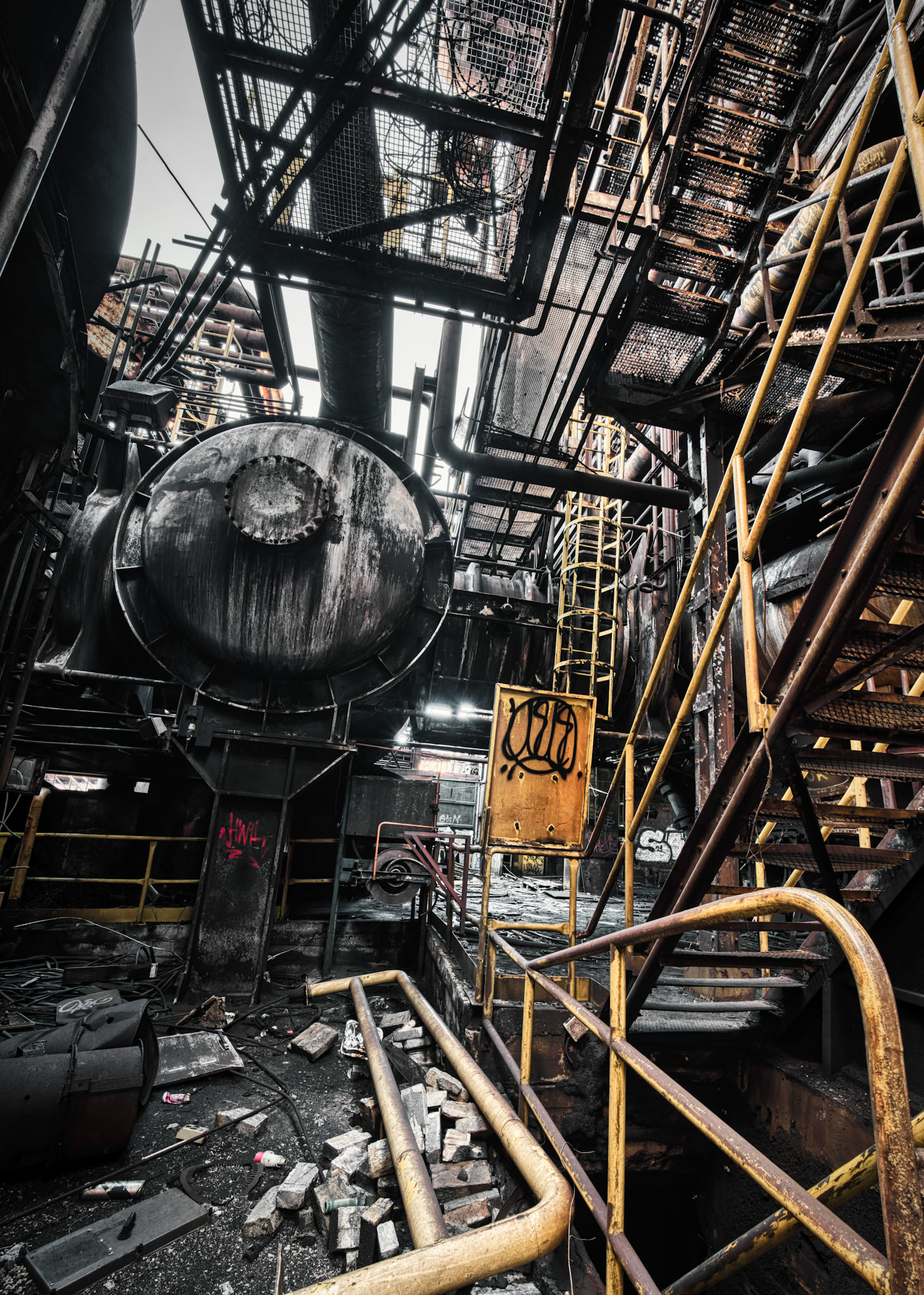
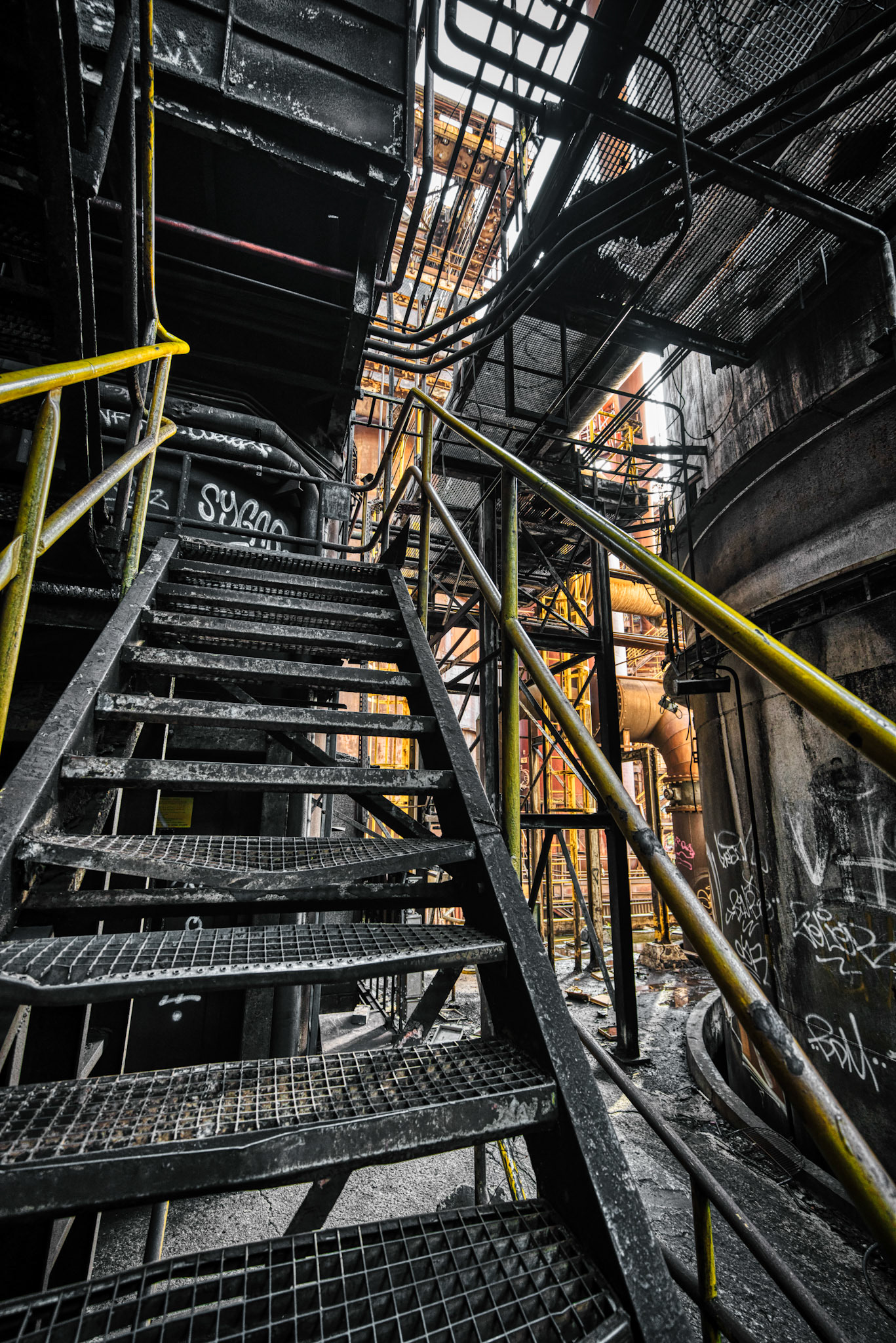
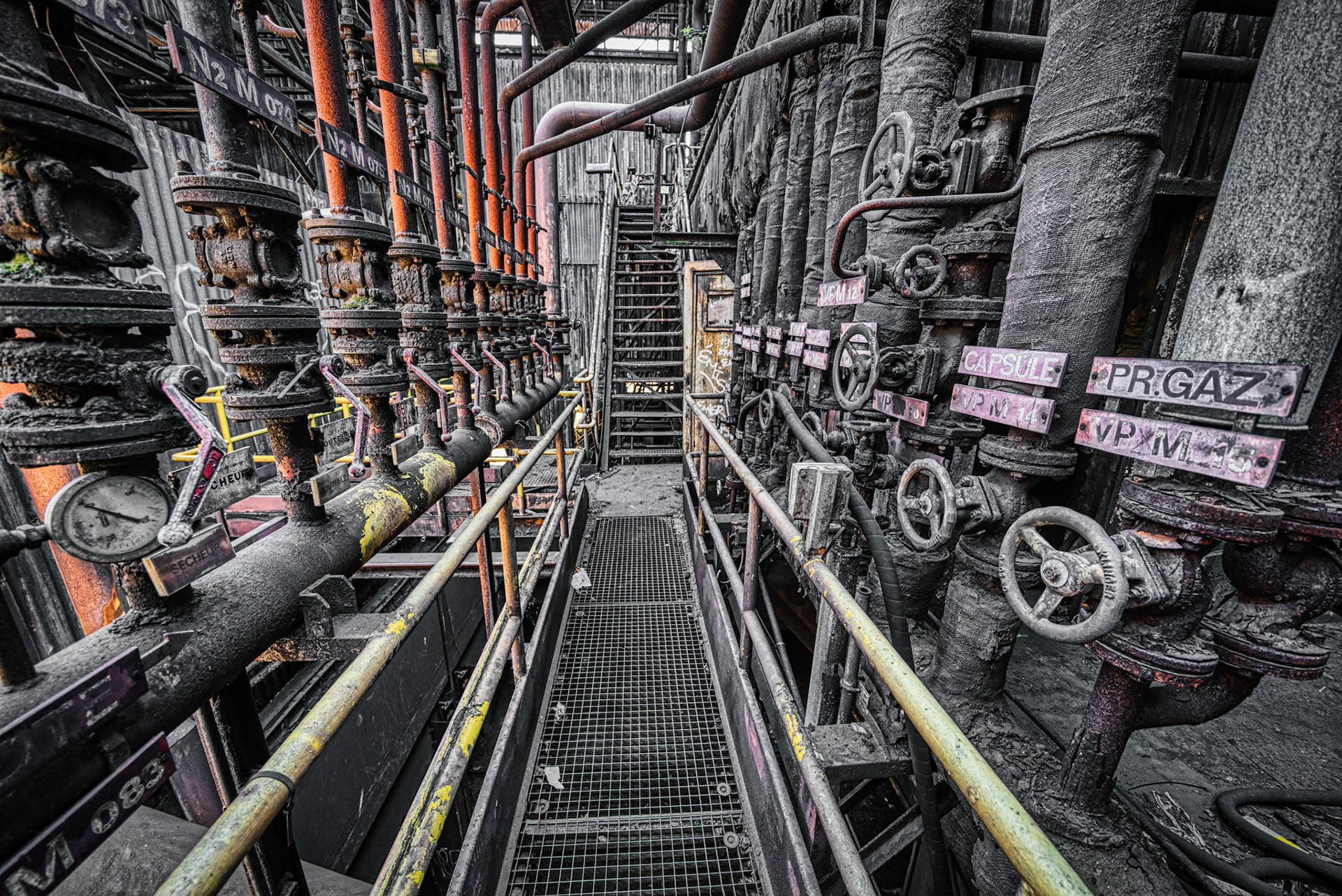
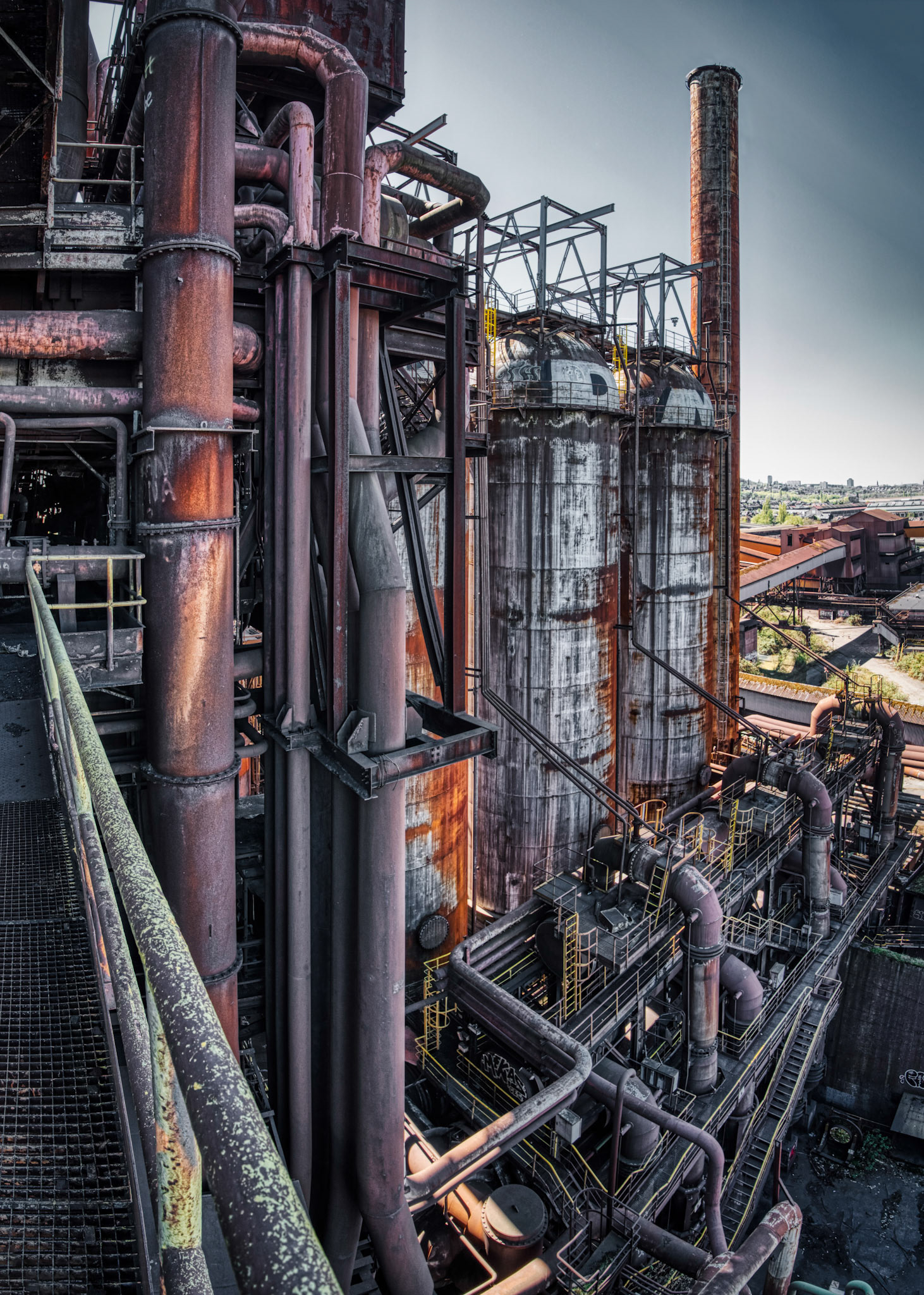
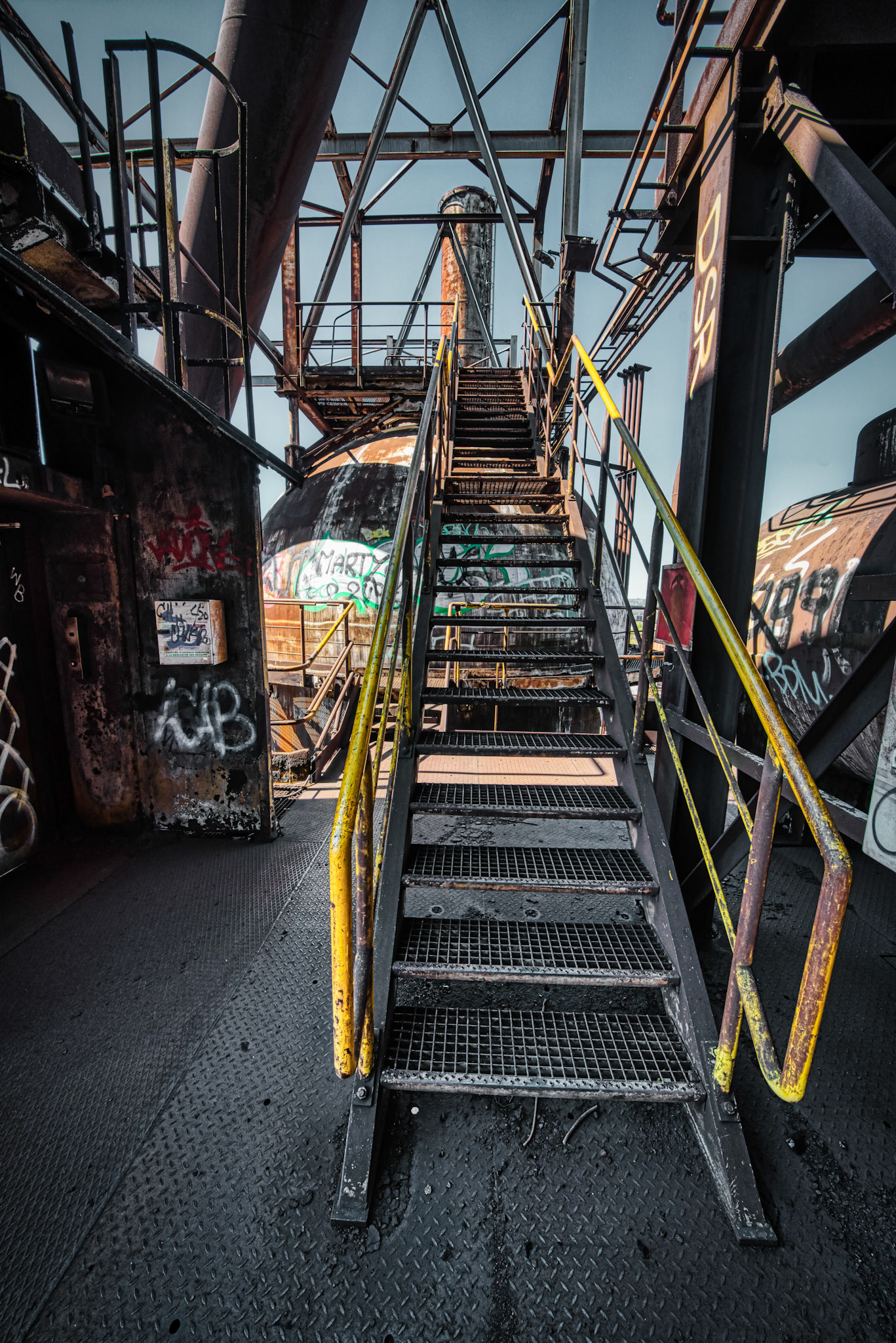
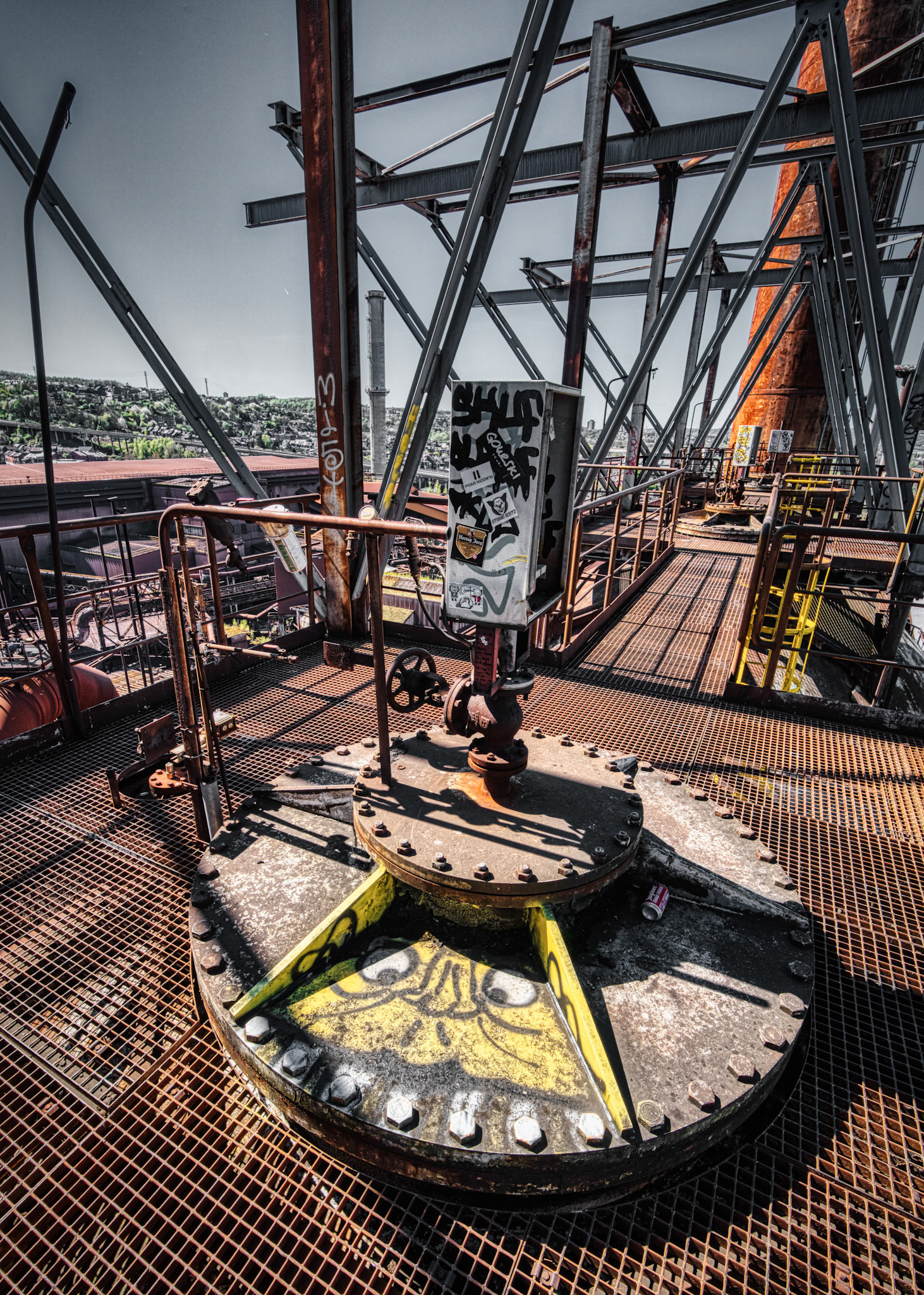
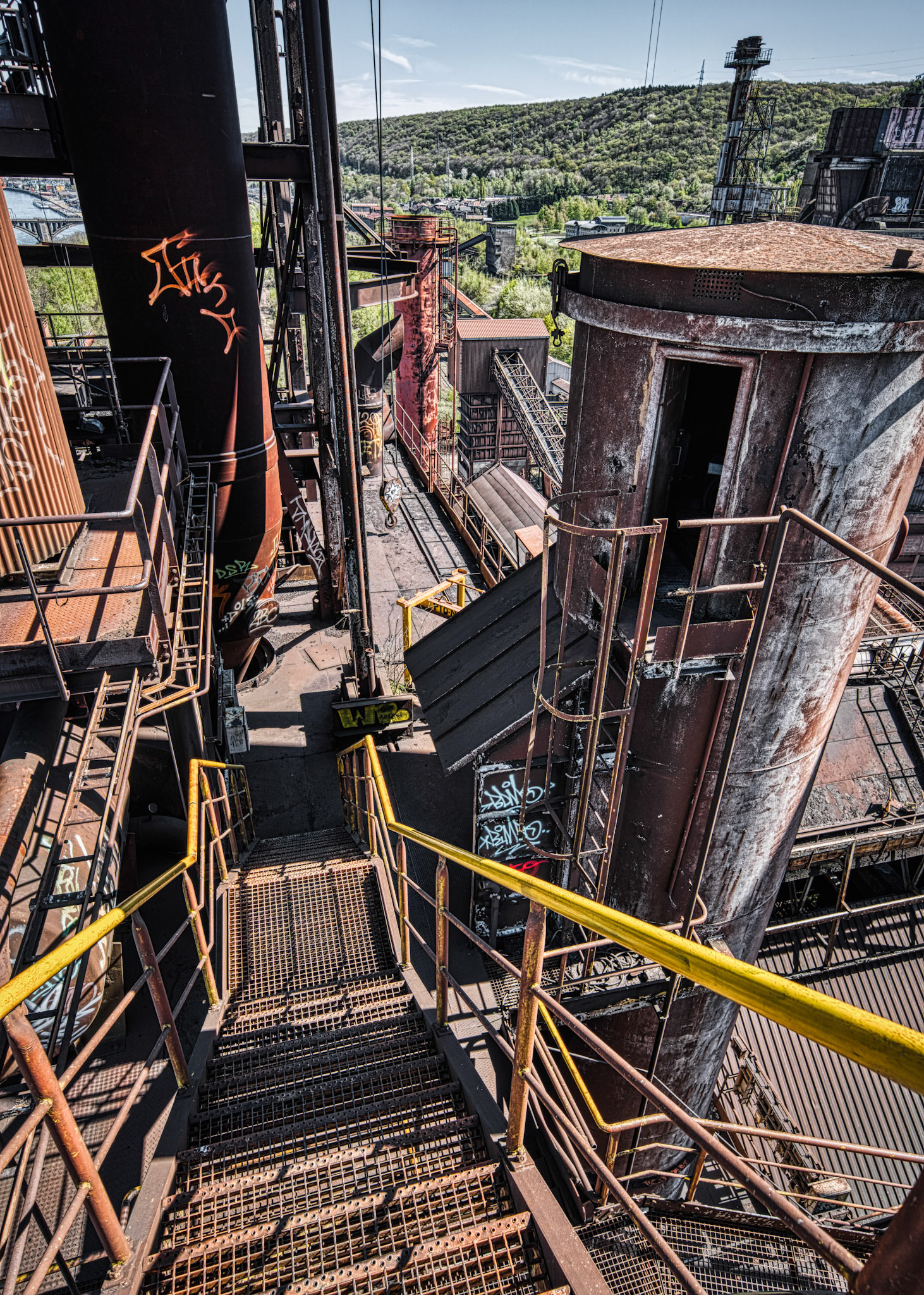
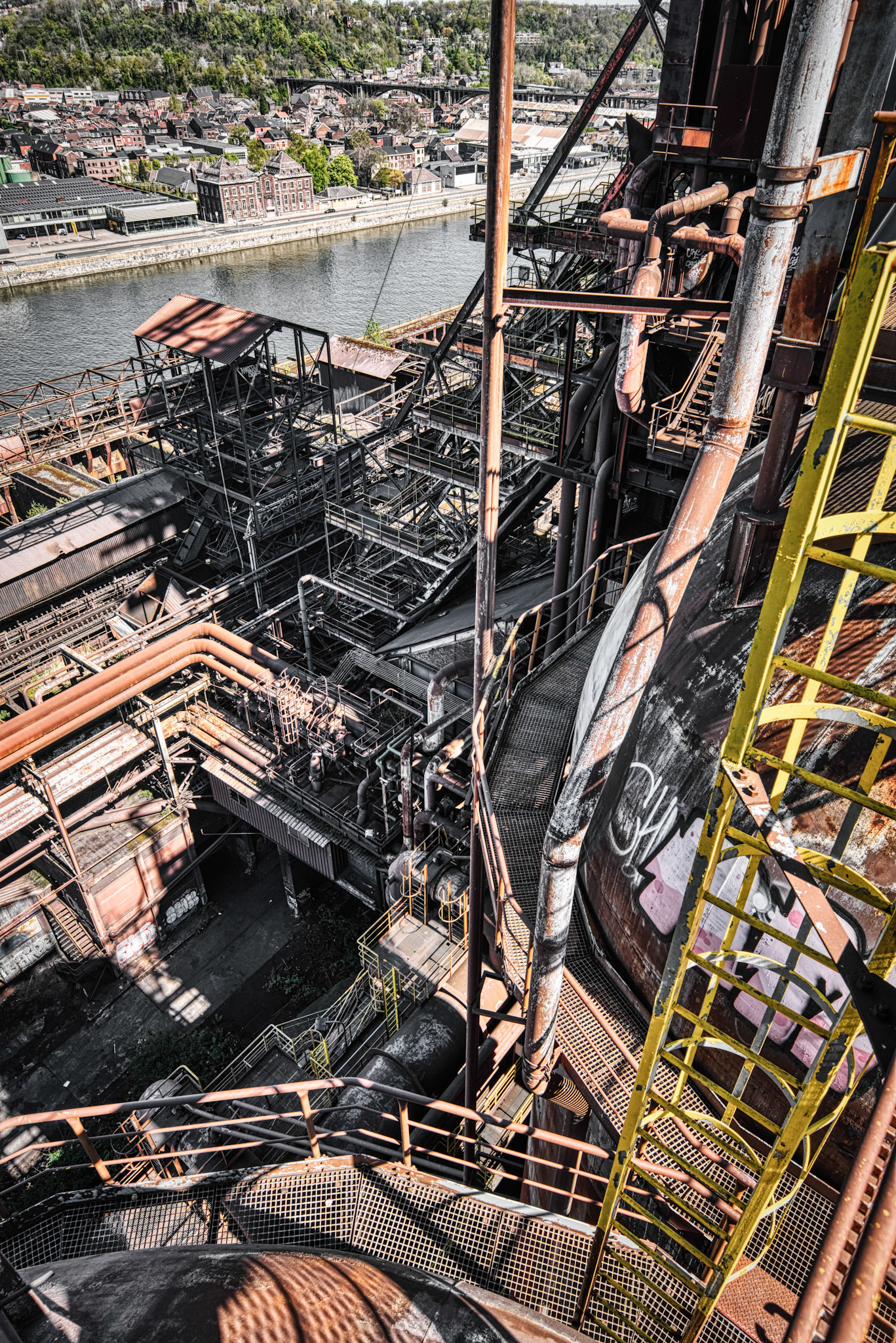
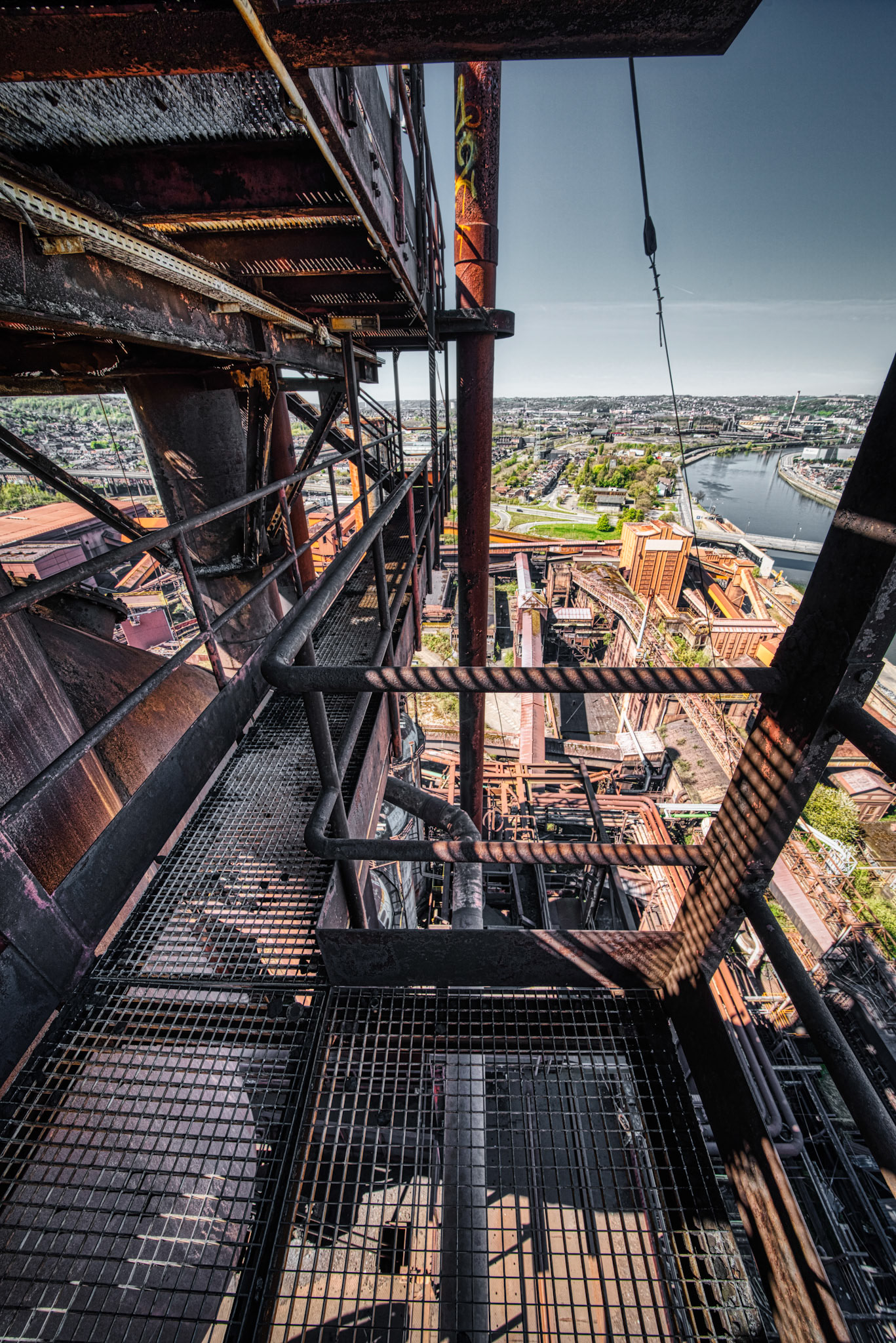
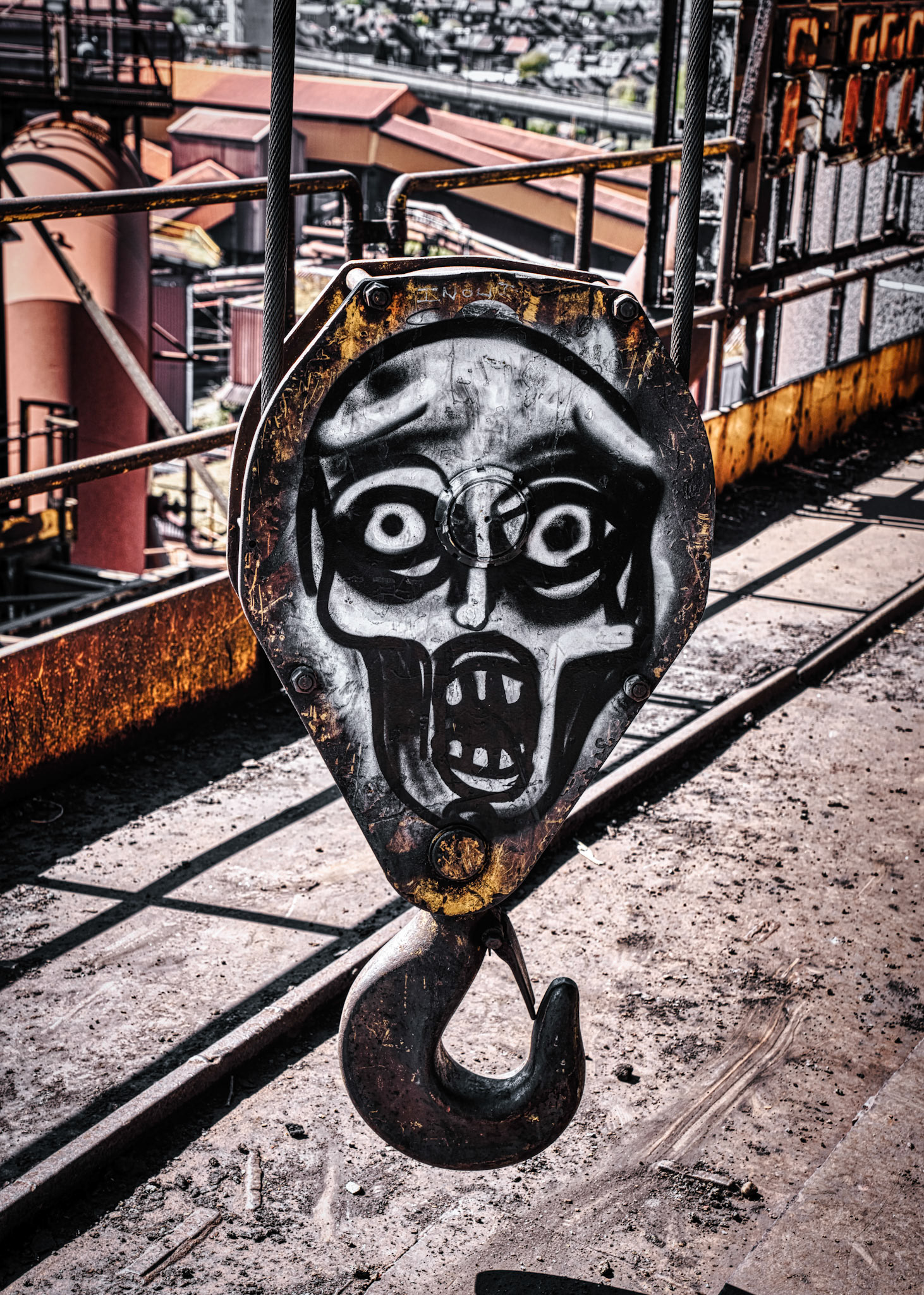
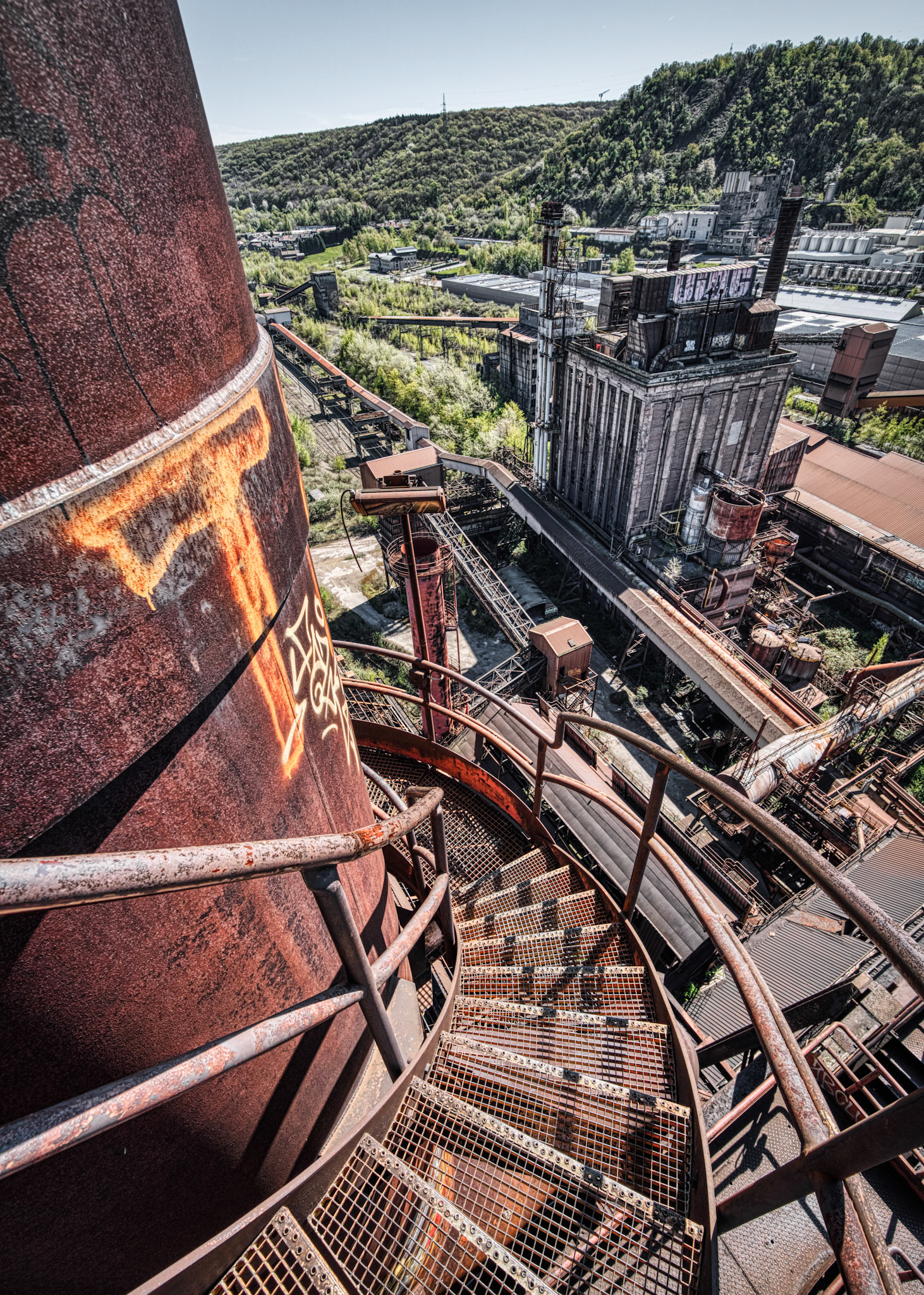
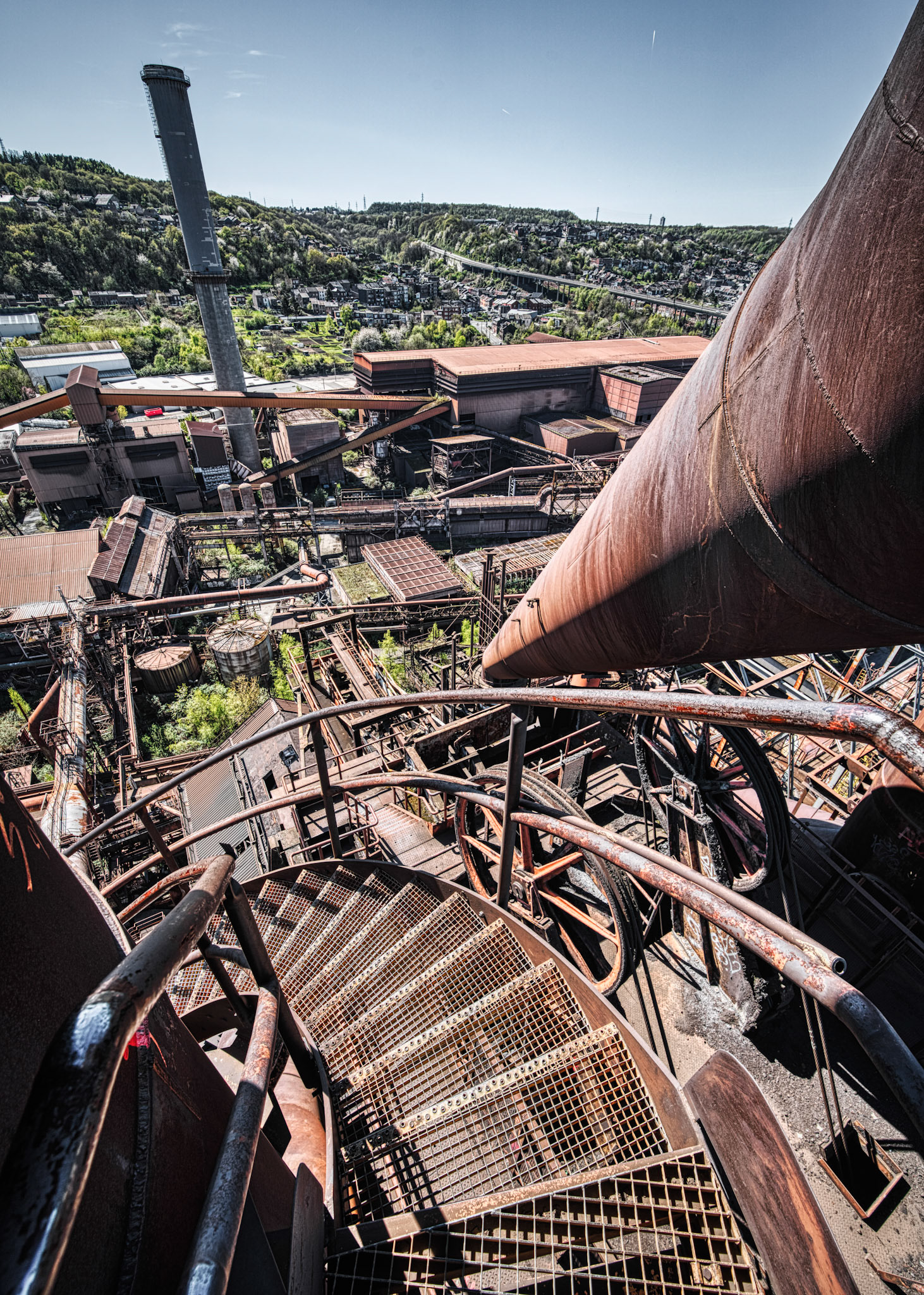
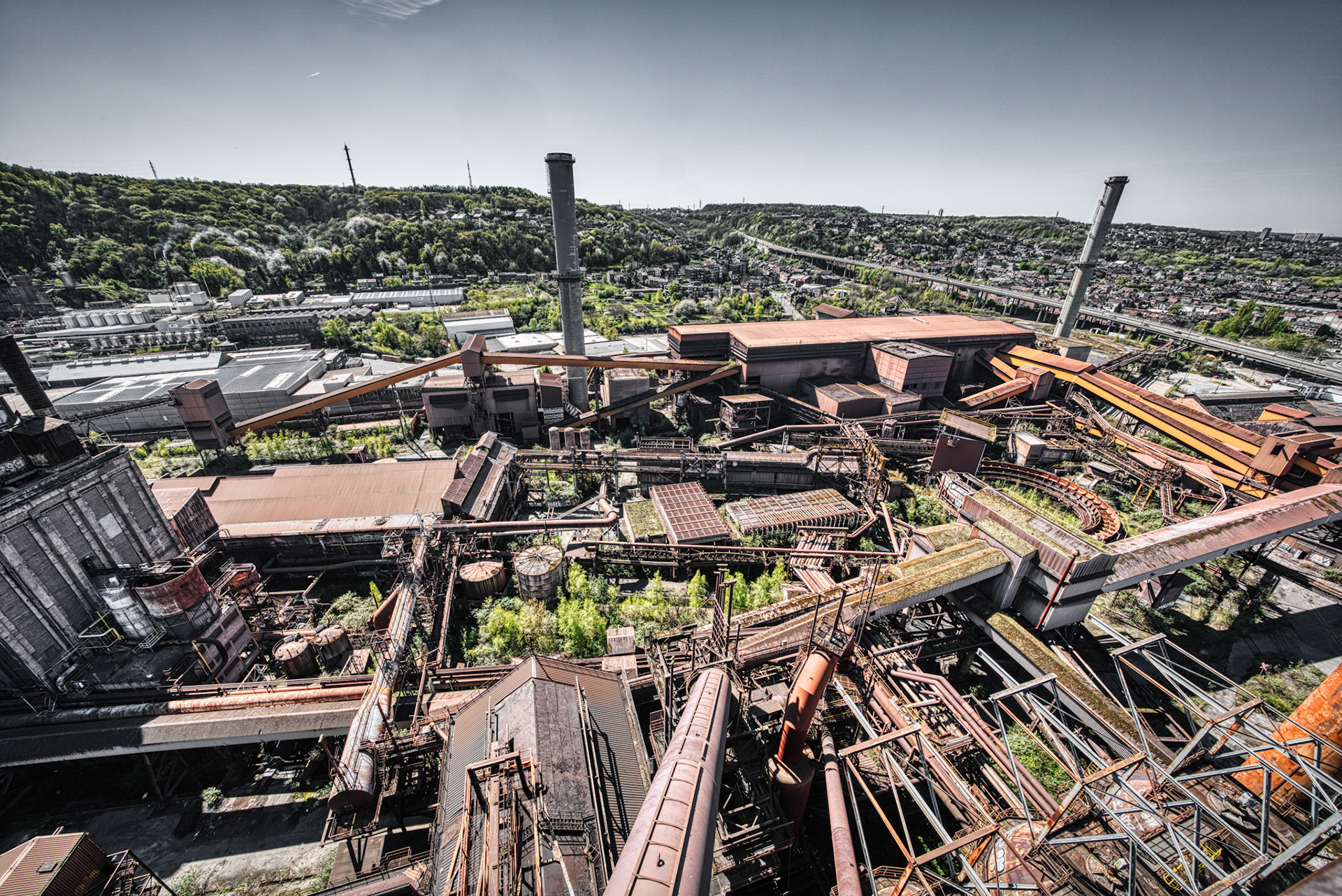
During the production of liquid iron in a blast furnace, gas will be produced as byproduct with a temperature of around 100 to 150 degrees. The energy content of this gas may equal to approximately 30 % of the gross energy consumption in the blast furnace. This energy content can be utilized by recovering, cleaning, and storing the BF gas and using it as a fuel gas in the steel plant or in the boilers for the production of steam for the electricity generation.
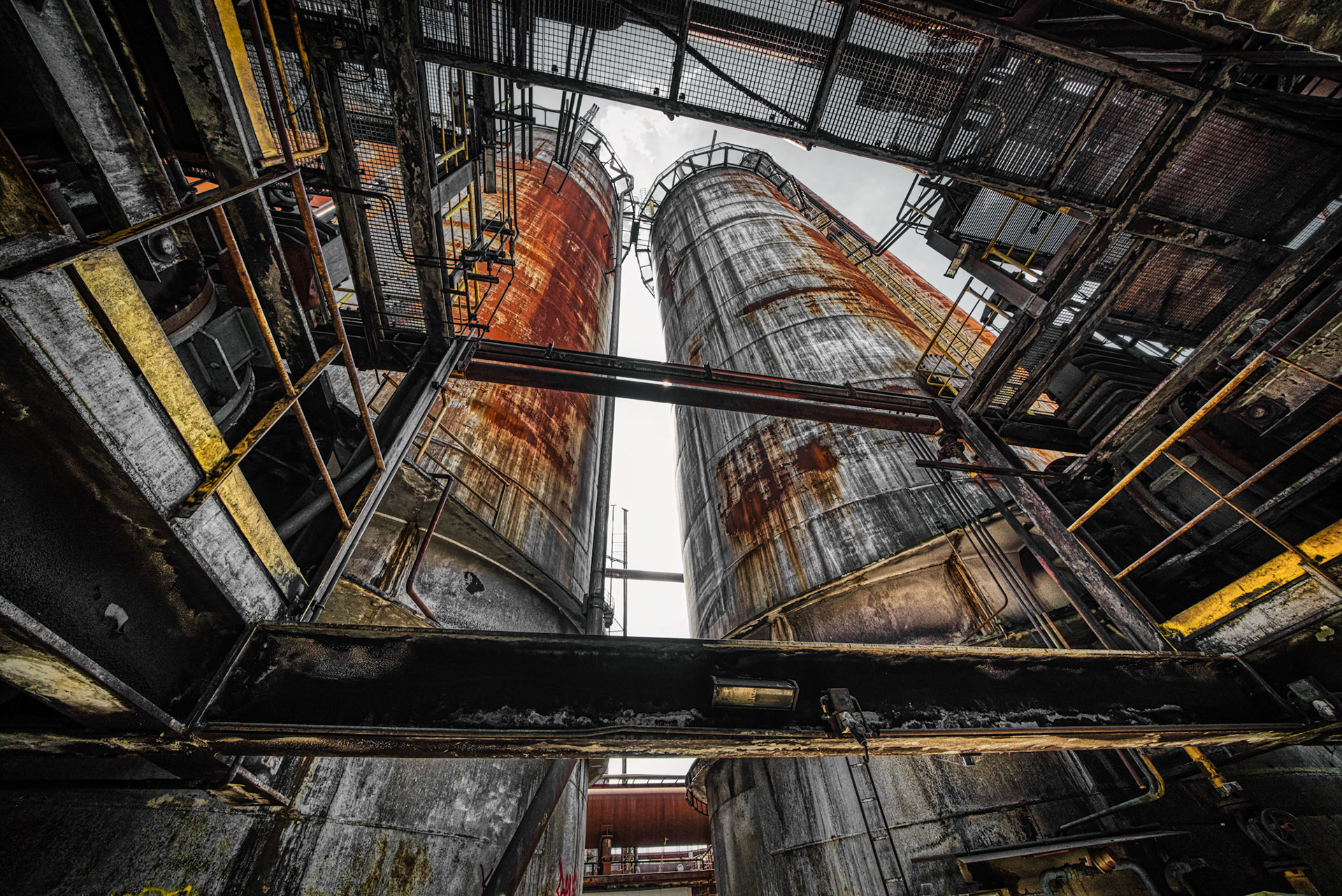
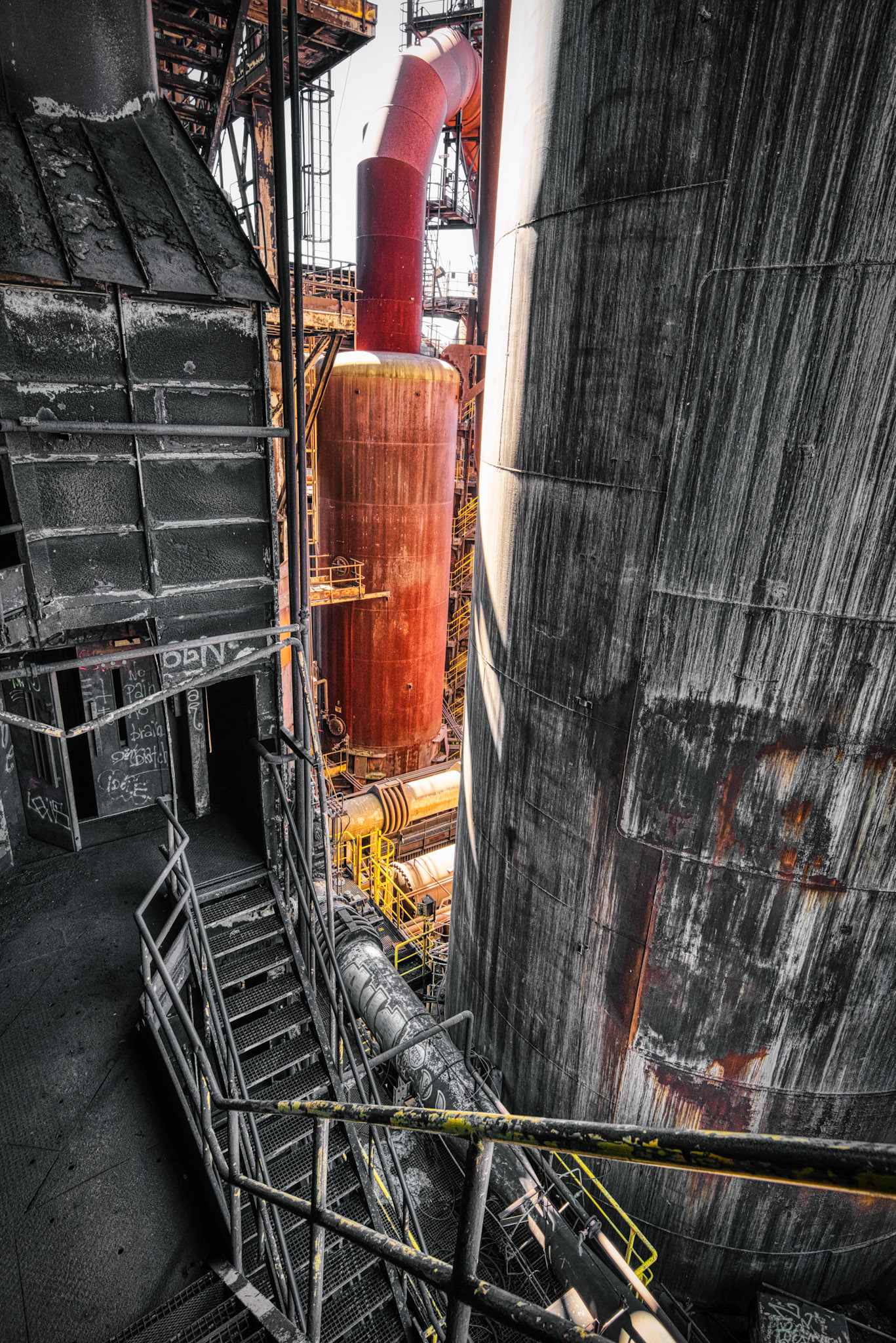
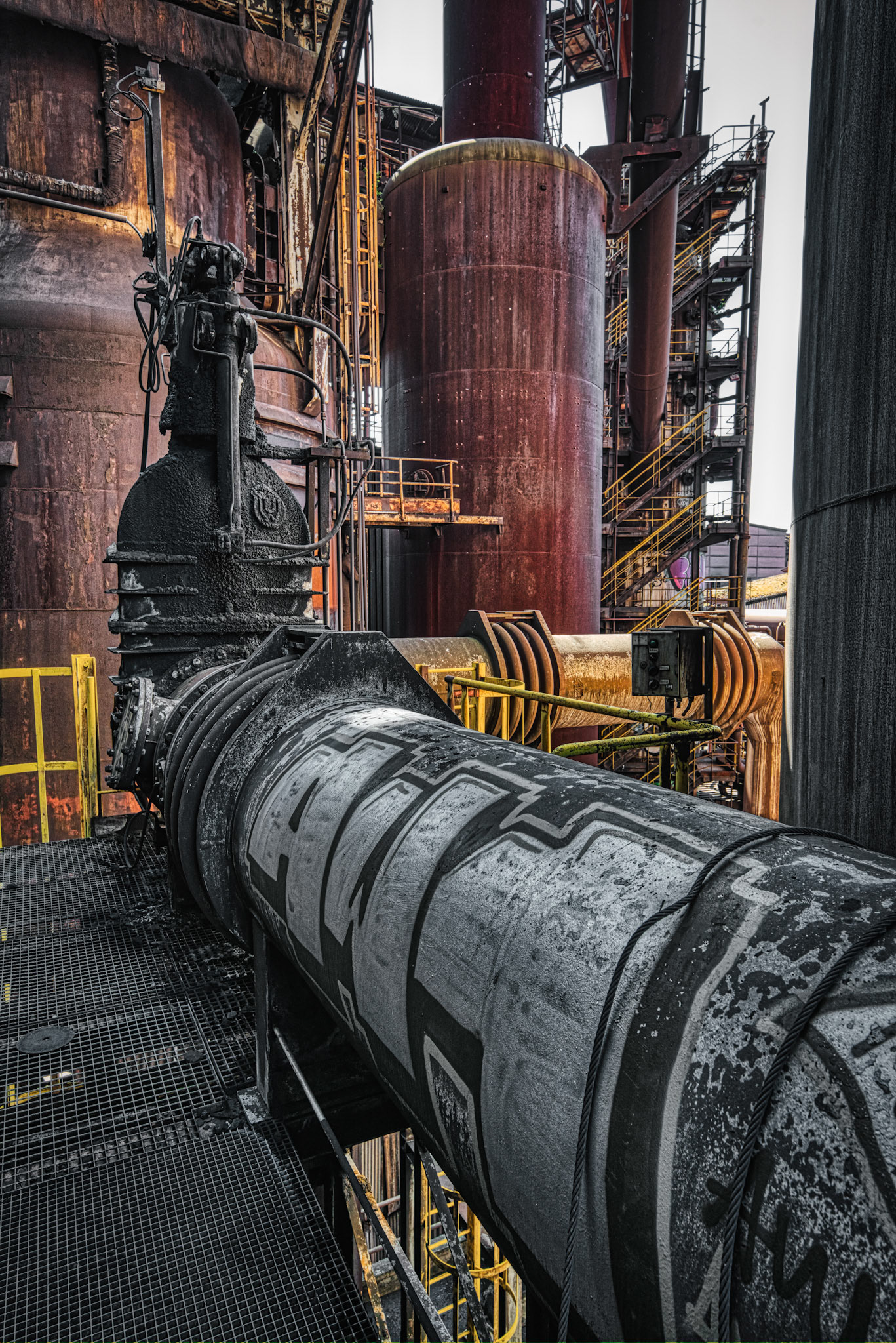
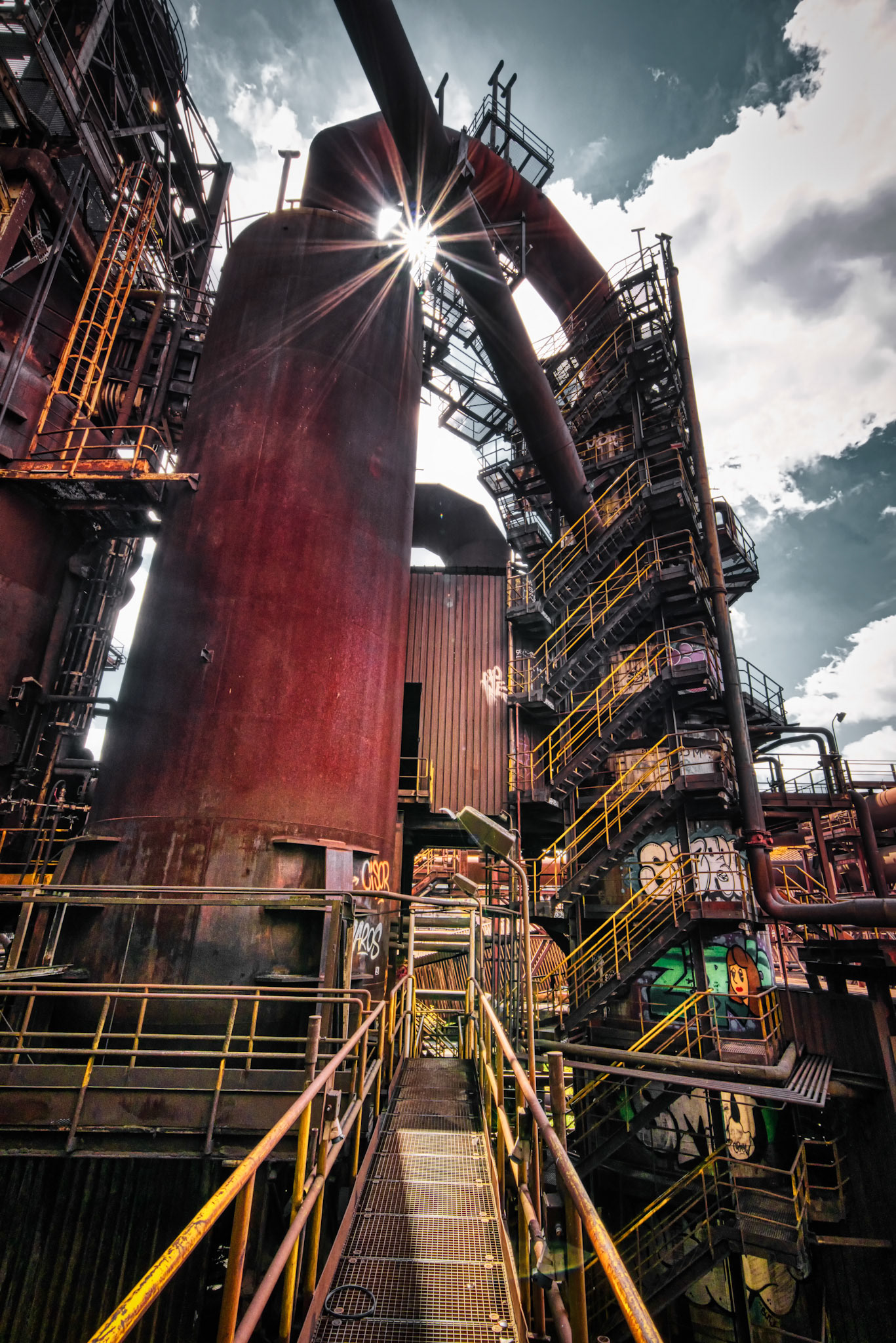
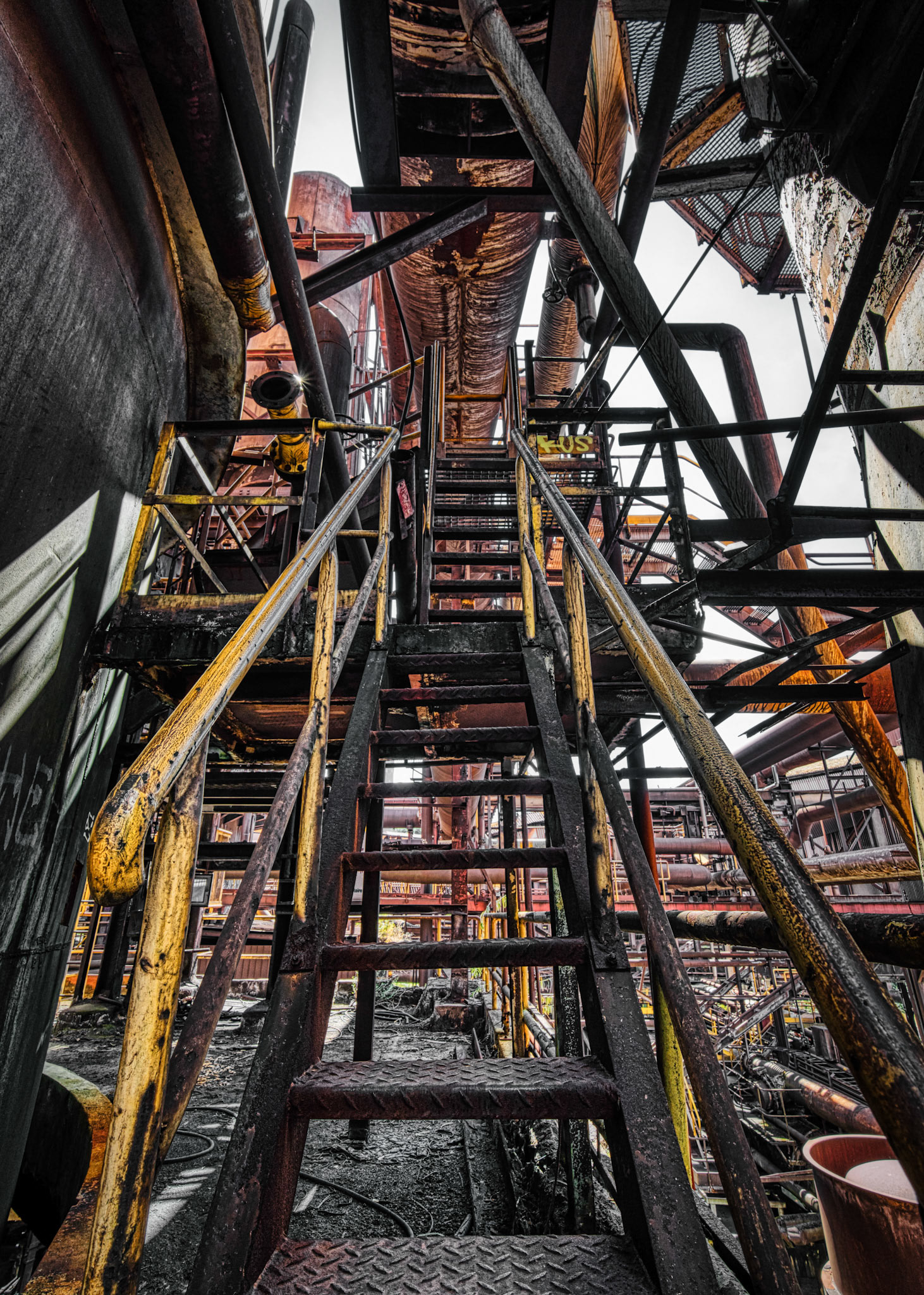
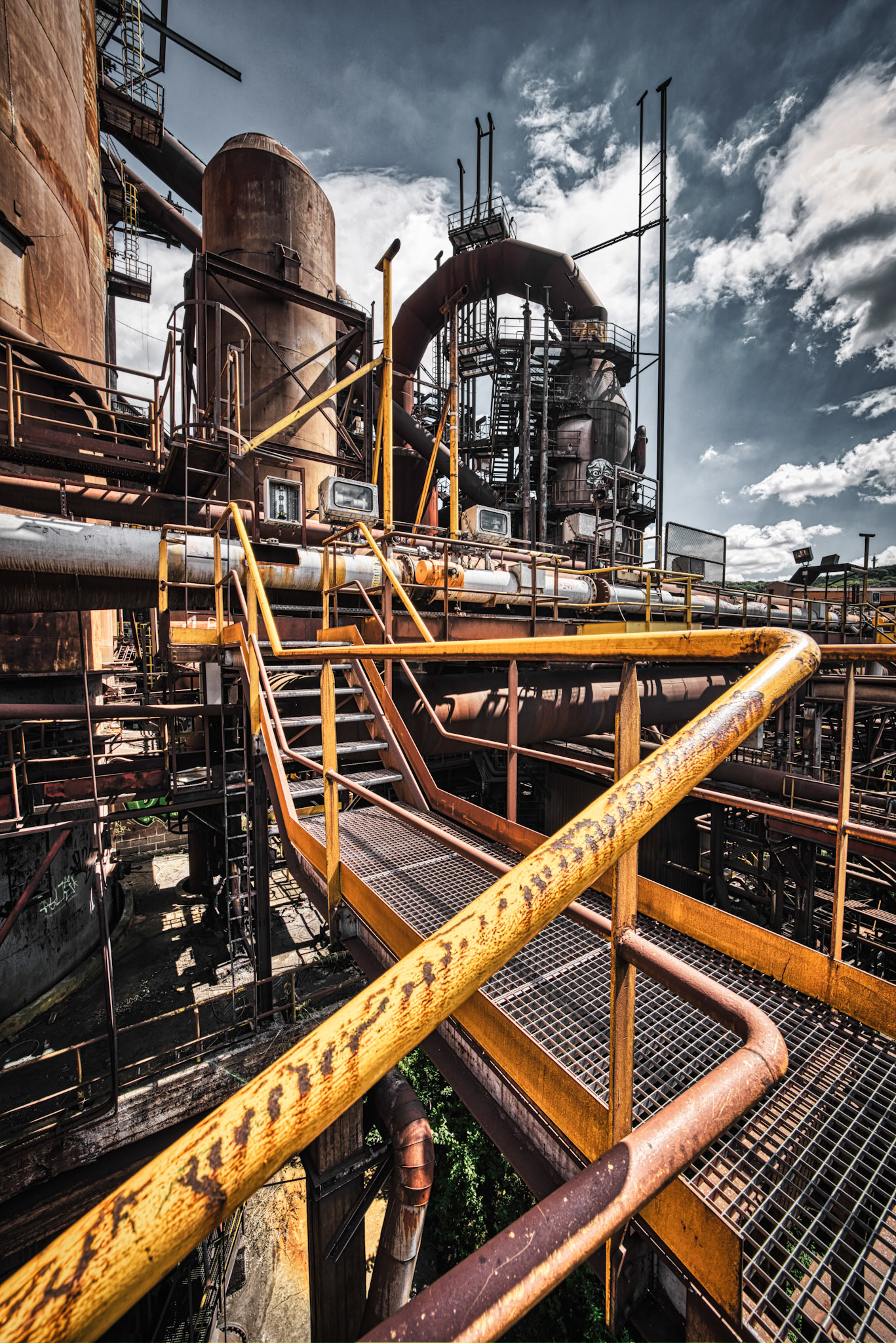
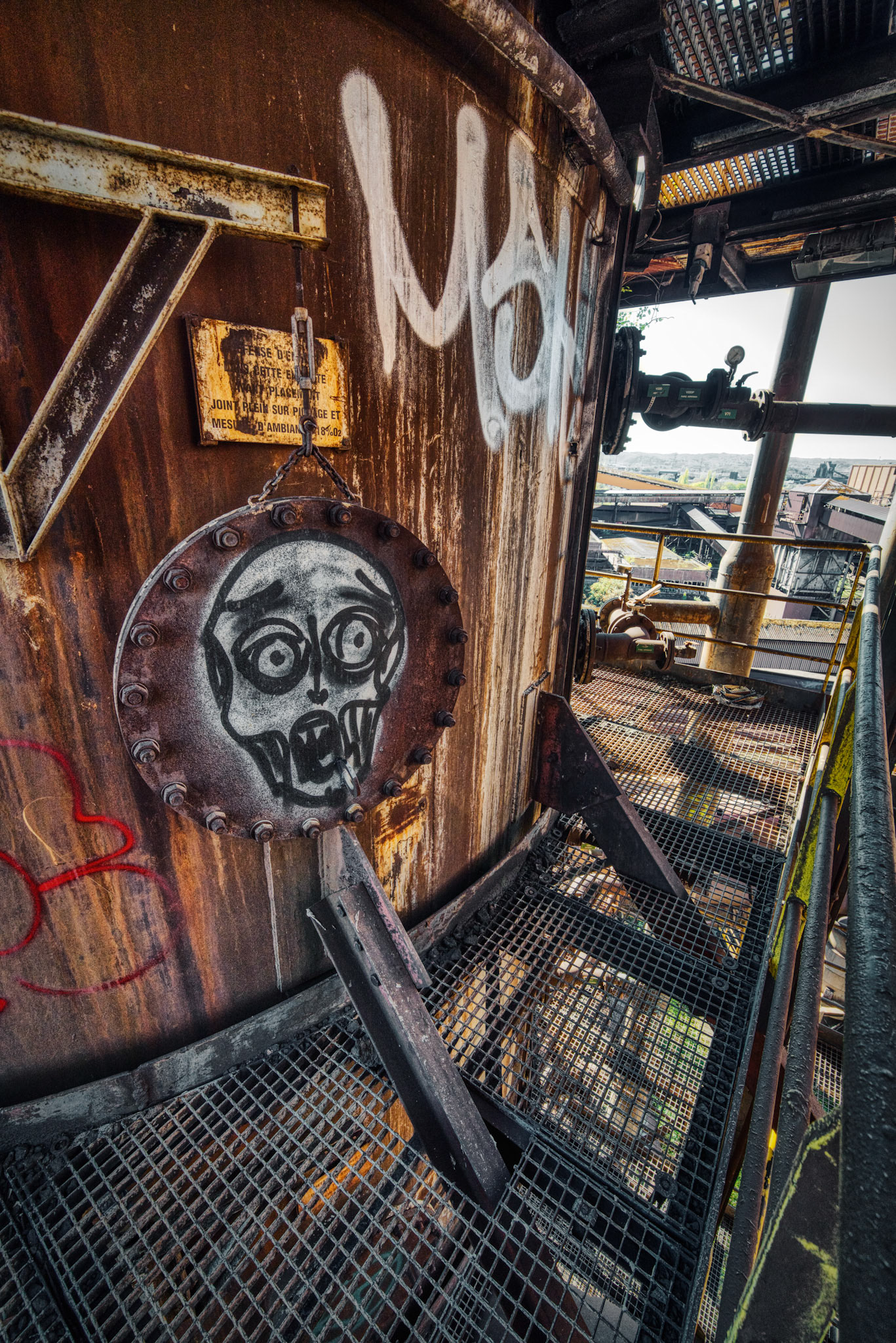
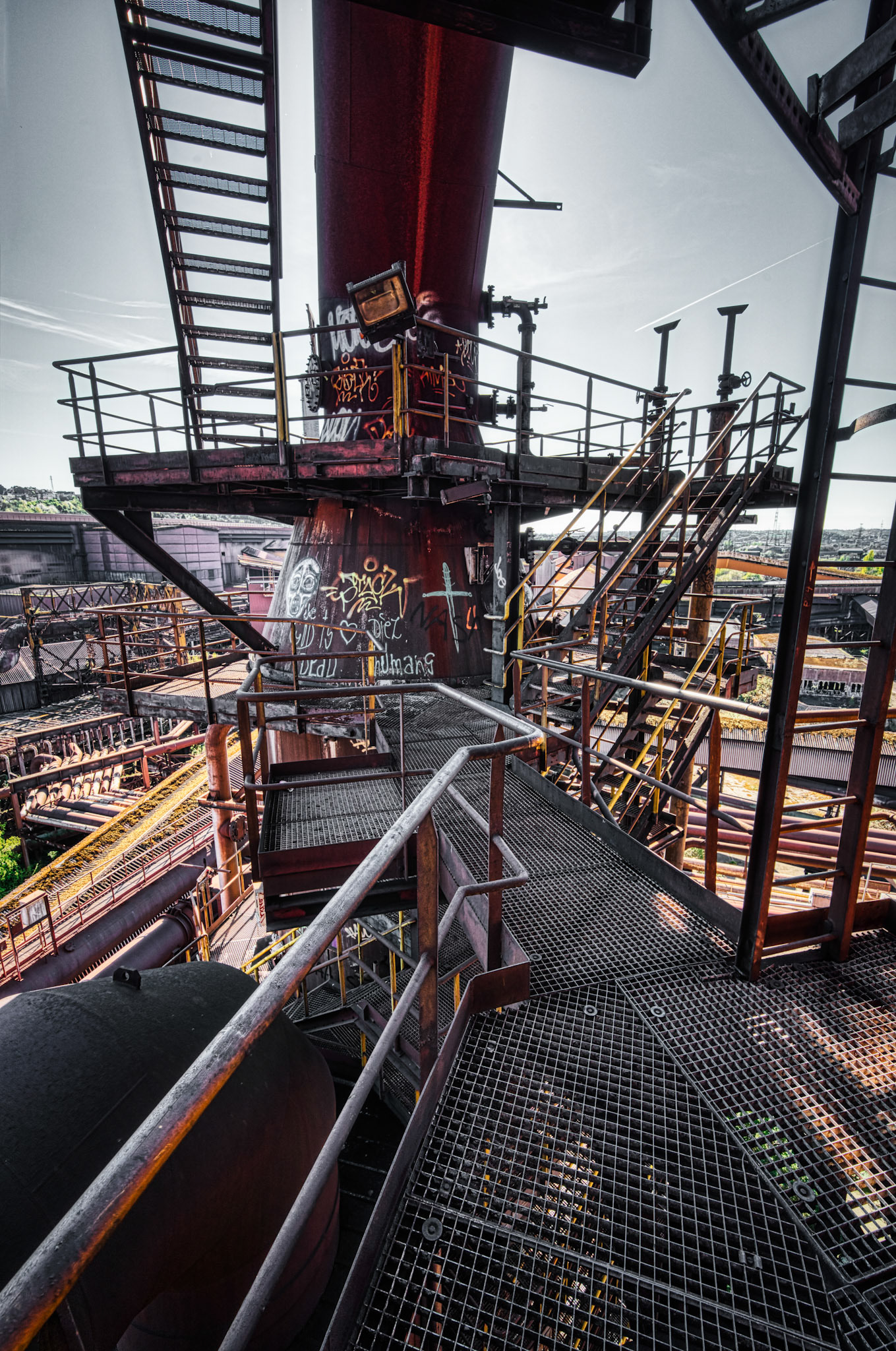
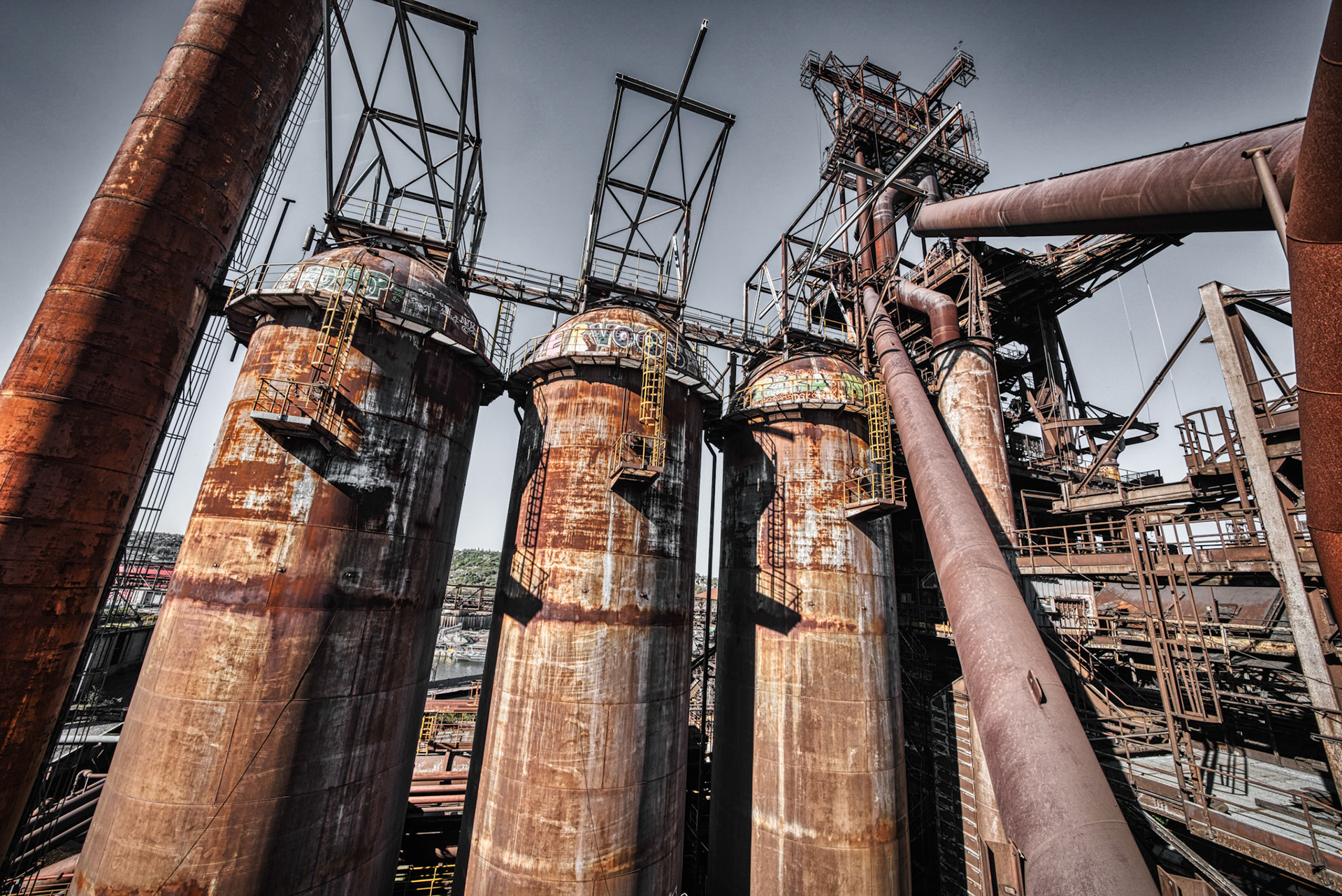
From the blast furnace cast house the pig iron will be poured into torpedo wagons. It is used to transport it from the blast furnace to the steelworks for further solidification or treatment. Torpedo wagons can be closed tightly and keep the iron in liquid condition up to 30 hours.
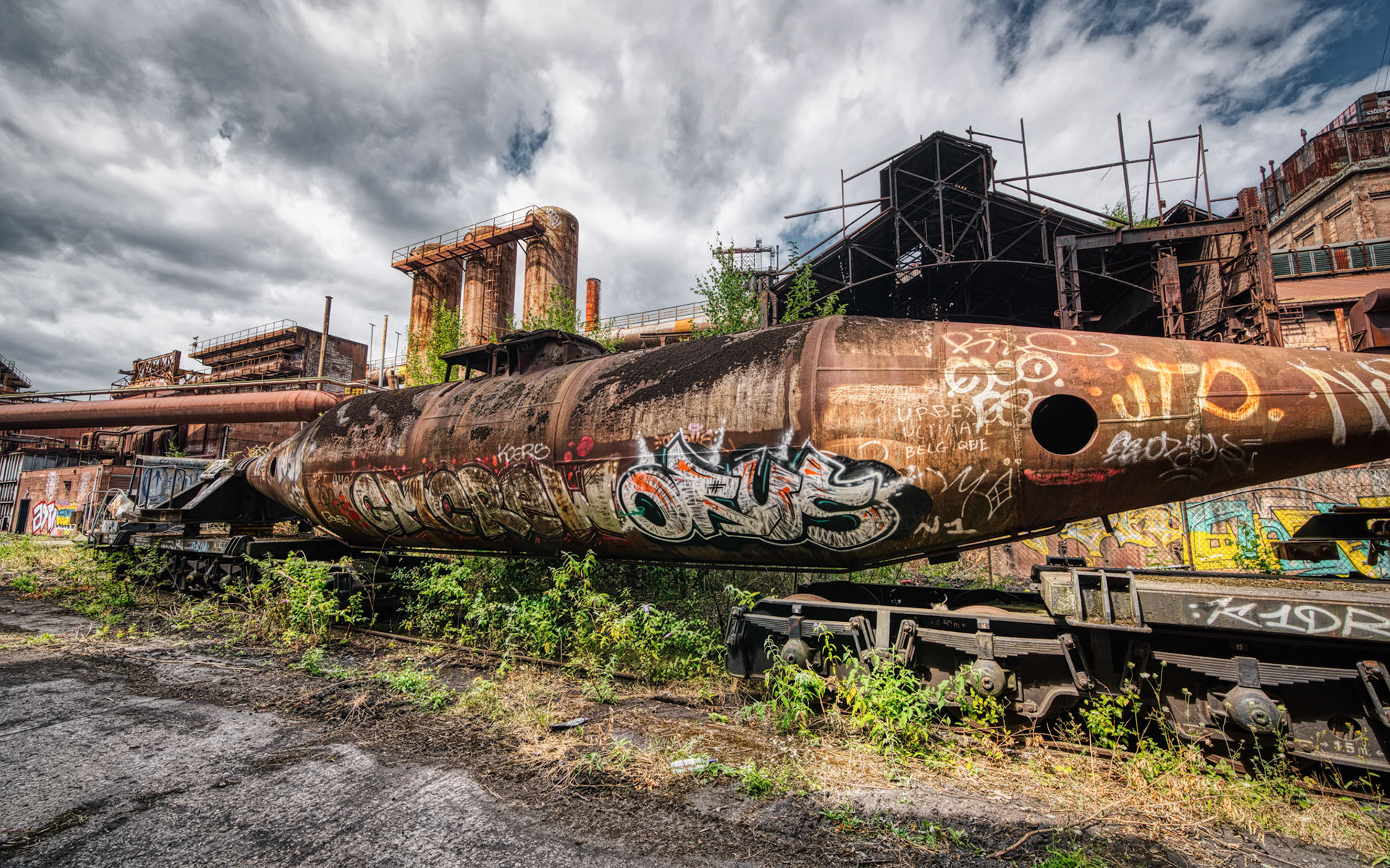
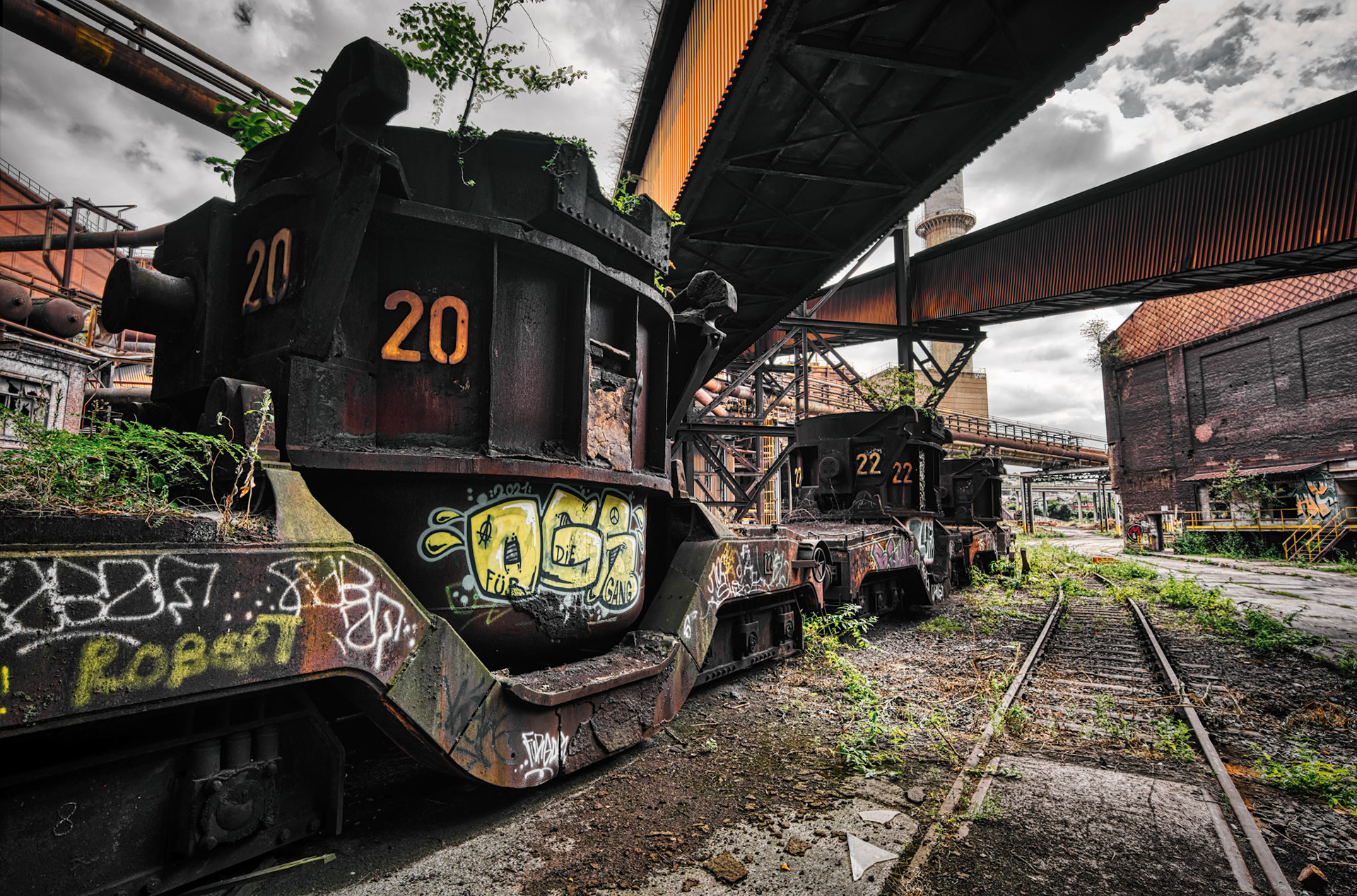